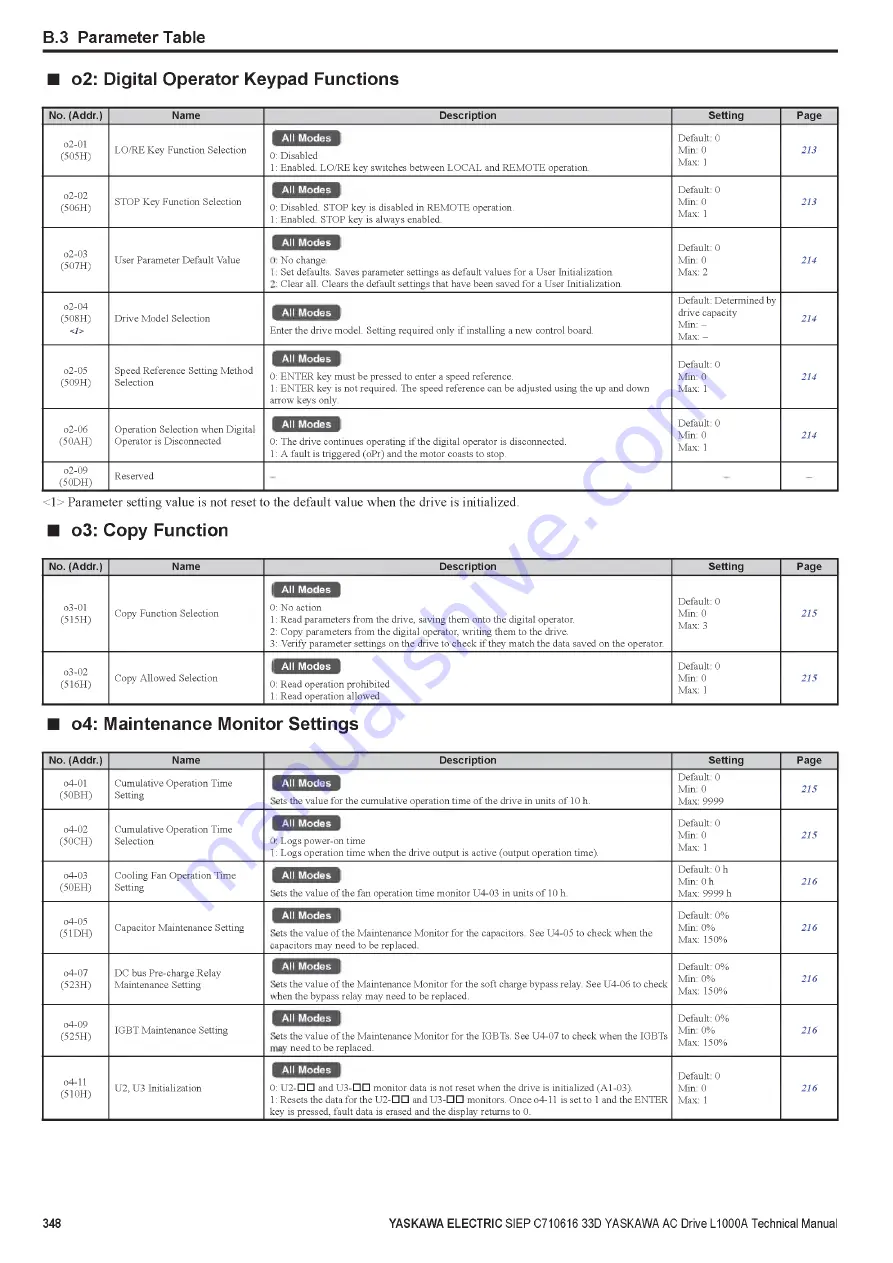
B.3 Parameter Table
■ o2: Digital Operator Keypad Functions
No. (Addr.)
Name
Description
Setting
Page
o2-01
(505H)
LO/RE Key Function Selection
0: Disabled
1: Enabled. LO/RE key switches between LOCAL and REMOTE operation.
Default: 0
Min: 0
Max: 1
213
o2-02
(506H)
STOP Key Function Selection
0: Disabled. STOP key is disabled in REMOTE operation.
1: Enabled. STOP key is always enabled.
Default: 0
Min: 0
Max: 1
213
o2-03
(507H)
User Parameter Default Value
N o change.
Set defaults. Saves parameter settings as default values for a User Initialization.
Clear all. Clears the default settings that have been saved for a User Initialization.
Default: 0
Min: 0
Max: 2
214
o2-04
(508H)
<1>
Drive M odel Selection
Enter the drive model. Setting required only if installing a new control board.
Default: Determined by
drive capacity
Min: -
Max: -
214
o2-05
(509H)
Speed Reference Setting Method
Selection
0: ENTER key must be pressed to enter a speed reference.
1: ENTER key is not required. The speed reference can be adjusted using the up and down
arrow keys only.
Default: 0
Min: 0
Max: 1
214
o2-06
(50AH)
Operation Selection when Digital
Operator is Disconnected
0: The drive continues operating if the digital operator is disconnected.
1: A fault is triggered (oPr) and the motor coasts to stop.
Default: 0
Min: 0
Max: 1
214
o2-09
(50D H )
Reserved
<1> Param eter setting value is not reset to the default value when the drive is initialized.
■ o3: Copy Function
No. (Addr.)
Name
|
Description
Setting
Page
o3-01
(515H)
Copy Function Selection
1
Default: 0
Min: 0
Max: 3
2 15
i All Modes
0
1
2
3
: N o action
: Read parameters from the drive, saving them onto the digital operator.
: Copy parameters from the digital operator, writing them to the drive.
: Verify parameter settings on the drive to check if they match the data saved on the operator.
o3-02
(516H)
Copy A llow ed Selection
1
Default: 0
Min: 0
Max: 1
2 15
1 All Modes
0: Read operation prohibited
1: Read operation allowed
■ o4: Maintenance Monitor Settings
No. (Addr.)
Name
|
Description
Setting
Page
o4-01
(50B H )
Cumulative Operation Time
Setting
ets the value fo r the cumulative operation tim e o f the drive in units o f 10 h.
Default: 0
Min: 0
Max: 9999
2 15
o4-02
(50CH)
Cumulative Operation Time
Selection
: Logs power-o
: Logs operatio
1
n time
n time when the drive output is active (output operation time).
Default: 0
Min: 0
Max: 1
2 15
o4-03
(50EH)
Cooling Fan Operation Time
Setting
ets the value o f
1
the fan operation tim e monitor U4-03 in units o f 10 h.
Default: 0 h
Min: 0 h
Max: 9999 h
2 1 6
o4-05
(51DH)
Capacitor Maintenance Setting
ets the value o f
apacitors may n
ШШ/ШШШЯШЯШШ
I
the Maintenance Monitor for the capacitors. See U 4-05 to check when the
eed to be replaced.
Default: 0%
Min: 0%
Max: 150%
2 1 6
o4-07
(523H)
DC bus Pre-charge Relay
Maintenance Setting
ets the value o f
hen the bypass
Ш Н Н Н ^ Н Н 1
the Maintenance Monitor for the soft charge bypass relay. See U 4-06 to check
relay may need to be replaced.
Default: 0%
Min: 0%
Max: 150%
2 1 6
o4-09
(525H)
IGBT Maintenance Setting
ets the value o f
ay need to be r
ШШ/ШШ/ШЯШШ
I
' the Maintenance Monitor for the IGBTs. See U 4-07 to check when the IGBTs
eplaced.
Default: 0%
Min: 0%
Max: 150%
2 1 6
o4-11
(510H)
U 2, U3 Initialization
0
1
k
: U 2 - D D and U
: R esets the dat
ey is pressed, f
ИНННННН^Ш Н 1
J 3 -D D monitor data is not reset when the drive is initialized (A1-03).
a for the U 2 - D D and U 3 - D D monitors. Once o4-11 is set to 1 and the ENTER
ault data is erased and the display returns to 0.
Default: 0
Min: 0
Max: 1
2 1 6
348
YASKAWA ELECTRIC SIEP C710616 33D YASKAWA AC Drive L1000A Technical Manual