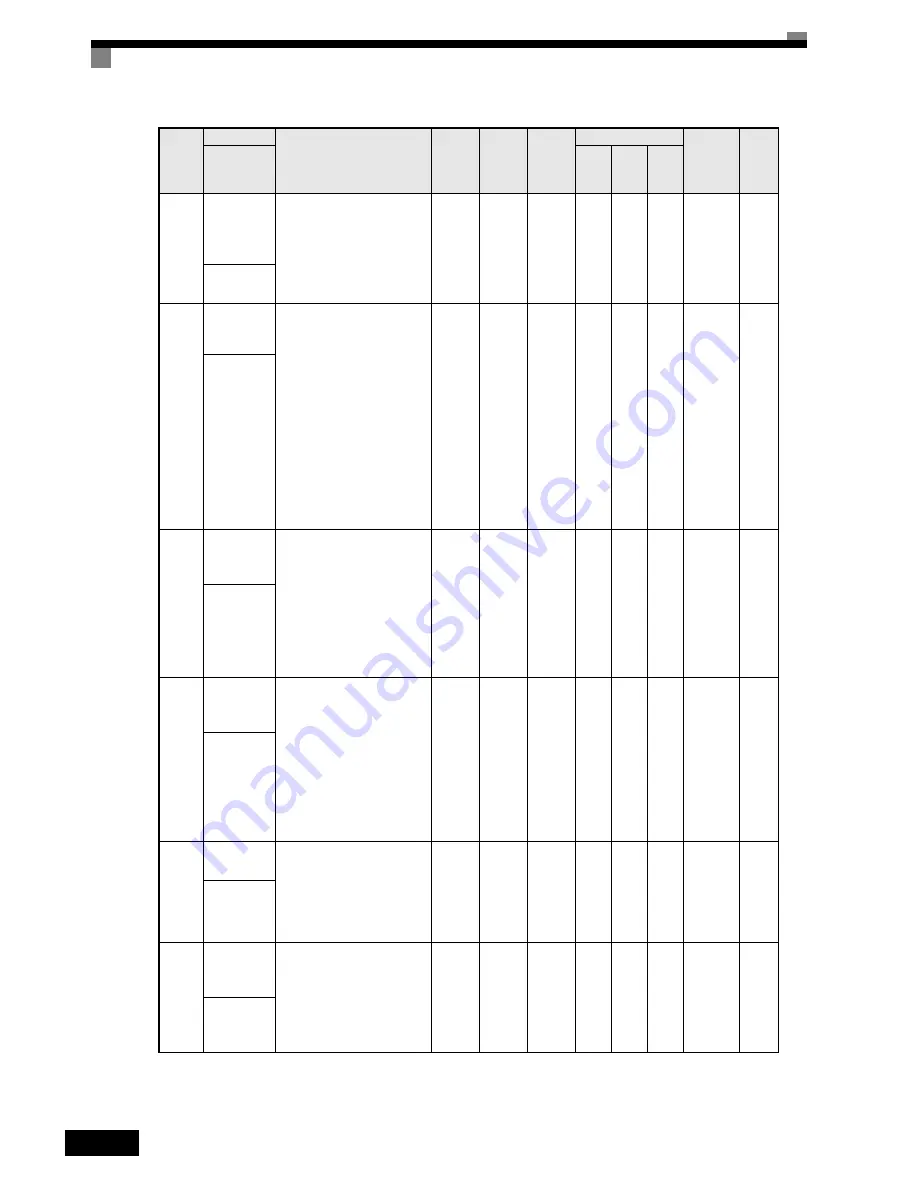
5
-58
L2-02
Momentary
power
loss
ridethru
time
Ridethrough
time, when
Momentary
Power Loss
Selection
(L2-01) is set to 1,
in
units of seconds.
0
to 2.0
0.1
s
*1
No
A
A
A
486H
6-52
PwrL
Ride-
thru
t
L2-03
Min.
base-
block
time
Sets
the Inverter's minimum
baseblock
time in units of
one
second, when the
Inverter
is restarted after
power
loss ridethrough.
Sets
the time to approxi-
mately
0.7 times the motor
secondary
circuit time con-
stant.
When
an overcurrent or
overvoltage
occurs when
starting
a speed search or DC
injection
braking, increase
the
set values.
0.1
to
5.0
0.1
s
*1
No
A
A
A
487H
6-52
6-53
PwrL
Base-
block
t
L2-04
Voltage
recovery
time
Sets
the time required to
return
the Inverter output
voltage
to normal voltage at
the
completion of a speed
search,
in units of one sec-
ond.
Sets
the time required to
recover
from 0 V to the max-
imum
voltage.
0.0
to
5.0
0.3
s
*1
No
A
A
A
488H
6-52
6-53
PwrL
V/F
Ramp
t
L2-05
Undervolt-
age
detec-
tion
level
Sets
the main circuit under-
voltage
(UV) detection level
(main
circuit DC voltage) in
V
units.
Usually
setting is not neces-
sary.
Insert
an AC reactor in the
Inverter
input side to lower
the
main circuit undervolt-
age
detection level.
150
to
210
*2
190
V
*2
No
A
A
A
489H
6-52
PUV
Det
Level
L2-06
KEB
decel-
eration
time
Sets
in seconds the time
required
to decelerate from
the
speed where the deceler-
ation
at momentary power
loss
command (KEB) is
input
to zero speed.
0.0
to
200.0
0.0
s
No
A
A
A
48AH
-
KEB
Fre-
quency
L2-07
Momentary
recovery
time
Set
in seconds the time to
accelerate
to the set speed
after
recovery from a
momentary
power loss.
0.0
to
25.5
0
s
*3
No
A
A
A
48BH
-
UV
RETURN
TIME
Param-
eter
Number
Name
Description
Setting
Range
Factory
Setting
Change
during
Opera-
tion
Control Methods
Register Page
LCD
Display
V/f
V/f
with
PG
Open
Loop
Summary of Contents for SYSDRIVE 3G3RV
Page 1: ...USER S MANUAL SYSDRIVE 3G3RV High function General purpose Inverters Cat No I532 E1 1...
Page 36: ...1 22...
Page 106: ...3 14...
Page 126: ...4 20...
Page 216: ...5 90...
Page 388: ...7 26...