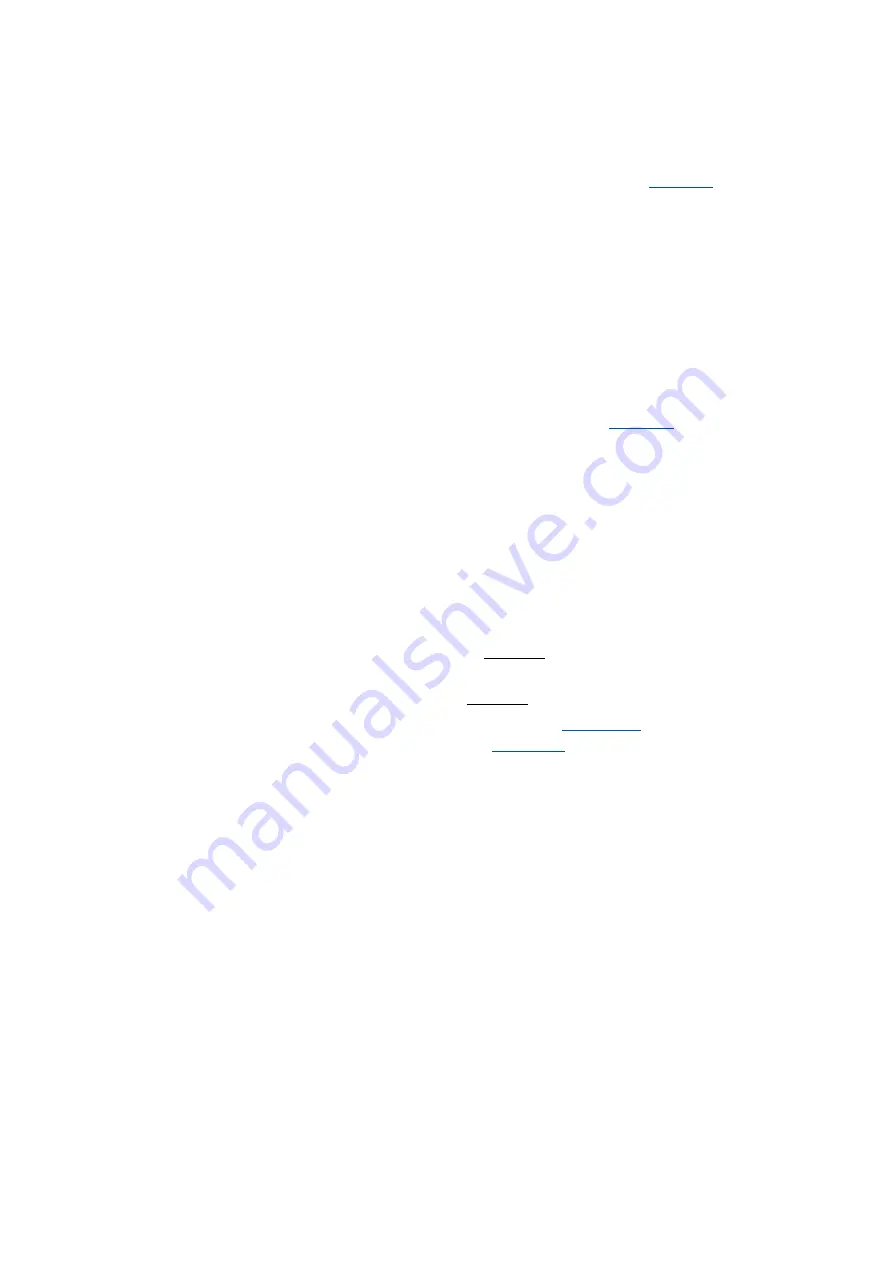
5
Motor control (MCTRL)
5.1
Motor selection/Motor data
144
Lenze · 8400 HighLine · Reference manual · DMS 12.0 EN · 06/2017 · TD23
_ _ _ _ _ _ _ _ _ _ _ _ _ _ _ _ _ _ _ _ _ _ _ _ _ _ _ _ _ _ _ _ _ _ _ _ _ _ _ _ _ _ _ _ _ _ _ _ _ _ _ _ _ _ _ _ _ _ _ _ _ _ _ _
Selection of the identification mode
From version 10.00.00 onwards
, two identification modes are available in
:
• "1: Basic identification" (previous mode)
• Only for asynchronous motors
• Duration approx. 30 s
• "2: extended identification"
• Stands out due to increased accuracy of the determined motor parameters.
• Also supports synchronous motors and asynchronous motors with a power of more than 11
kW.
• Duration approx. 80 s
Tip!
In the Lenze setting, a setting of "0: automatic" is selected in
. This setting ensures
that the inverter automatically selects the optimum procedure for motor parameter
identification.
Preconditions for executing the motor parameter identification
• The motor parameter identification must be carried out when the motor is cold!
• The load machine may remain connected. Holding brakes, if present, may remain in the braking
position.
• In case of a synchronous motor:
• The shaft must be able to rotate freely (must not be locked).
• An identification is only possible with the extended motor parameter identification.
• For an asynchronous motor from a power of 11 kW:
An identification is only possible with the extended motor parameter identification.
• The inverter has to be ready for enable (has to be in the "
Inhibit the inverter if it is enabled, e.g. via the
device command or a LOW signal at
the X4/RFR terminal.
• The motor has to be at standstill.