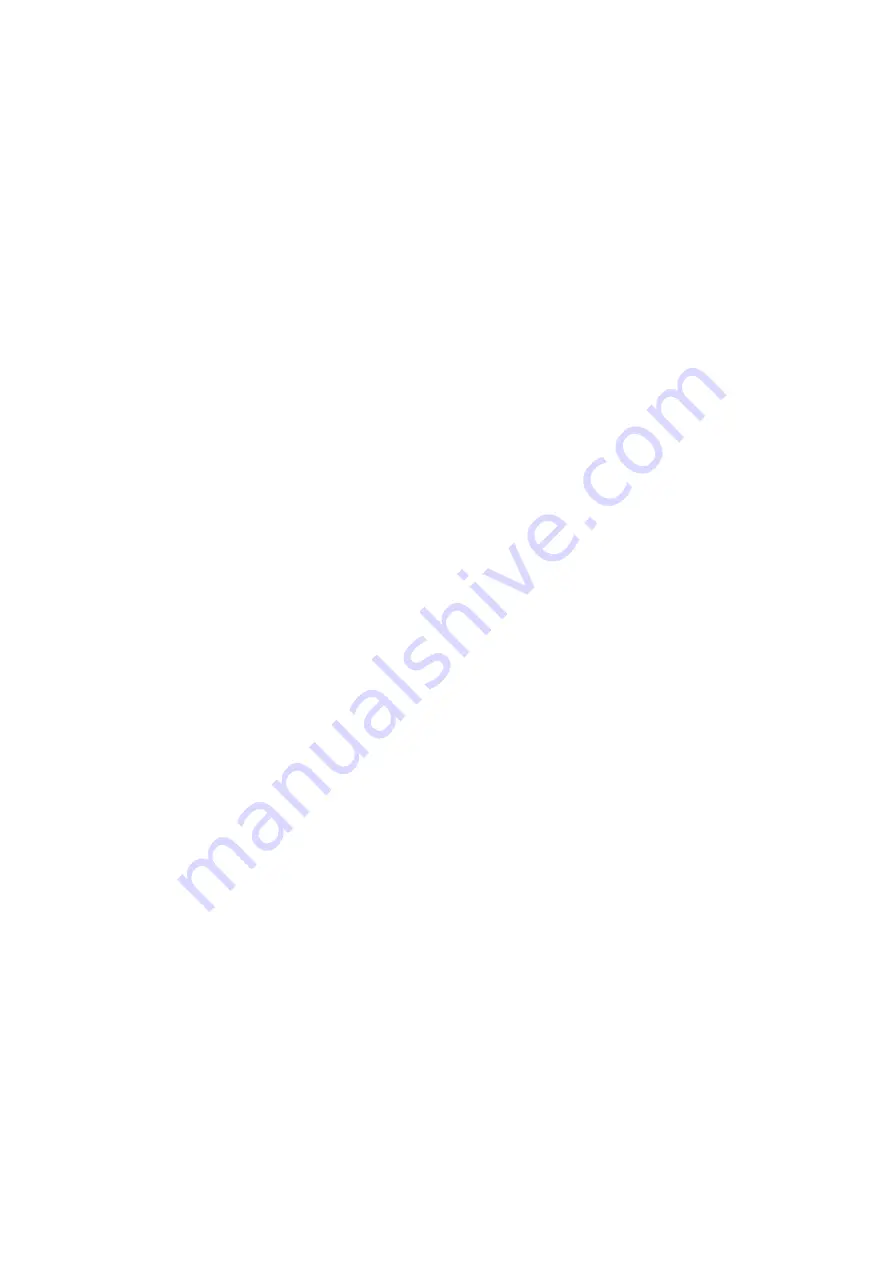
ME0392-4C
5.4 Receiving and Forwarding of I/O Signals Necessary for Operation ····· 5-13
5.5 I/O Port ·················································································· 5-14
5.6 Position Data (Position Table) ····················································· 5-17
5.7 Programming ·········································································· 5-18
5.7.1 SEL command word list ·········································································· 5-18
5.7.2 Symbol extension ·················································································· 5-18
5.7.3 Step comment number of characters ························································· 5-18
5.7.4 Position data comment ··········································································· 5-18
5.7.5 SEL data list ························································································· 5-19
5.7.6 Memory map ························································································ 5-20
5.8 Types of Operations ································································· 5-22
5.9 How to Operate ······································································· 5-23
5.9.1 Auto start upon power on ········································································ 5-23
5.9.2 Starting a program by specifying its program number ···································· 5-25
5.10 ELECYLINDER Operation ························································· 5-27
5.10.1 Specification ························································································· 5-28
5.10.2 Applicable version·················································································· 5-28
5.10.3 ELECYLINDER control system ································································· 5-29
5.10.4 Input and output signals and features of EC connection unit ··························· 5-31
5.10.5 Assignment and operation system of EC signals · ········································ 5-37
5.10.6 Timing for input and output signals ···························································· 5-39
5.10.7 Maintenance bit output for predictive maintenance ······································· 5-40
5.10.8 Configuration example ············································································ 5-41
5.10.9 Caution ······························································································· 5-47
5.10.10 List of related parameters ······································································ 5-48
5.10.11 Related errors ····················································································· 5-51
Chapter 6 Field Network, PIO, SIO
6.1 Interface Specifications ····························································· 6-1
6.1.1 I/O Slot ································································································ 6-3
6.1.2 PIO/SIO/SCON extension unit, PIO unit ····················································· 6-13
6.2 Functional Specifications ··························································· 6-14
6.2.1 List of applicable devices ········································································ 6-14
6.2.2 Parallel I/O and remote I/O ······································································ 6-15
6.2.3 I/O Ports and reading and writing of data ···················································· 6-17
ME0392-4C
6.3 Parameter Configuration ···························································· 6-53
6.3.1 Basic setting ························································································· 6-53
6.3.2 Other settings ······················································································· 6-57
6.3.3 Examples of parameter settings at delivery ················································· 6-58
6.3.4 Example of use of each network and parameter ··········································· 6-60
6.4 Caution ·················································································· 6-101
6.4.1 Network setting files ··············································································· 6-101
6.4.2 PROFIBUS-DP ····················································································· 6-102
6.4.3 EtherCAT ····························································································· 6-103
6.4.4 EtherNet/IP ·························································································· 6-103
6.5 Example of Connectivity Setting ·················································· 6-104
6.5.1 Downloading setting file for network (ESI file) ·············································· 6-104
6.5.2 Sysmac studio startup and PLC communication connectivity ·························· 6-105
6.5.3 Installing setting file for network (ESI file)···················································· 6-106
6.5.4 Setup of EtherCAT network configuration ··················································· 6-109
6.5.5 Changing PDO mapping setting ································································ 6-113
6.5.6 Data Rransfer to PLC ············································································· 6-118
Chapter 7 6-axis Cartesian Robot
7.1 Guideline of Coordinate Systems ················································ 7-1
7.1.1 List of coordinate systems ······································································· 7-1
7.1.2 Applicable robots ··················································································· 7-2
7.1.3 Specific axis coordinate system ································································ 7-3
7.1.4 Orthogonal coordinate system ·································································· 7-5
7.2 Caution When Using Orthogonal Coordinate System Features ·········· 7-10
7.2.1 Relation between axis numbers and axis patterns ········································ 7-10
7.2.2 CP operation ························································································ 7-11
7.2.3 PTP operation ······················································································· 7-13
7.2.4 Wrist form and singularity ········································································ 7-15
7.2.5 Position data ························································································· 7-17
7.2.6 Coordinate system definition data ····························································· 7-19
7.2.7 Positioning in each coordinate system ······················································· 7-21
7.2.8 Jog movement ······················································································ 7-25
7.2.9 Simple contact check zone ······································································ 7-28
Summary of Contents for R-unit RSEL
Page 2: ......
Page 5: ...ME0392 4C 2 Quick Start Guide Japanese Only ...
Page 32: ...Actuator Coordinate System Intro 18 ME0392 4C 2 Slider type 3 Table type 0 0 0 0 ...
Page 50: ...Chapter 1 RSEL System 1 4 Installation 1 13 ME0392 4C ...
Page 244: ...Chapter 4 Unit connection Installation and Wiring 4 5 PIO Circuit 4 32 ME0392 4C ...
Page 316: ...Chapter 5 Operation 5 10 ELECYLINDER Operation 5 52 ME0392 4C ...
Page 438: ...Chapter 6 Field Network PIO SIO 6 5 Example of Connectivity Setting 6 120 ME0392 4C ...
Page 532: ...10 6 Servo Gain Adjustment 10 90 10 7 Parameter Configuration Advanced Use 10 93 ...
Page 638: ...Chapter 10 Parameter 10 7 Parameter Configuration Advanced Use 10 106 ME0392 4C ...
Page 838: ...Chapter 14 Warranty 14 Warranty 14 3 ME0392 4C ...
Page 843: ......
Page 844: ......