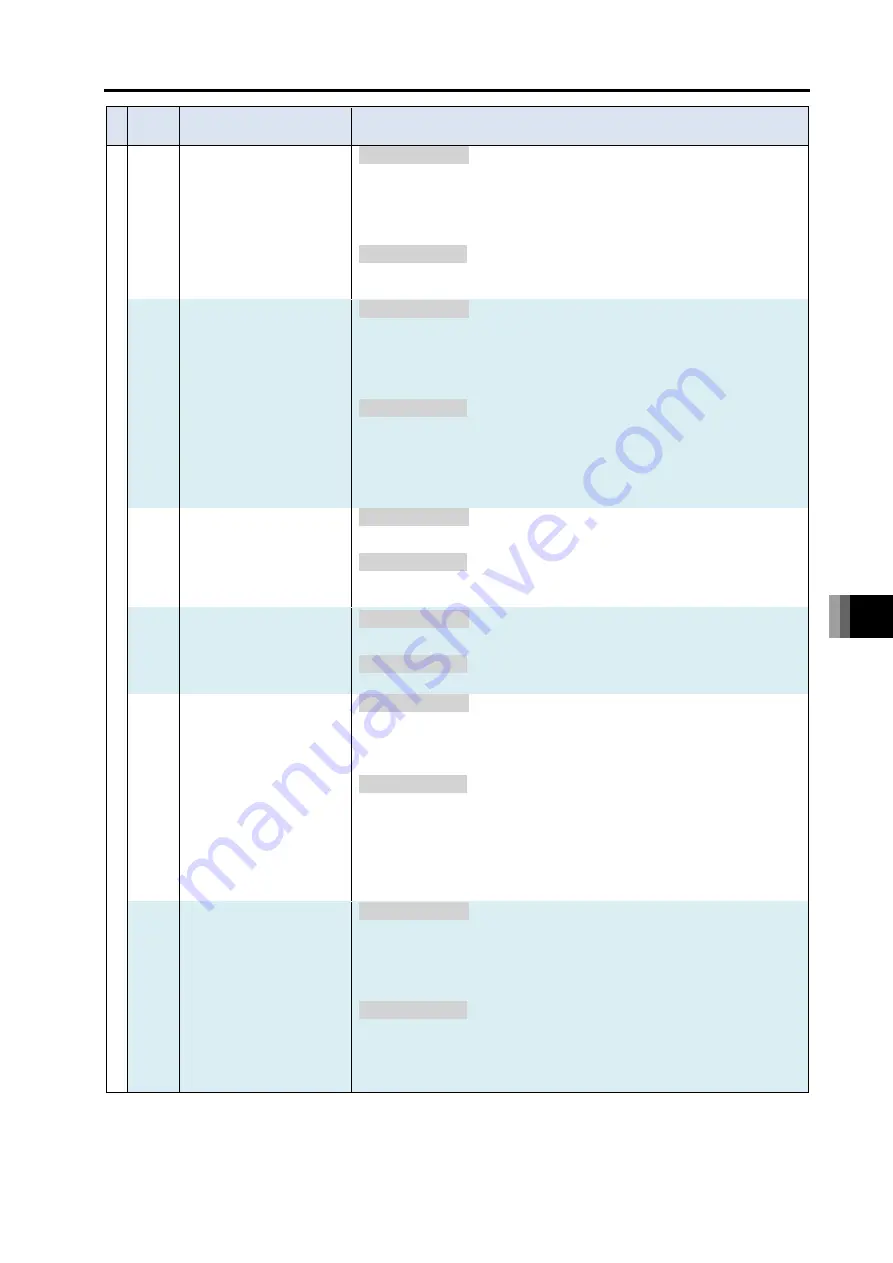
Chapter
11 T
roubleshooting
11.3 Error List
11-43
ME0392-4C
Error
No.
Error name
Content and Cause /
Countermeasure
O
per
at
io
n-
can
cel
lat
ion
478
Driver unit actual speed
exceeded
[Content & Cause]
1) An external force was applied to an actuator
2) The sliding resistance on an actuator is high
3) The brake cannot be released
4) Malfunction of encoder
5) Malfunction of driver unit
[Countermeasure]
1) Revise condition of assembly
2) If there is no problem with the payload, cut off the power and check
sliding resistance by hand
3) Check condition of brake cable wiring, and then brake operation check
manually
4) Replace the motor unit (encoder)
5) Replace driver unit
479
Slave driver alarm
detection
[Content & Cause]
1) An alarm on the driver was detected
[Countermeasure]
1) The error numbers on the driver unit should be display in the detailed
information Info1.
Check the detail of the applicable alarm code in “11.4 Alarm Codes of
Driver Unit” in order to take a counteraction.
47A
Positioning completion
time-out error
[Content & Cause]
1) An external force was applied to an actuator
2) The sliding resistance on an actuator is high
3) The brake cannot be released
4) Malfunction of encoder
5) Malfunction of driver unit
6) Contact error at connector of actuator connection cable
7) Cable breakage on actuator connection cable
[Countermeasure]
1) Revise condition of assembly
2) If there is no problem with the payload, cut off the power and check
sliding resistance by hand
3) Check condition of brake cable wiring, and then brake operation check
manually
4) Replace the motor unit (encoder)
5) Replace driver unit
6) Check actuator connection cable connection status and connect again
7) Replace the actuator connection cable
47B
Coordinate system
number error
[Content & Cause]
1) A coordinate system number out of the range was indicated in a SEL
command
• Out of Work Coordinate System No 0 to 15
• Out of Tool Coordinate System No. 0 to 15
2) Offset of Work Coordinate System No. 0 or Tool Coordinate System No.
0 was changed or inquired
[Countermeasure]
1) Indicate a coordinate number in the range in a SEL command
• Work Coordinate System No 0 to 15
• Tool Coordinate System No. 0 to 15
2) Offset of Work Coordinate System No. 0 or Tool Coordinate System No.
0 should not be changed or inquired
11.3 Error List
ME0392-4C
11-44
Error
No.
Error name
Content and Cause /
Countermeasure
O
per
at
io
n-
can
cel
lat
ion
47C
Coordinate system type
error
[Content & Cause]
1) A wrong number (other than 2) was indicated when indicating the
coordinate system type in Protocol B
0: Work Coordinate System, 1: Tool Coordinate System
2) Malfunction on SEL unit
[Countermeasure]
1) Check the sending message and indicate the number correctly
2) Replace SEL unit
47D
Coordinate system data
change prohibition error
during servo use
[Content & Cause]
1) Work coordinate system number or tool coordinate system number in
use of the servo system was attempted to be changed
2) Work coordinate system or tool coordinate system offset in use of the
servo system was attempted to be changed
[Countermeasure]
1) Correct the SEL program so it is not necessary to change the
coordinate system number selected during the axis operation
2) Correct the SEL program so it does not change the offset in the work
coordinate system or tool coordinate system currently selected during
the axis operation
47E
Simple interference
check zone entry
detection
[Content & Cause]
1) Irruption to the simple interference check zone was detected
[Countermeasure]
1) Change the operation conditions or operation patterns to avoid irruption
to the simple interference check zone
47F
Axes group indication
error
[Content & Cause]
1) The indicated axes group is invalid
[Countermeasure]
1) A valid axes group should be indicated
480
Out of target track range
error
[Content & Cause]
1) Position data setting error
2) Position data setting error
3) Position data setting error
[Countermeasure]
1) Check the position number in the step that the error occurred and set it
in the operation range of the orthogonal coordinate system
2) Check the position number in the step that the error occurred and set it
in the operation range of the orthogonal coordinate system
3) Check the position number in the step that the error occurred and set it
out of the CP operation limited band
481
Multi-slider too close
detection error
[Content & Cause]
1) Multiple slider servo command position excess approach area irruption
was detected
2) Multiple slider servo current position excess approach area irruption
was detected
[Countermeasure]
1) Perform the following operation after escaping from the over-
approaching position by jog, etc.
2) Perform the following operation after escaping from the over-
approaching position by jog, etc.
Summary of Contents for R-unit RSEL
Page 2: ......
Page 5: ...ME0392 4C 2 Quick Start Guide Japanese Only ...
Page 32: ...Actuator Coordinate System Intro 18 ME0392 4C 2 Slider type 3 Table type 0 0 0 0 ...
Page 50: ...Chapter 1 RSEL System 1 4 Installation 1 13 ME0392 4C ...
Page 244: ...Chapter 4 Unit connection Installation and Wiring 4 5 PIO Circuit 4 32 ME0392 4C ...
Page 316: ...Chapter 5 Operation 5 10 ELECYLINDER Operation 5 52 ME0392 4C ...
Page 438: ...Chapter 6 Field Network PIO SIO 6 5 Example of Connectivity Setting 6 120 ME0392 4C ...
Page 532: ...10 6 Servo Gain Adjustment 10 90 10 7 Parameter Configuration Advanced Use 10 93 ...
Page 638: ...Chapter 10 Parameter 10 7 Parameter Configuration Advanced Use 10 106 ME0392 4C ...
Page 838: ...Chapter 14 Warranty 14 Warranty 14 3 ME0392 4C ...
Page 843: ......
Page 844: ......