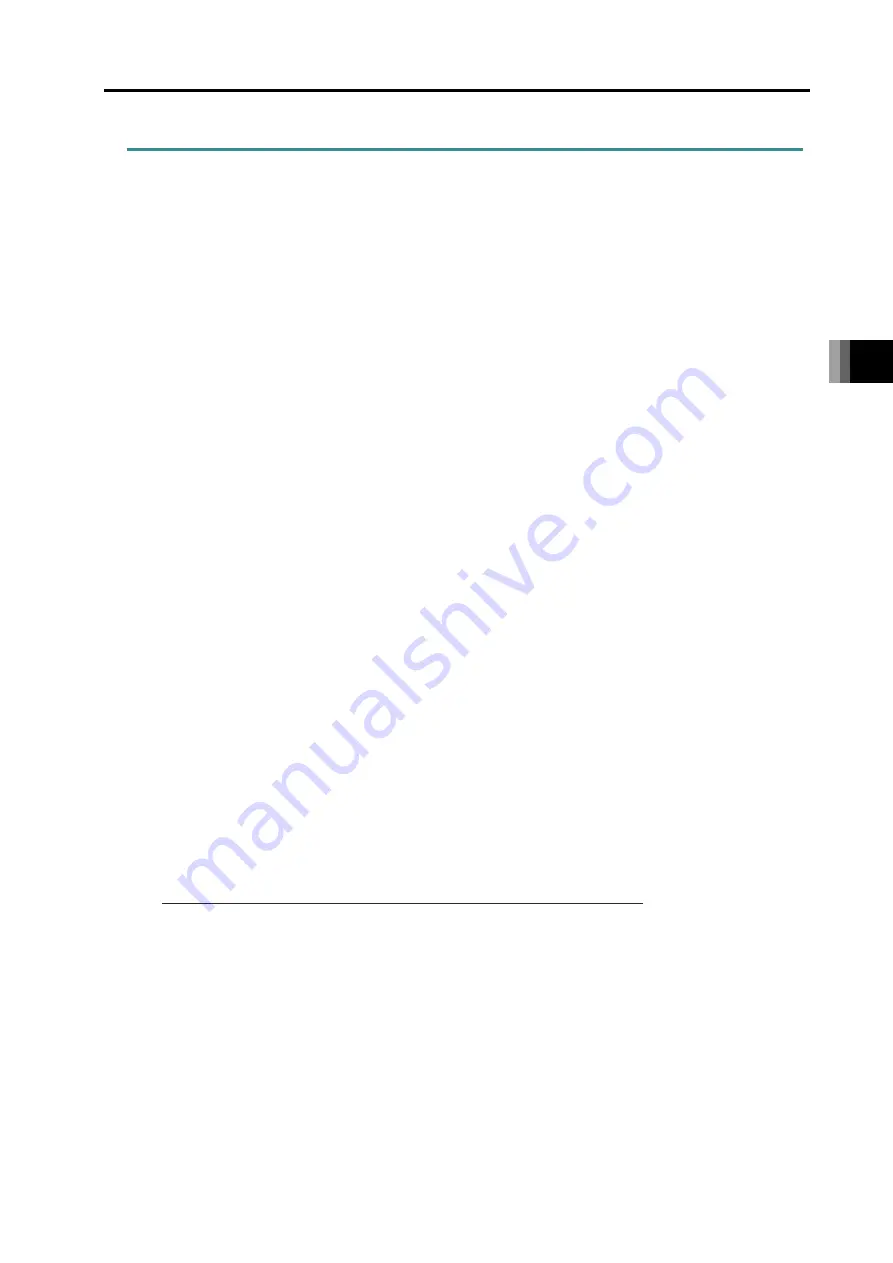
Chapter 5 Operation
5.10 ELECYLINDER Operation
5-46
ME0392-4C
[4] Setting to EC
Select Menu → EC (E) → Teaching Tool (T) in the PC software and the following EC teaching
tool should be launched. Only the identified EC should be connected.
* Teaching of positions, parameter change and alarm list check should be available in the
same manner as the PC teaching software for RCEC.
[5] Trial operation
In MANU Mode, ELECYLINDER would not accept any command on the input and output
ports.
If you would like to have a trial run on the input and output ports in MANU Mode, establish
the setting in the PC teaching software or a teaching pendant (TB-02/03).
●
When Operating in PC Teaching Software
Select "Permit EC I/O Command" from the dropdown list in the toolbar.
By doing so, a trial run on the input and output ports should become available in MANU Mode.
Toolbar select
Contents
Prohibit EC I/O
Command
I/O indication disabled
Select this when teaching operation.
Permit EC I/O
Command
I/O indication enabled
Select this when trial run
5.10 ELECYLNDER Operation
ME0392-4C
5-47
5.10.9 Caution
The caution notes when operating ELECYLINDER with an EC connection unit (RCON-EC-4)
being connected to the SEL unit.
(1)
ELECYLINDER connected to RSEL is not capable for use in the single solenoid system.
Make sure to use it in the double solenoid system.
(2) SIO connector (SIO connector equipped on the ELECYLINDER unit) on ELECYLINDER
connected to the EC connection unit cannot be used.
(3) The jog switch on the EC connection unit should perform forward end and rearward end
movements with the data set in the position data. It should perform the home-return
operation before an operation to both forward and rearward end movements if the home-
return operation is not completed.
(4) As the jog switch to be activated/inactivated should be set in the I/O parameter No.191 “EC
Connection Unit JOG Switch”, the setting should be reflected to all the EC connection units
at once.
(5) The EC connection unit occupies domains for four axes (one word) even though not all of
four axes are connected. Also, an axis number that an axis is not connected should not be
pulled one number forward.
(6) When in “MANU Mode
”
and a teaching tool is set to “Permit EC I/O Command
”
, any teaching
operation of ELECYLINDER in the PC software is not available. (There should be Alarm 124
or 125 generated in the PC teaching software. Refer to [16.3 EC Teaching Tool Error List in
XSEL PC Software (RSEL Edition)] for details.)
Set it to “Prohibit EC I/O Command
”
wen having a teaching operation.
(7) While an operation command is kept activated, if the setting is switched to “Permit EC I/O
Command
”
in “MANU Mode
”
or “MANU Mode
”
is switched to “AUTO Mode
”
, the
ELECYLINDER may receive the operation command and may start operation.
Make sure to turn any operation command signal off before switching the setting to avoid
any operation at the timing of switching.
(8) ELECYLINDER equipped with a digital speed controller should show “tool in connection
”
while a teaching tool is connected or during communication in the XSEL serial
communication protocol (Format B) with a host device (such as PLC and touch panel), and
use of the digital speed controller should be disabled.
Passing approximately 5 seconds with no communication will enable use of the digital speed
controller.
(Even while a teaching tool is connected, the digital speed controller may become available
to use depending on windows.)
Summary of Contents for R-unit RSEL
Page 2: ......
Page 5: ...ME0392 4C 2 Quick Start Guide Japanese Only ...
Page 32: ...Actuator Coordinate System Intro 18 ME0392 4C 2 Slider type 3 Table type 0 0 0 0 ...
Page 50: ...Chapter 1 RSEL System 1 4 Installation 1 13 ME0392 4C ...
Page 244: ...Chapter 4 Unit connection Installation and Wiring 4 5 PIO Circuit 4 32 ME0392 4C ...
Page 316: ...Chapter 5 Operation 5 10 ELECYLINDER Operation 5 52 ME0392 4C ...
Page 438: ...Chapter 6 Field Network PIO SIO 6 5 Example of Connectivity Setting 6 120 ME0392 4C ...
Page 532: ...10 6 Servo Gain Adjustment 10 90 10 7 Parameter Configuration Advanced Use 10 93 ...
Page 638: ...Chapter 10 Parameter 10 7 Parameter Configuration Advanced Use 10 106 ME0392 4C ...
Page 838: ...Chapter 14 Warranty 14 Warranty 14 3 ME0392 4C ...
Page 843: ......
Page 844: ......