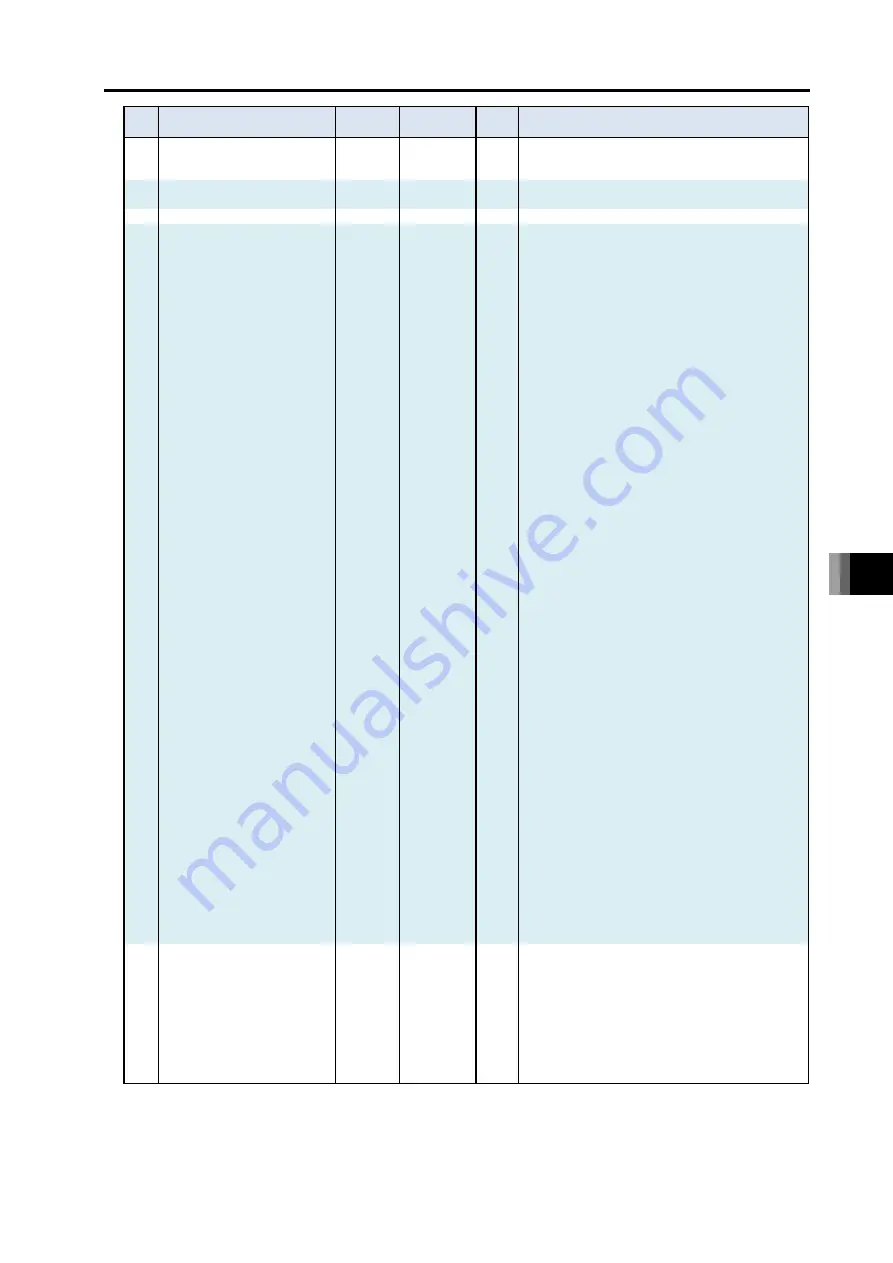
Chapter 10 Parameter
10.2 Parameter List (SEL Unit)
1. I/O parameter
10-4
ME0392-4C
10.2 Parameter List (SEL Unit)
10.2.1 I/O parameter
No.
Parameter name
Setting at
Delivery Input range Unit
Remarks
1 I/O port assignment type
Depends on
Controller
Construction
0 to 20
0: Fixed assignment
1: Automatic assignment
* Priority of I/O port assignment at automatic
assignment
(
I/O1→PIO
unit
•
PIO/SIO unit)
2
to
13
Reserved by the system
0H
0H to
FFFFFFFFH
14 Number of Ports Used for I/O1
Fieldbus Remote Input
Depends on
Controller
Construction
0 to 1,024
Multiple of 8
15 Number of Ports Used for I/O1
Fieldbus Remote Output
Depends on
Controller
Construction
0 to 1,024
Multiple of 8
16 I/O1fix-allocated input port start
No.
Depends on
Controller
Construction
-1 to 3,999
0 + (Multiple of 8) (0 to 299)
1,000 + (Multiple of 8) (1,000 to 3,999)
(Invalid if a negative value is set.)
* Only fieldbus available for setting in 1,000 to 3,999
17 I/O1fix-allocated output port
start No.
Depends on
Controller
Construction
-1 to 6,999
300 + (multiple of 8) (300 to 599)
400 + (multiple of 8) (4,000 to 6,999)
(Invalid if a negative value is set.)
* Only fieldbus available for setting in 4,000 to 6,999
18 I/O1 error monitor
Depends on
Controller
Construction
0 to 5
0: Do not monitor
1: Monitor
2: Monitor (Do not monitor 24-V I/O power errors)
3: Monitor (Monitor 24-V I/O power errors)
4: Monitor (Make 24V I/O power errors to message
level)
* Only PIO available for setting in 2 to 4
* Some exceptions apply.
19 (For expansion)
0
20 Input filtering periods
2
1 to 9
ms Input signal is recognized when the status is held for
twice the period set by this parameter.
21 Reserved by the system
(change is prohibited)
0
1 to 9
22 Reserved by the system
2000
0 to 99,999
ms
23 Reserved by the system
0H
0H to
FFFFFFFFH
24 I/O setting bit pattern 1
(global specification)
10000H
0H to
FFFFFFFFH
Bits 0-3: Reserved by the system
Bits 4 to 7: RDY LED function selection
(0: Program can be run
1: Error of operation-cancellation level or
higher is not present
2: Error of cold-start level or
* SYS LED prioritizes ALM flash
condition
Bits 8-19: Reserved by the system
Bits 20 to 23: ALM LED function selection
(0: An error higher than message level
has occurred
1: An error higher than operation
cancel level has occurred
2: An error higher than cold-start level
has occurred
3: An error higher than system shutoff
level has occurred)
Bits 24-27: Reserved by the system
25 I/O setting bit pattern 2
(global specification)
0H
0H to
FFFFFFFFH
Bits 0-3: Reserved by the system
Bits 4-7: Reserved by the system
Bits 8-11: Reserved by the system
10.2
Parameter List (SEL Unit)
1. I/O parameter
ME0392-4C
10-5
No.
Parameter name
Setting at
Delivery Input range Unit
Remarks
26
to
27
(For expansion)
0
28 I/O ready output port number
0
0 to 6,999
Output port ON when I/O is ready
(Invalid if “0” is set)
29 Reserved by the system
0
0 to 6,999
30 Input function selection 000
1
0 to 5
0: General-purpose input
1: Program start signal (ON edge)
(Input ports 007 to 014, BCD-specified program
number)
2: Program start signal (ON edge)
(Input ports 007 to 014, binary-specified program
number)
3: Program start signal (ON edge) (Input ports. 008
to 014, BCD-specified program number)
Note: The function of “I/O parameter No. 44, Input
function selection 014” (relating to drive-
source cutoff reset) is assigned to “I/O
parameter No. 37, Input function selection
007,” while the function of “I/O parameter
No. 43, Input function selection 013” (error
reset, program number specified for
program start) is assigned to “I/O parameter
No. 44, Input function selection 014.”
To specify a program number of 7 bit long,
“1: Program number specified for program
start” must be set for “I/O parameter No. 38,
Input function selection 008” through “I/O
parameter No. 44, “Input function selection
014.”
4: Program start signal (ON edge)
(Input ports. 008 to 014, binary-specified program
number)
Note: The function of “I/O parameter No. 44, Input
function selection 014” (relating to drive-
source cutoff reset) is assigned to “I/O
parameter No. 37, Input function selection
007,” while the function of “I/O parameter
No. 43, Input function selection 013” (error
reset, program number specified for
program start) is assigned to “I/O parameter
No. 44, Input function selection 014.”
To specify a program number of 7 bit long,
“1: Program number specified for program
start” must be set for “I/O parameter No. 38,
Input function selection 008” through “I/O
parameter No. 44, “Input function selection
014.”
* When using this signal to start a program, make
sure the signal remains ON for 100 ms or longer
so that the program will start without fail.
* Program Nos. 1 to 99 can be started via BCD
specification, while program Nos. 1 to 255 can be
started via binary specification.
Note: The port number assigned to this function can
be changed using I/O parameter No. 283,
“Port number assigned to input function
selection 000.”
31 Input function selection 001
0
0 to 5
0: General-purpose input
1: Software reset signal (1 s ON)
* If continued operation is specified as the action
upon emergency stop, enable the software reset
signal (to provide a means of canceling the
operation).
Note: The port number assigned to this function can
be changed using I/O parameter No. 284,
“Port number assigned to input function
selection 001.”
Summary of Contents for R-unit RSEL
Page 2: ......
Page 5: ...ME0392 4C 2 Quick Start Guide Japanese Only ...
Page 32: ...Actuator Coordinate System Intro 18 ME0392 4C 2 Slider type 3 Table type 0 0 0 0 ...
Page 50: ...Chapter 1 RSEL System 1 4 Installation 1 13 ME0392 4C ...
Page 244: ...Chapter 4 Unit connection Installation and Wiring 4 5 PIO Circuit 4 32 ME0392 4C ...
Page 316: ...Chapter 5 Operation 5 10 ELECYLINDER Operation 5 52 ME0392 4C ...
Page 438: ...Chapter 6 Field Network PIO SIO 6 5 Example of Connectivity Setting 6 120 ME0392 4C ...
Page 532: ...10 6 Servo Gain Adjustment 10 90 10 7 Parameter Configuration Advanced Use 10 93 ...
Page 638: ...Chapter 10 Parameter 10 7 Parameter Configuration Advanced Use 10 106 ME0392 4C ...
Page 838: ...Chapter 14 Warranty 14 Warranty 14 3 ME0392 4C ...
Page 843: ......
Page 844: ......