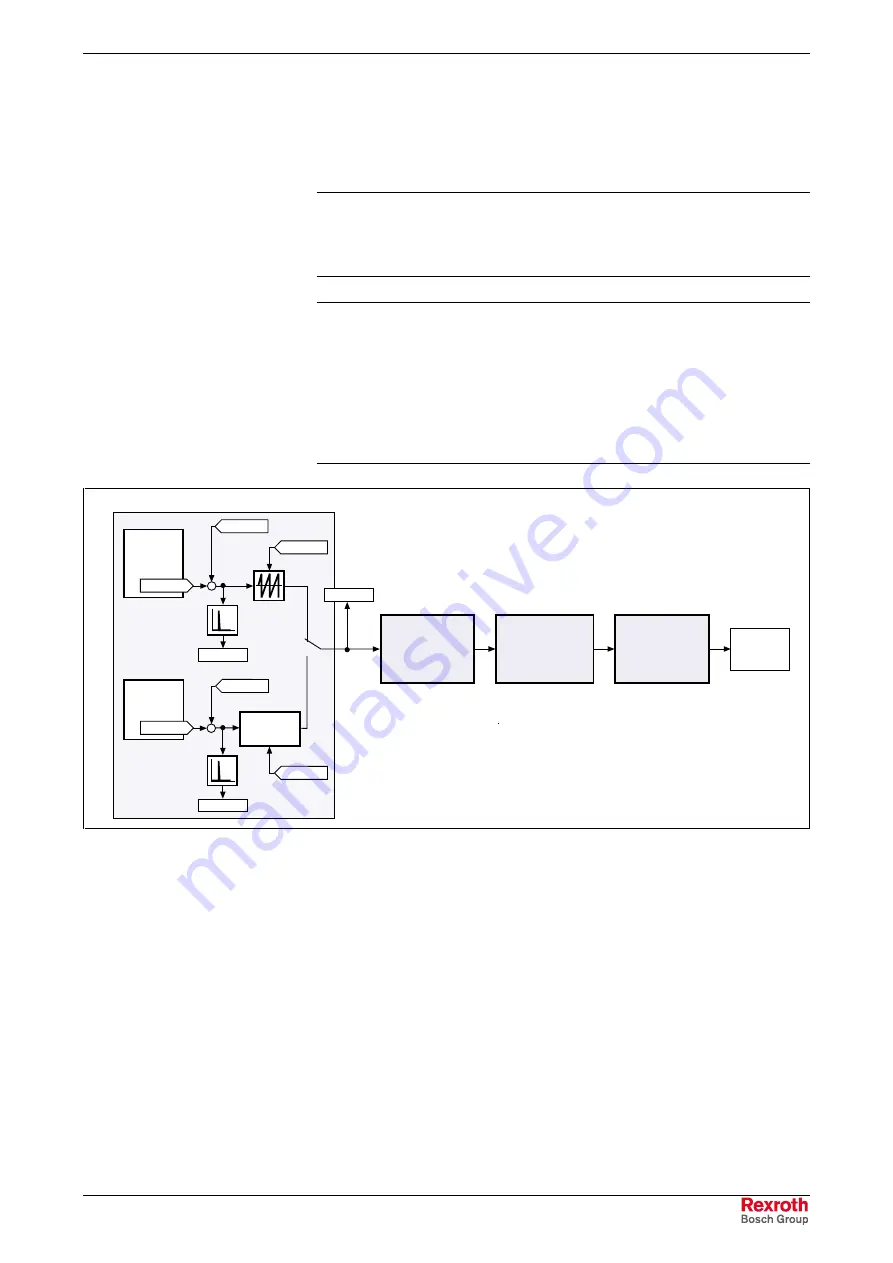
MPH-02, MPB-02, MPD-02
Operating Modes
7-79
DOK-INDRV*-MP*-02VRS**-FK01-EN-P
•
In the case of a virtual master axis, command values are cyclically
preset by the master via the master communication.
See also "Measuring Encoder" in chapter "Extended Drive Functions"
Note:
The master axis position can only be processed in a binary
format (1 master axis revolution = 2
20
increments). This has to
be taken into consideration when using a real master axis
encoder and the encoder has to be selected accordingly.
Note:
The minimum/maximum value of
P-0-0054, Additive master
axis position
at maximum corresponds to the master axis
cycle (P-0-0750 * 2
20
).
Exception:
When
P-0-0750, Master axis revolutions per master axis
cycle
equals zero, the resulting maximum value for parameter
P-0-0054 is (231 – 1) increments and the minimum value is
–231 increments.
P-0-0052
P-0-0053
electronic
gear
with
fine adjust
dynam.
synchron-
ization
DF000097v01_en.fh7
+
+
evaluation
real
master axis
encoder
virtual
master axis
position
fine
interpolator
master axis evaluation and adjustment
cmd value
processing
specific to
oper. mode
internal
command
value
P-0-0775
P-0-0750
P-0-0764
P-0-0750
P-0-0054
P-0-0054
P-0-0764
Fig. 7-47:
Function block "master axis evaluation" for real/virtual master axis
The command value input in the synchronization modes with real or
virtual master axis is carried out depending on the kind of master axis:
•
real master axis:
A measuring encoder is cyclically evaluated in the position loop clock,
the master axis position is displayed in parameter
P-0-0052, Actual
position value of measuring encoder
.
•
virtual master axis:
A virtual master axis position is cyclically preset in the NC clock via
parameter
P-0-0053, Master axis position
. This master axis position
is preset by the master in equidistant intervals.
Command Value Input with
Real/Virtual Master Axis
Courtesy
of
CMA/Flodyne/Hydradyne
▪
Motion
Control
▪
Hydraulic
▪
Pneumatic
▪
Electrical
▪
Mechanical
▪
(800)
426-5480
▪
www.cmafh.com