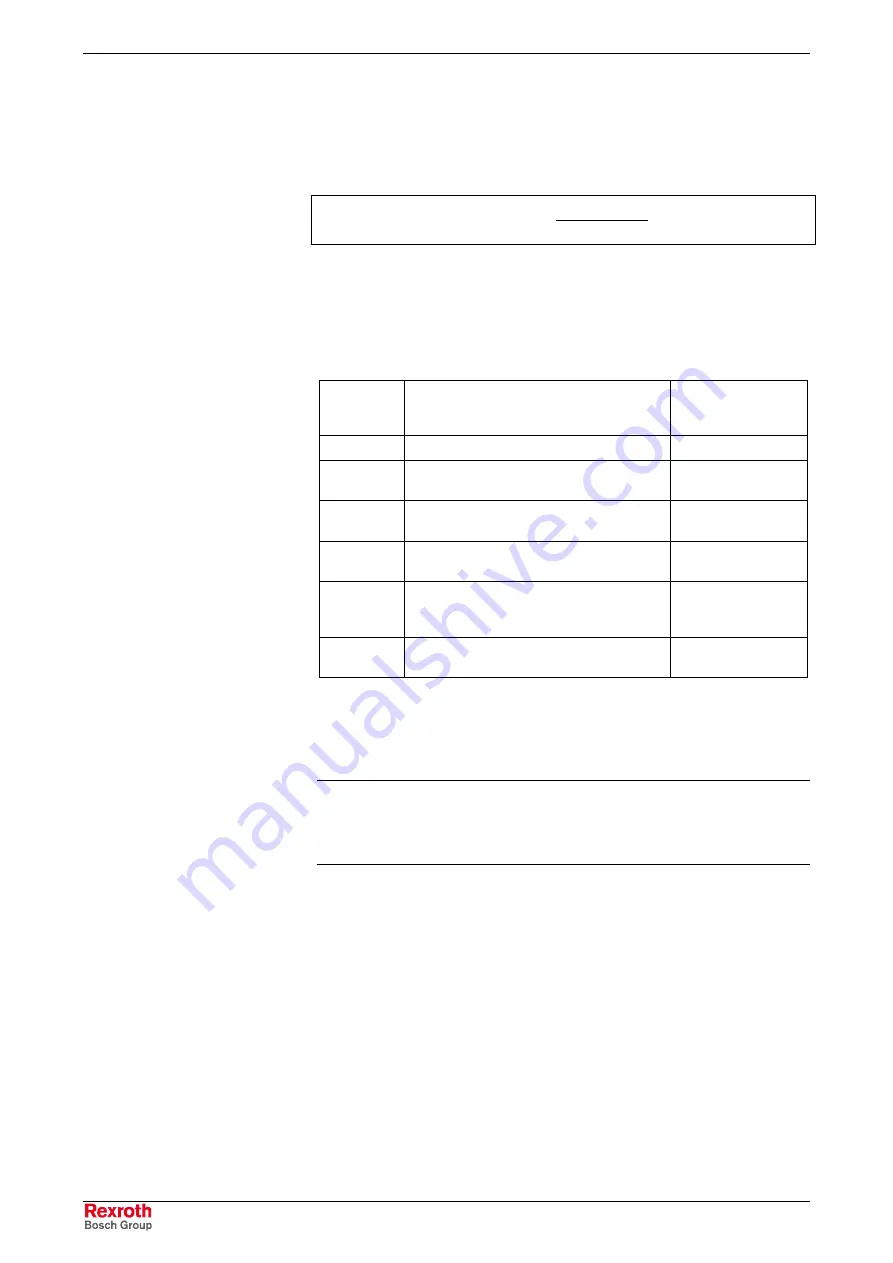
5-60
Motor, Mechanical Axis System, Measuring Systems
MPH-02, MPB-02, MPD-02
DOK-INDRV*-MP*-02VRS**-FK01-EN-P
therefore be switched off in this case by the respective value in the
P-0-0185, Control word of encoder 2 (optional encoder)
parameter.
Determining the maximum frequency of the encoder (encoder output
frequency):
min
/
60000
/
max
,
s
n
rev
DP
f
out
encoder
∗
=
f
encoder, out
:
encoder output frequency in kHz
DP/rev:
number of lines of the encoder
n
max
:
maximum speed of the spindle in min
-1
Fig. 5-76:
Calculating the output frequency of the encoder
In the firmware there are, for the different encoder types, maximum
frequencies stored up to the values of which troublefree signal evaluation
is guaranteed:
Value of
P-0-0075
External encoder used
Maximum
frequency stored in
firmware
1
GDS/GDM encoder (Rexroth standard)
70 kHz
2
incremental encoder with sine signals
(signal specification of Heidenhain)
200 kHz
3
resolver encoder with encoder data
memory
2 kHz
4
encoder with HIPERFACE interface
from Stegmann
200kHz
5
incremental encoder with square-wave
signals
(signal specification of Heidenhain)
500 kHz
8
encoder with EnDat interface
from Heidenhain
200 kHz
Fig. 5-77:
Maximum frequency for troublefree encoder evaluation
When the maximum encoder output frequency reaches or exceeds the
maximum frequency stored in the firmware it makes sense to deactivate
the spindle encoder monitor.
Note:
The maximum frequency stored in the firmware has a "safety
distance" to the maximum input frequency of the respective
optional input module (see documentation "Project Planning
Manual for control sections").
Notes on Commissioning
See also "Notes on Commissioning" in section "Basics on Measuring
Systems, Resolution"!
If monitoring the axis position is desired when the drive is switched on the
values for the monitoring window have to be entered:
•
P-0-0095, Absolute encoder monitoring window for motor
encoder
•
P-0-0096, Absolute encoder monitoring window for opt. encoder
The unit is that of the actual position value. The size of the monitoring
window depends on application-specific aspects of operational safety. If
this monitoring function is not desired you have to enter the value "0".
Setting the Axis Position
Monitor (Only with Absolute
Encoder)
Courtesy
of
CMA/Flodyne/Hydradyne
▪
Motion
Control
▪
Hydraulic
▪
Pneumatic
▪
Electrical
▪
Mechanical
▪
(800)
426-5480
▪
www.cmafh.com