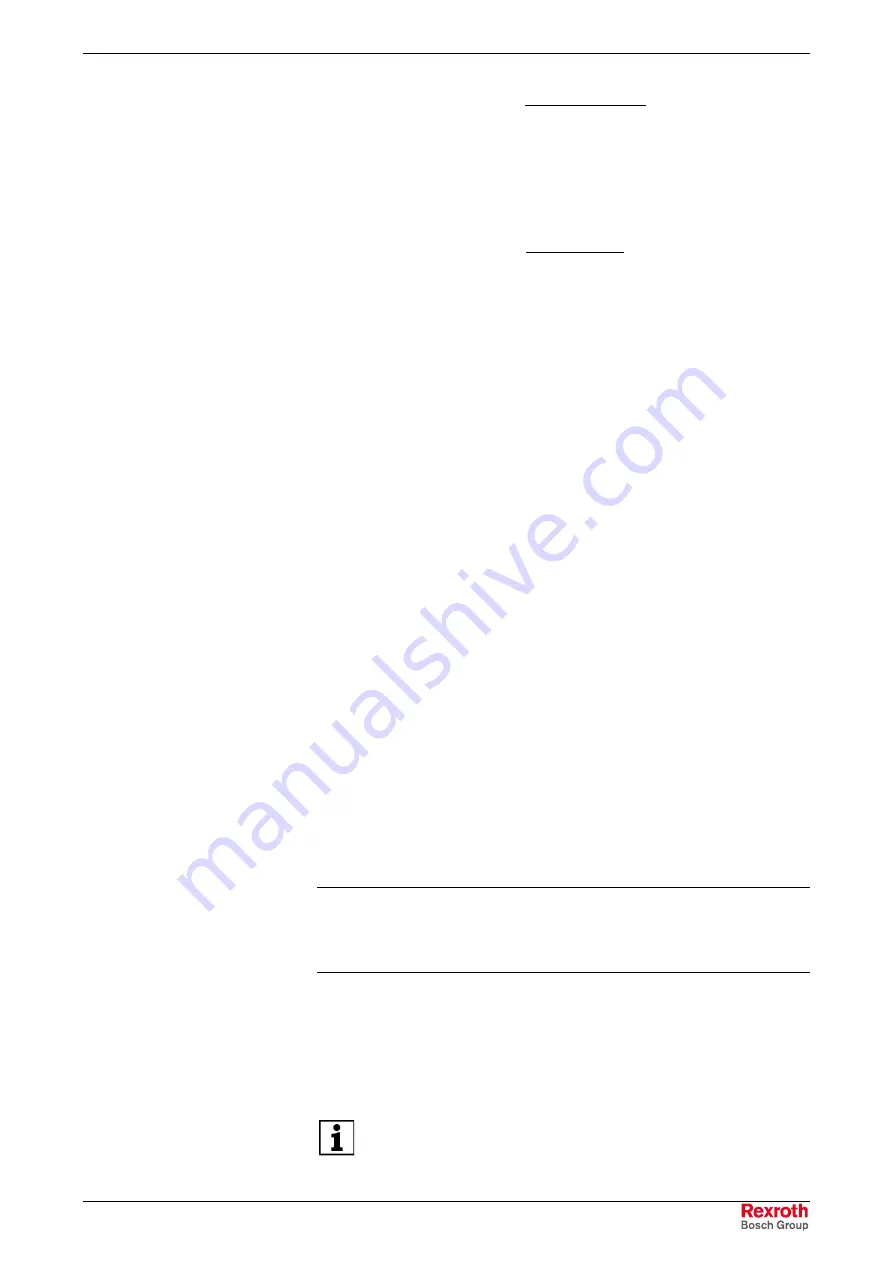
MPH-02, MPB-02, MPD-02
Drive Control
6-59
DOK-INDRV*-MP*-02VRS**-FK01-EN-P
If the step response shows less overshooting and shorter period of
oscillation:
7. Check whether there is further improvement when increasing the
value in parameter
P-0-1122, Velocity control loop filter:
bandwidth of band-stop filter
or when changing the value in
parameter
P-0-1123, Vel. cont. loop filter: center frequency of
band-stop filter
.
If the step response shows the same behavior:
8. Check the determined resonance frequency; if necessary,
significantly increase the value in parameter
P-0-1122, Velocity
control loop filter: bandwidth of band-stop filter
.
9. With the previously optimized values in the parameters
P-0-1122,
Velocity control loop filter: bandwidth of band-stop filter
and
P-0-1123, Vel. cont. loop filter: center frequency of band-stop
filter
optimize the velocity loop again.
10. If necessary, carry out another optimization procedure for parameters
P-0-1122 and P-0-1123 due to the high-frequency or less attenuated
resonance points that are now possibly occurring.
Diagnostic and Status Messages
The velocity error (S-0-0347) is generated from the effective velocity
command value (P-0-0048) and the current actual velocity value
(S-0-0040) by means of subtraction.
The acceleration torque is determined from the total inertia (determined
using the automatic control loop setting) and the value in parameter
S-0-0164, Acceleration feedback value 1
. It is displayed in parameter
P-0-0451, Actual acceleration torque/force value
.
The current process torque is determined from the current total torque in
parameter
S-0-0084, Torque/force feedback value
and the determined
P-0-0451,
Actual acceleration torque/force value
. It is displayed in
P-0-0452, Actual process torque/force value
.
The output signal of the velocity loop is limited to a maximum and a
minimum torque. This is a torque/force command value that already
includes the additive component for the friction torque compensation.
This torque command value is limited with the parameters S-0-0082,
S-0-0083 and S-0-0092. The effective torque/force command value
(P-0-0049) can be read at the output of the limitation.
Note:
When the limit is active, the corresponding warning
E8260
Torque/force command value limit active
is generated and
the respective bit (positive/negative limitation) is set in
parameter
P-0-0555, Controller status word
.
The correct function of the velocity loop is monitored in the drive to avoid
the so-called "runaway effect". Possible error causes are:
•
incorrect commutation angle
•
interchanged motor connection
In the case of error the drive torque is immediately disabled and the error
message
F8078 Speed loop error
is generated.
See also Troubleshooting Guide for "F8078 Speed loop error"
Optimizing Rejection Filter or
Velocity Loop
Velocity Error
Acceleration Torque/Force
Process Torque/Force
Current Command Value Limit
(E8260)
Speed Loop Error (F8078)
Courtesy
of
CMA/Flodyne/Hydradyne
▪
Motion
Control
▪
Hydraulic
▪
Pneumatic
▪
Electrical
▪
Mechanical
▪
(800)
426-5480
▪
www.cmafh.com