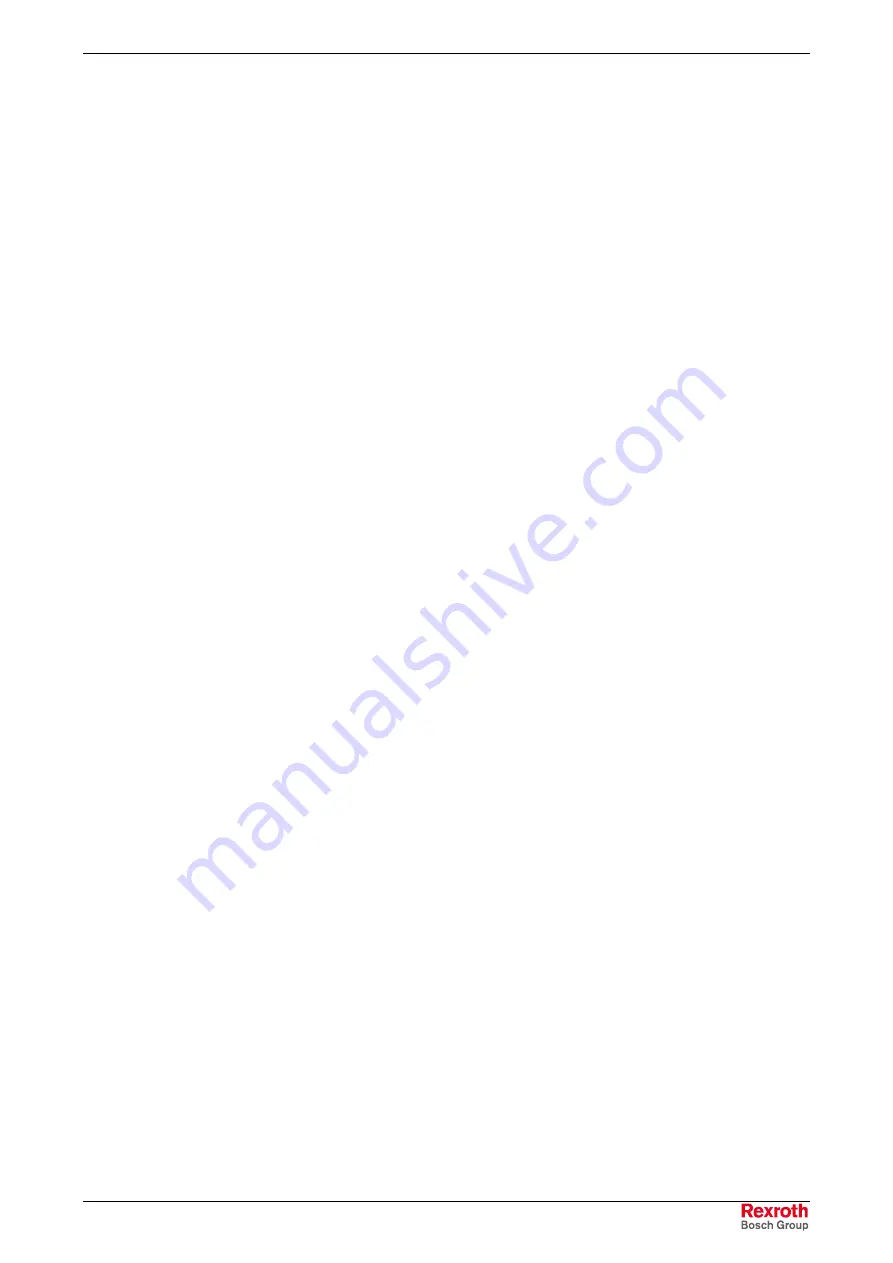
MPH-02, MPB-02, MPD-02
Drive Functions
8-9
DOK-INDRV*-MP*-02VRS**-FK01-EN-P
Parameters for relative measuring systems, distance-coded:
•
S-0-0165, Distance-coded reference offset A
•
S-0-0166, Distance-coded reference offset B
•
S0-0177, Absolute offset 1
•
S-0-0178, Absolute offset 2
Diagnostic messages for relative measuring systems:
•
C0600 Drive controlled homing procedure command
•
C0601 Homing only possible with drive enable
•
C0602 Distance home switch - reference mark erroneous
•
C0604 Homing of absolute encoder not possible
•
C0606 Reference mark not detected
•
C0607 Reference cam input not assigned
Functional Description
General Information
With regard to the type and arrangement of the reference marks, relative
measuring systems can be divided into 4 groups:
•
Group 1:
Single-turn measuring systems with absolute range, such as single-
turn HSF or resolvers. These measuring systems have an absolute
position measuring range of one encoder revolution or parts of one
encoder revolution (resolver) and do not have their own reference
mark signal. The controller, however, recognizes the zero position
(0 dgr) of the actual position value as the reference mark signal.
These properties apply to:
•
single-turn motor encoders of Rexroth motors of the MHD, MKD,
MKE, MSK, MSH, MAD and MAF series
•
GDS measuring system from Rexroth
•
single-turn encoder from Heidenhain (with EnDat interface)
•
Group 2:
incremental rotary measuring systems with one reference mark per
encoder revolution, such as the ROD or RON types from Heidenhain
•
Group 3:
incremental linear measuring systems with one or several reference
marks, such as the LS linear scales from Heidenhain
•
Group 4:
incremental measuring systems with distance-coded reference marks,
such as the LSxxxC linear scales from Heidenhain
For measuring systems with distance-coded reference marks see also
"Relative Measuring Systems" in chapter "Motor, Mechanical Axis
System, Measuring Systems"
In order to establish the position data reference of relative measuring
systems the drive has to be able to identify an unequivocal dedicated
point within the travel range of the axis. To do this, the axis has to carry
out the following movement:
•
pass the dedicated point (encoders of group 1, 2 or 3)
- or -
•
pass two neighboring distance-coded reference marks (encoders of
group 4)
Pertinent Diagnostic Messages
Type and Arrangement of
Reference Marks
Action of the Axis Drive to
Establish Position Data
Reference
Courtesy
of
CMA/Flodyne/Hydradyne
▪
Motion
Control
▪
Hydraulic
▪
Pneumatic
▪
Electrical
▪
Mechanical
▪
(800)
426-5480
▪
www.cmafh.com