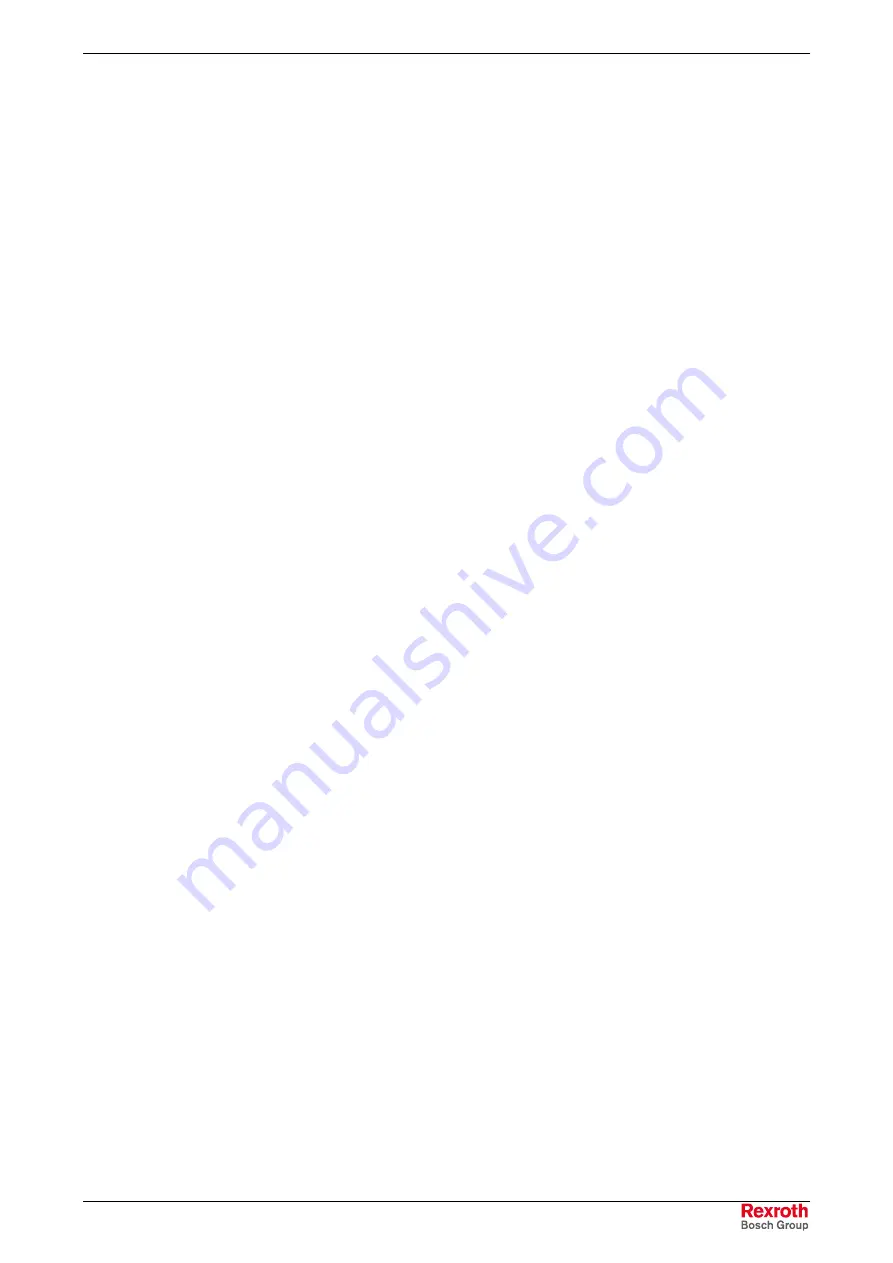
MPH-02, MPB-02, MPD-02
Motor, Mechanical Axis System, Measuring Systems
5-77
DOK-INDRV*-MP*-02VRS**-FK01-EN-P
Scaling of Physical Data
Brief Description
The controller via data maps the drive to an internal mathematical model.
The status variables of the drive are determined on the basis of:
•
position
measurement,
•
current measurement and
•
temperature
measurement.
The measured values collected in this way are converted into phys. data:
•
position, velocity, acceleration and jerk data
•
current data, torque and force data
•
temperature data and load data
The master transmits command values to the drive that are used by the
controller for transforming them at the motor output shaft or mechanical
axis system. The drive in return registers and transmits actual values,
signals operating and command states and, if necessary, generates error
messages and warnings.
Communication between drive and master also takes place by
exchanging data.
An operating data (numeric value) can only be evaluated as a physical
value, when the numeric value is connected to a physical unit and the
position of the decimal point (decimal places). The data thereby is
"scaled" in a qualitative and quantitative way.
All data are stored in parameters and transmitted as parameter values
(for explanations on parameters see chapter "Parameters, Basics" in
chapter "Handling, Diagnostic and Service Functions"). The scaling of the
parameters containing data of the following physical values can be
defined by the customer:
•
position
•
velocity
•
acceleration
•
torque/force
•
temperature
To simplify the scaling definition so-called "preferred scalings" were
predefined. But physical data can also be exchanged in the control-
internal format, i.e. without concrete reference to physical units. To do
this, the scaling for certain data can be freely set ("parameter scaling").
Depending on the kind of motion of motor or load, the data can be
displayed
•
in linear form (linear axis or motor motion)
- or -
•
in rotary form (rotary axis or motor motion)
In the drive firmware there are mechanical transfer elements between
motor and load mapped by means of mathematical models. The physical
data can thereby be referred to
•
the point where the load takes effect (load-side data reference)
- or -
•
the point where the force is input (motor-side data reference).
Scaling
Parameters
Preferred Scaling/
Parameter Scaling
Linear and Rotary Data
Motor Reference/Load Reference
Courtesy
of
CMA/Flodyne/Hydradyne
▪
Motion
Control
▪
Hydraulic
▪
Pneumatic
▪
Electrical
▪
Mechanical
▪
(800)
426-5480
▪
www.cmafh.com