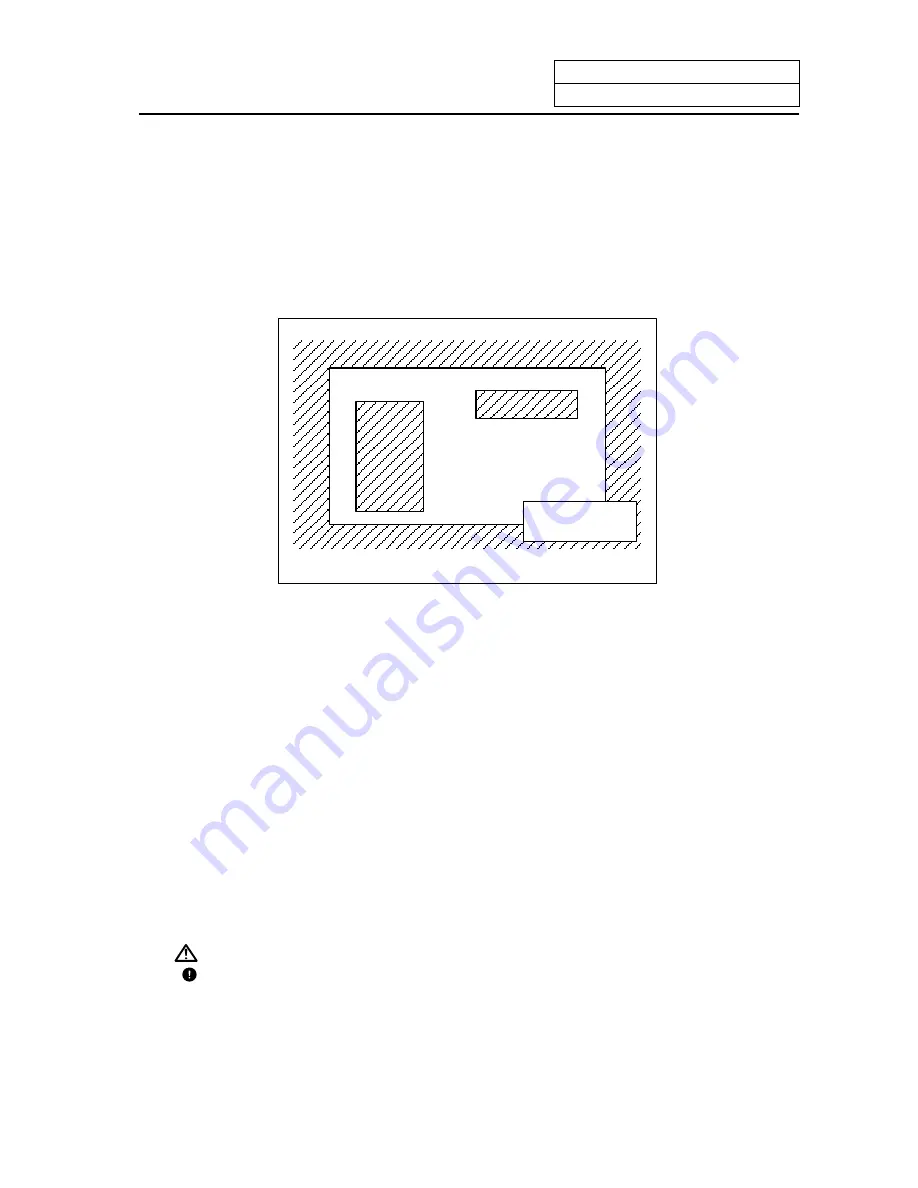
5. Stored Stroke Limit
III
-26
5. Stored Stroke Limit
(1) Outline
Three tool entry prohibited ranges can be set with stored stroke limit I, stored stroke limit II, IIB and
stored stroke limit IB. Part of the prohibited range on the outside of soft limit I can be validated with
stored stroke limit IC.
The stored stroke limit II and IIB select the outer side (II) and inner side (IIB) of the entry prohibited
range with parameters.
Stored stroke limit IB
Stored stroke limit IIB
Stored stroke limit I
Stored stroke
limit IC
If the tool tries to move over the set range, an alarm will appear, and the axis will decelerate to a stop.
If the prohibited range is entered and an alarm occurs, movement will be possible only in the
direction opposite the entry direction.
[Valid Conditions of Stored Stroke Limit]
When using the relative position detection system, the stored stroke limit is invalid until the
reference point return is completed after the power is turned ON.
The stored stroke limit can be validated even if the reference point return is not yet completed, by
setting parameter #2049 type = 9.
If the absolute position detection is valid when using the absolute position detection system, the
stored stroke limit will be validated immediately after the power is turned ON.
[Stored stroke limit coordinates]
The stored stroke limit check is carried out in the basic machine coordinate system established by
the reference point return. To validate the stored stroke limit even when the reference point return is
not yet completed, check the stored stroke limit using the temporary basic machine coordinate
system (basic coordinate system defined when the power was previously turned OFF).
When the 1st dog-type reference point return is completed after the power is turned OFF, the
correct coordinate system is established.
CAUTION
Always set the stored stroke limit. Failure to set this could result in collision with the machine
end.
(Note)
The axis movement possible when the reference point return has not yet completed is limited
to manual and handle feed only. Automatic operation is validated after the reference point
return is completed.
Summary of Contents for EZMotion-NC E60 Series
Page 1: ......
Page 15: ...I OPERATION SECTION ...
Page 361: ...II MACHINE OPERATION MANUAL ...
Page 399: ...III SETUP ...
Page 472: ...IV APPENDIXES ...
Page 510: ......