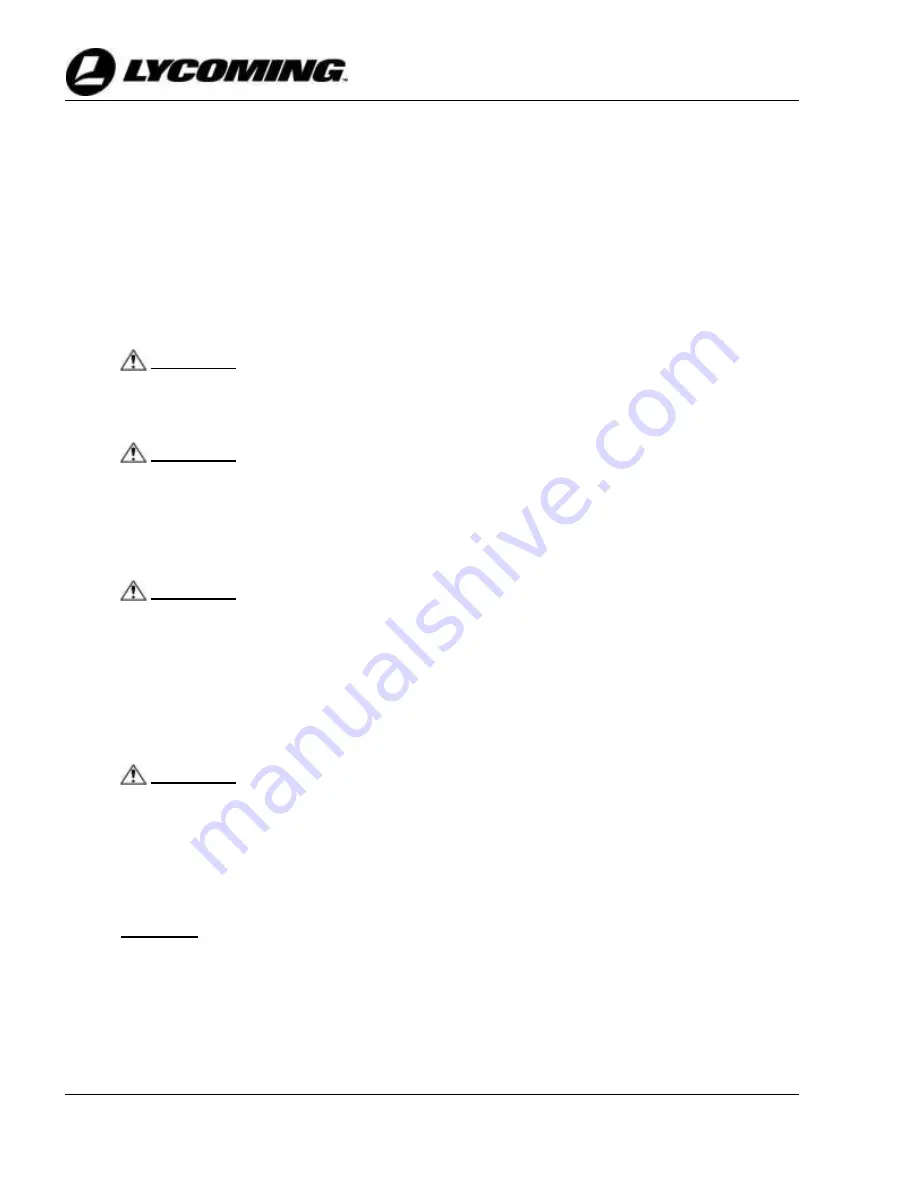
IO-390-D Series Engine Maintenance Manual
72-30
© 2020 Avco Corporation. All Rights Reserved
Page 194
March 2020
IO-390-D Series Engine Maintenance Manual
(1)
Immediately before the Cylinder Compression Check:
(a)
Operate the engine at usual cylinder head and oil temperatures (specified in Appendix
A of the
IO-390-D Series Engine Installation and Operation Manual
).
(b)
Put the power control in the IDLE CUT-OFF position.
(c)
Move the ignition switch to the OFF position to shut down the engine.
(d)
Make sure that the aircraft master switch and fuel supply switches are all in the OFF
position.
(e)
After the engine is shut down, complete the Cylinder Compression Check
immediately to get an accurate measurement.
(f)
Set the aircraft brakes and install the wheel chocks.
CAUTION
TAKE ALL NECESSARY PRECAUTIONS AGAINST ACCIDENTAL
ROTATION OF THE CRANKSHAFT/PROPELLER TO PREVENT
INJURY.
(2)
Disable power to the engine.
CAUTION
IGNTION LEADS AND SPARK PLUGS ARE VERY HOT. IN THE
NEXT STEP, WEAR PERSONAL PROTECTIVE GEAR TO PREVENT
BURNS.
(3)
Disconnect all of the spark plugs leads per the “Spark Plug Removal” procedure in
Chapter 74-20.
(4)
Remove the top spark plug from each cylinder.
CAUTION
USE GLOVES OR RAGS TO PROTECT HANDS WHILE HOLDING
THE PROPELLER BLADE.
(5)
Turn the crankshaft by hand in the direction of propeller rotation to put the piston in a
position as close to Top Dead Center (TDC) on the compression stroke as possible.
(6)
Install the threaded end of an adapter with a coupling end in the spark plug hole of the
cylinder to be tested.
(7)
Make sure that the air valve on the differential compression tester is in the OPEN
position.
CAUTION
BEFORE CONNECTION OF THE COMPRESSION TESTER, MAKE
SURE THAT THE AIR SUPPLY REGULATOR DOES NOT SHOW
MORE THAN 80 PSI (552 KPA) OF AIR PRESSURE. EXCESSIVE
AIR PRESSURE CAN CAUSE THE PROPELLER TO TURN. KEEP
CLEAR OF THE ROTATIONAL RADIUS OF THE PROPELLER.
(8)
Connect the differential compression tester to the adapter and to a clean source of
compressed air.
NOTICE:
Operate the differential compression tester per the manufacturer’s instructions.
(9)
Set the differential compression tester to approximately 100 to 120 psi (689 to 827 kPa).
(10)
Make sure that the engine cylinder pressure gage showed 80 psi (±2 psi) (552 kPa (± 14
kPa)), while it keeps the regulated pressure at 80 psi (552 kPa) for at least 5 seconds.
(11)
One mechanic holds the propeller firmly in place, to prevent crankshaft rotation, while
the other mechanic opens the cylinder pressure valve in the next step.