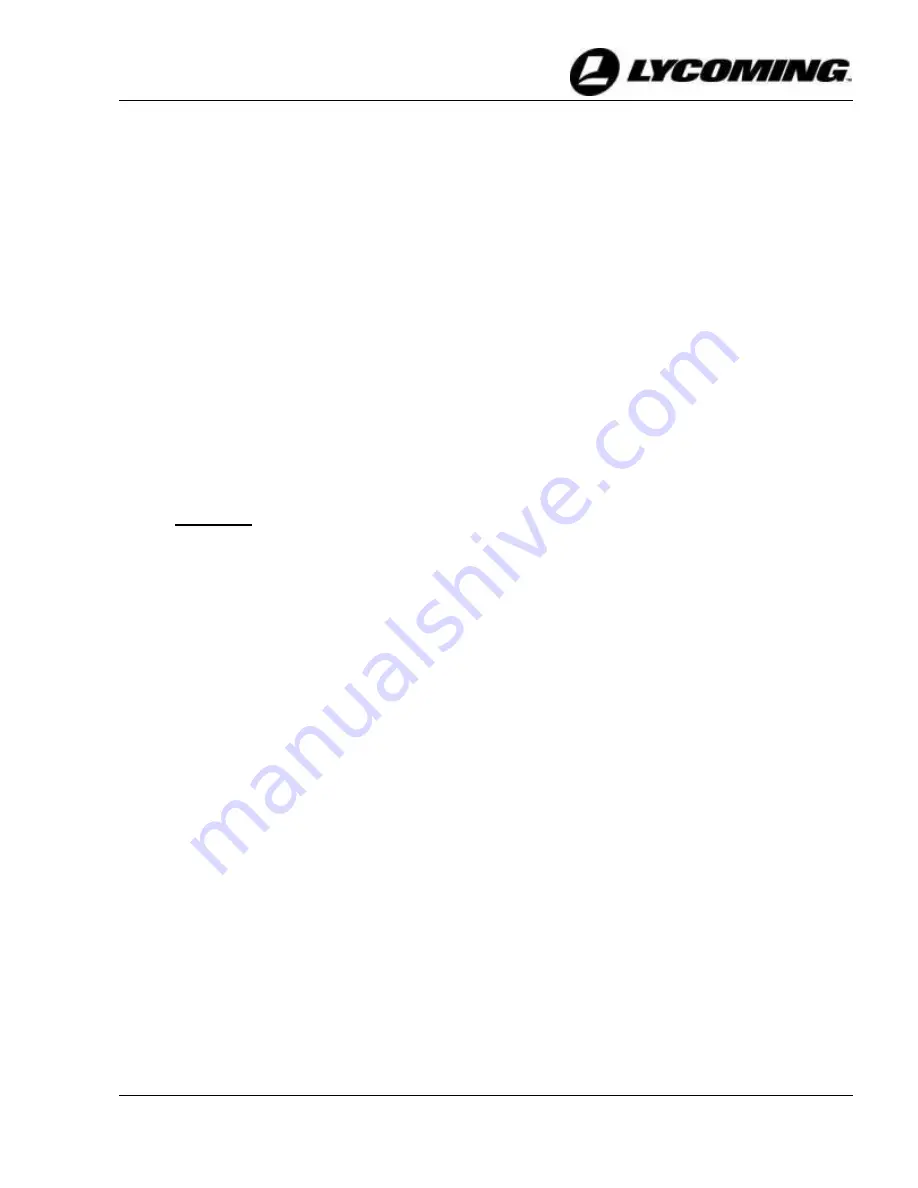
IO-390-D Series Engine Maintenance Manual
© 2020 Avco Corporation. All Rights Reserved
72-00
March 2020
Page 105
IO-390-D Series Engine Maintenance Manual
To adjust the idling speed to the desired rpm:
(1)
When the idle speed is stable, move the cockpit mixture control lever with a very slow,
steady pull toward the IDLE CUT-OFF position, do not let the engine stop. While
monitoring the tachometer, steadily move the mixture control lever to the FULL RICH
position.
(2)
An increase of more than 50 rpm during fuel mixture adjustment is an indication of an
excessively rich idle mixture. An immediate decrease in rpm (without an initial
momentary increase) is an indication that the idle mixture is too lean. Adjust the fuel
mixture as follows:
If the fuel mixture is too lean:
If the fuel mixture is too rich:
Turn the mixture adjustment wheel
(Figure 2) at the side of the fuel
injector servo toward
"R"
for
Rich
.
Turn the mixture adjustment wheel
(Figure 2) at the side of the fuel
injector servo away from
"R"
.
Turn the idle mixture adjustment
wheel on the throttle body in the
direction to
enrich
the fuel mixture.
Turn the idle mixture adjustment
wheel on the throttle body in the
direction to
lean
the fuel mixture.
NOTICE:
Run-up the engine to 2000 rpm to clear the engine each time you turn the idle
mixture adjustment wheel to adjust the idle speed mixture.
C.
After the adjustment, run up the engine again to 2000 rpm. Complete the previous steps
until the idle speed check shows a momentary increase of approximately 25 to 50 rpm.
D.
Make the final idle speed adjustment for the desired idling rpm with a closed throttle.
E.
If the idle speed setting is not stable after repeated attempts, complete a check of the idle
linkage. Look for loose connections which could cause erratic idling. Also take into
account weather conditions and field altitude which could affect the idle speed mixture
adjustment.
6.
Engine Mount Inspection
A.
Examine the engine mounts to make sure they are not cracked, damaged, or bent. Replace a
cracked, damaged, or bent engine mount in accordance with the aircraft manufacturer’s
instructions.
B.
Examine the engine mount bores for radial scoring. Replace the crankcase if radial scoring on
the engine mount bores is more than 0.010 in. (0.254 mm) depth.
C.
Examine the engine mounts for looseness. Tighten any loose hardware. Refer to the aircraft
manufacturer’s instructions.
D.
Examine the rubber engine mounts and mounting hardware for signs of deterioration or
damage. Replace worn or damaged engine mounts or hardware in accordance with the
aircraft manufacturer’s instructions.
E.
After the first 100 hours of operation, make sure that the engine fastening nuts and bolts for
the engine mounts are torqued correctly. For torque values, refer to the aircraft
manufacturer’s instructions.