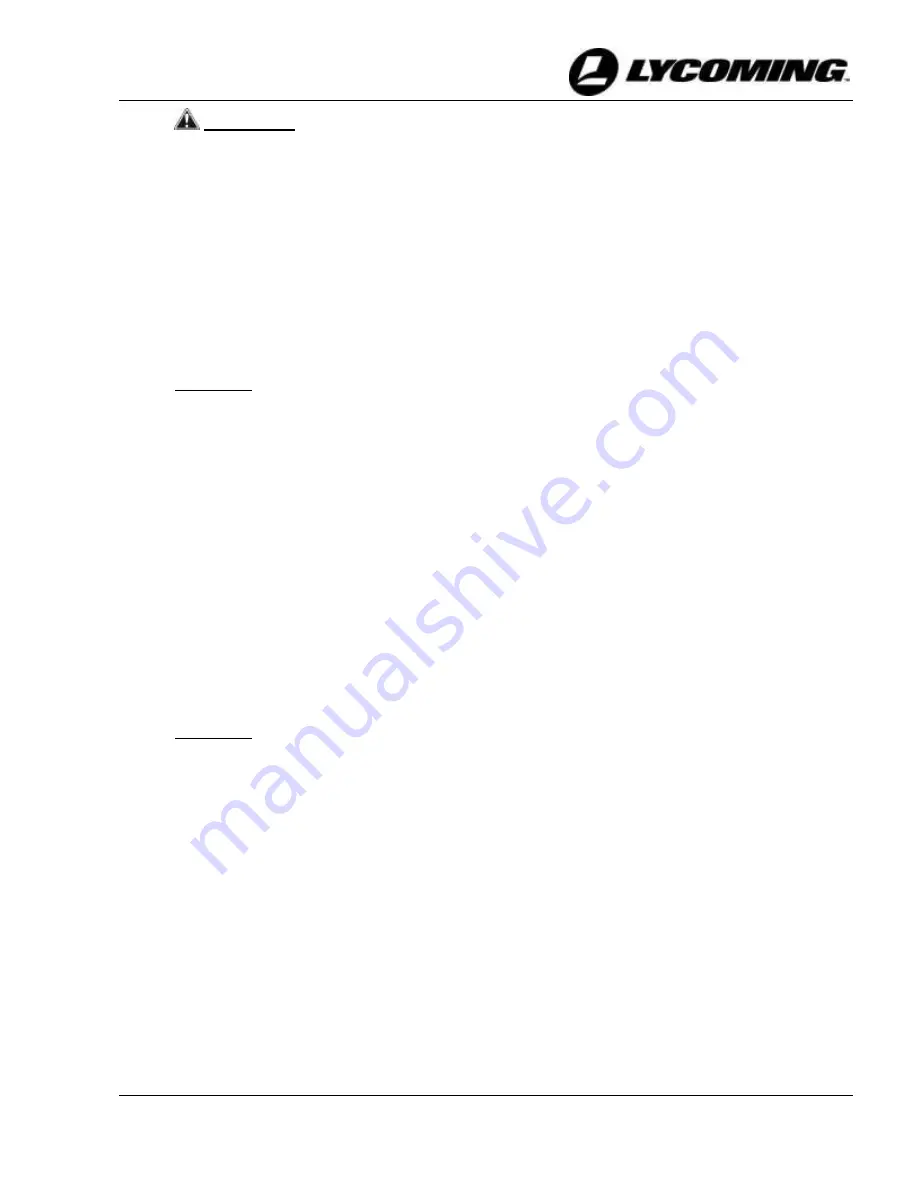
IO-390-D Series Engine Maintenance Manual
© 2020 Avco Corporation. All Rights Reserved
72-30
March 2020
Page 195
IO-390-D Series Engine Maintenance Manual
WARNING
IN THE NEXT STEP, HOLD THE PROPELLER FIRMLY WHEN
OPENING THE AIR VALVE ON THE DIFFERENTIAL
COMPRESSION TESTER. PENT-UP AIR PRESSURE IN THE
CYLINDER COULD CAUSE THE CRANKSHAFT TO TURN.
(12)
Slowly open the air valve on the differential compression tester and increase the pressure
to the cylinder to 15 to 20 psi (103 to 138 kPa).
(13)
Listen for escaping air. If escaping air is heard, refer to Table 2 to identify and correct
the cause.
(14)
Continue to turn the propeller in the direction of rotation against the 15 to 20 psi (103 to
138 kPa) pressure until the piston reaches TDC evident by a sudden decrease in the force
necessary to turn the propeller.
NOTICE:
If you turn the propeller past TDC, back up the rotation at least one revolution
and repeat this step to prevent backlash and to keep the piston rings in position.
Then repeat the previous step to turn the propeller to TDC.
(15)
With the piston at TDC, one mechanic holds the propeller securely while the other
mechanic opens the air valve slowly and completely. Gradually increase the air supply
pressure up to 80 psi (552 kPa). As the pressure increases, the other mechanic must
move the propeller back and forth slightly with a rocking motion to make sure that the
piston rings are seated.
(16)
Record the pressure reading on the engine cylinder pressure gage. The difference
between the engine cylinder pressure gage reading and the pressure shown on the air
supply pressure gage reading is the amount of leakage through the cylinder.
(17)
The minimum approved engine cylinder pressure reading is 60 psi (414 kPa). Maximum
approved leakage is 25% (20 psi (138 kPa) of the 80 psi (552 kPa) regulated pressure).
(18)
Close the air valve and disconnect the differential compression tester from the engine
cylinder and connect it to the spark plug hole of the next engine cylinder to be tested.
NOTICE:
Pressure readings for all of the engine cylinders are to be nearly equal. Refer to
Table 2.
(19)
Complete the previous steps for each of the remaining engine cylinders.
(20)
Refer to Table 2 for a summary of the Cylinder Compression Check results and
corrective action. Corrrective action in Table 2 applies to procedures in this chapter.
D.
Review and analyze the results. Take any necessary corrective action.
E.
Record the results of the Cylinder Compression Check for each cylinder on the 100-Hour
Inspection Checklist in Chapter 05-20.
F.
After all service is complete, examine and install the spark plugs and connect the ignition
leads to the spark plugs per the following procedures in Chapter 74-20.
•
Spark Plug Inspection
•
Spark Plug Rotation
•
Ignition Harness Inspection
•
Spark Plug Installation
•
Spark Plug Gap Setting