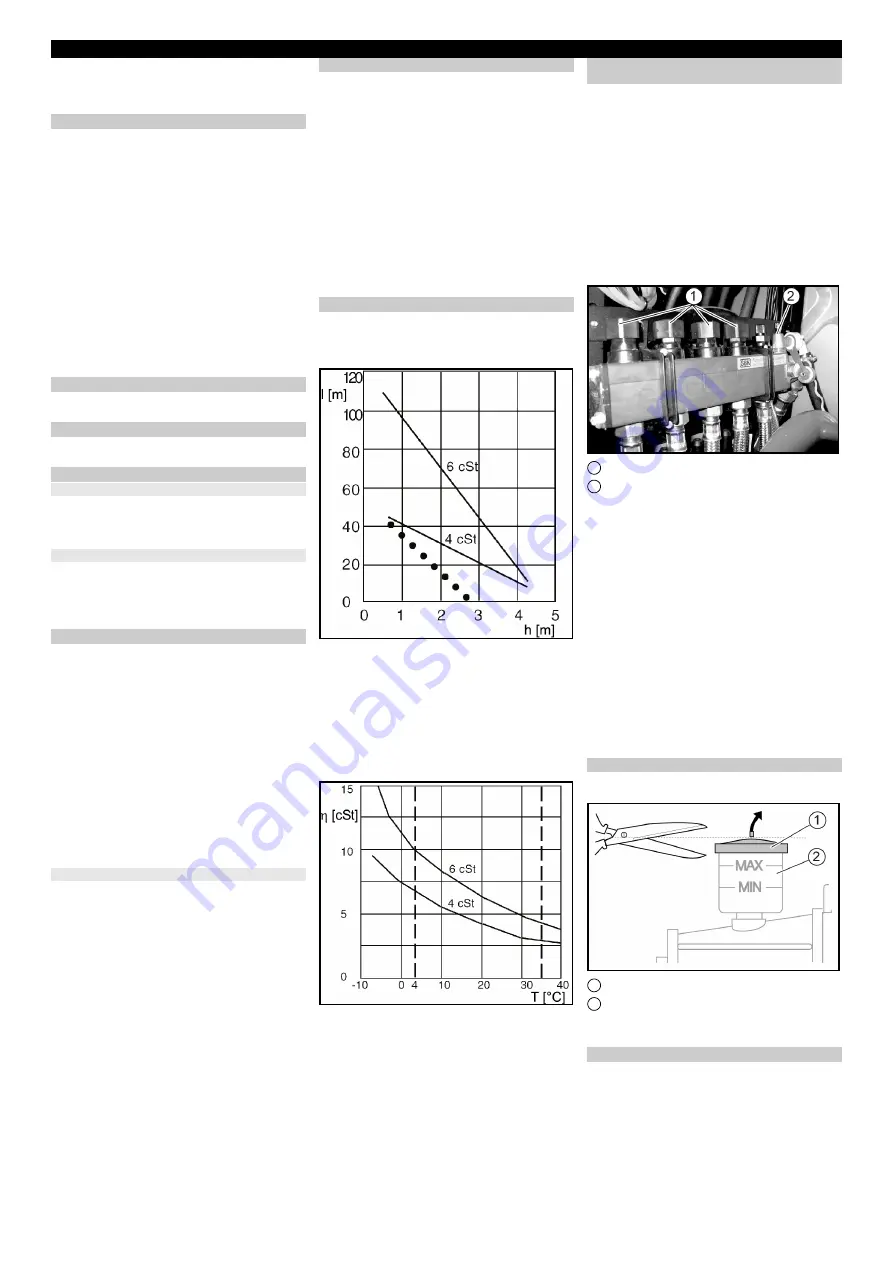
78
English
Installing the system (for technical specialists only)
Note
The system may only be set up by:
●
KÄRCHER customer service technicians
●
Authorised KÄRCHER persons
Preparation of the installation site
몇
WARNING
Health risk due to exhaust gases
Exhaust gases from gas or oil-fired systems are harmful
to health.
Position the system so that the exhaust gases do not
escape near air inlets.
Ensure sufficient ventilation at the installation site and
dispose of the exhaust gases properly.
The following requirements must be satisfied in order to
correctly install the system:
●
Horizontal, level foundation according to separate
drawing (request from KÄRCHER).
●
Electrical connection, see "Technical data".
●
Water connection, see the "Technical data".
●
For winter operation, sufficient insulation / heating of
the water and fuel supply line.
●
Waste water manhole and proper waste water dis-
posal.
●
Sufficient lighting at the washing station to ensure
safe working conditions for the washing customers.
Unpacking the system
1. Unpack the system.
2. Dispose of the packaging material for recycling.
Align and set up the system
1. Align the system on a level and horizontal installa-
tion site using the set screws on the base frame.
Mounting the attachments
Exhaust gas manifold
1. Place the exhaust gas manifold on the roof from the
outside.
2. Secure the exhaust gas manifold from the inside
with the enclosed screws.
Cleaning tool
1. Connect the high-pressure hose to the system.
2. Connect the high-pressure hose to the high-pres-
sure gun.
3. Connect the spray lance to the high-pressure gun.
4. Tighten all union nuts hand-tight.
Water connection
A category 5 system separator must be installed be-
tween the system and the drinking water network to iso-
late the system from the drinking water network. Locally
applicable regulations must also be observed.
Note
Impurities in the inlet water can damage the system.
Kärcher recommends using a water filter (see “Acces-
sories”).
ATTENTION
Risk of damage
Unsuitable water can damage the system.
Only use water of drinking quality to supply the system.
Observe the water quality requirements specified in the
chapter "Intended use".
1. Feed the supply hose through the system opening
from below and connect it.
For the connection values, see chapter "Technical da-
ta".
4. Water type (option)
When using a water distribution block 4. water type, pro-
cessed water can also be used with certain washing
programmes.
Processed water quality requirements:
●
pH value: 6.5...9.5
●
Electrical conductivity: Conductivity of fresh water
1200 µS/cm, max. 2000 µS/cm
●
settleable substances: < 0.5 ml *
●
Filterable particles: < 50 µm **
●
Hydrocarbons: < 20 mg/l
●
Chloride: < 300 mg/l
●
Calcium: < 200 mg/l
●
Total hardness: < 28 °dH, < 50° TH, < 500 ppm (mg
CaCO
3
/l)
●
Iron: < 0.5 mg/l
●
Manganese: < 0.05 mg/l
●
Copper: < 2 mg/l
●
Sulphate: < 240 mg/l
●
Active chloride: < 0.3 mg/l
●
Free of unpleasant odours
* Sample volume 1 litre / settling time 30 minutes
** no abrasive substances
Electrical connection
DANGER
Risk of injury from electric shock
If the power supply is not set up correctly, users can be
killed or injured by electric shock.
Have the power supply set up by an experienced elec-
trician.
●
The electrical connection must meet the require-
ments of IEC 60664-1.
●
The system must be protected by a fault current pro-
tection switch with a trigger current no greater than
30 mA.
●
A marked EMERGENCY OFF switch must be in-
stalled in the supply line of the system at an easily
accessible location from which the entire system
can be switched off.
1. After connecting the system, check the direction of
rotation of the hot water circulation pump and the
washing station heater circulation pump (option).
Fuel line to external fuel tank
Note
The maximum permissible negative pressure in the fuel
line (measured between the fuel filter and fuel pump) is
0.4 bar.
The negative pressure depends on:
●
the pipeline length
●
the suction height
●
the control panels, branches and angles in the suc-
tion line (dotted line in the diagram)
●
the pipeline cross-section
Note
From +4 C, EL heating oil precipitates paraffin, which
accumulates on the inner wall of the pipe.
●
the viscosity of the heating oil (temperature-depend-
ent)
Measures against too high of negative pressure are:
●
Minimum inner pipe diameter 6 mm
●
short, preferably straight pipelines
●
In extreme cases, use a separate fuel line with feed
pump
●
Preheat heating oil, provide suction line with trace
heating
●
Maximum viscosity 4...6 cSt at 20 °C
●
If there is a risk of frost, use heating oil with additives
(flow improvers) (winter fuel oil).
Connect the washing station heater and start
operation
Note
A prerequisite for the correct functioning of the washing
station heater is that the washing station is designed by
the customer in accordance with KÄRCHER's recom-
mendations.
1. Connect the on-site pipes of the washing station
heater to the distributors in the device.
2. Mount the outdoor temperature sensor:
●
protected from direct sunlight (north of the equator
on the north side, south of the equator on the south
side),
●
protected from warm walls,
●
protected from warm air currents.
3. Connect the immersion pump for filling the washing
station heater to the filling valve (on the red distribu-
tor).
1
Flow line stop valve
2
Filling valve
4. Lay the return line from the filling valve of the blue
distributor to the tank with frost protection solution.
5. Open the flow stop valves and the filling valves.
6. Pump frost protection mixture into the system for
frost protection down to minus 25 °C.
7. Switch on the floor heating pump (see chapter "Con-
troller/Service menu").
8. Carry out the filling process until there are no more
bubbles in the return line.
9. Close the return filling valve (on the blue distributor)
and continue to fill in frost protection until the pres-
sure gauge shows approx. 1.5 bar.
10. Close the filling line stop valve.
11. Let the underfloor heating pump run for at least an-
other 15 minutes. If necessary, top up with frost pro-
tection until the pressure gauge shows 1.5 bar.
12. Remove the hose, collecting and disposing of the
remaining frost protection solution.
13. Check the hose and pipe connections for leaks.
14. Set the thermostatic mixing valve, see chapter "Set-
tings/Washing station heater",
Checking the oil level
1. The oil level on all high-pressure pumps must be be-
tween the MIN and MAX marks on the oil tank.
1
Cover
2
Oil tank
2. Cut off the tip of the oil tank cover on each high-
pressure pump.
Filling with operating materials
1. Fill with operating materials as described in the sec-
tion "Filling with operating materials".
Note
The softening salt is filled into the salt tank during the in-
itial startup of the base exchanger. Therefore, do not
add softening salt yet.
Summary of Contents for SB MB
Page 39: ...Deutsch 39 Ma blatt Variante CAB SB MB Standard SB MB Comfort...
Page 40: ...40 Deutsch Ma blatt Variante SKID SB MB Standard SB MB Comfort...
Page 41: ...Deutsch 41 Ma blatt Variante SKID mit Anbausatz WSO...
Page 80: ...80 English Dimension sheet variant CAB SB MB standard SB MB comfort...
Page 81: ...English 81 Dimension sheet variant SKID SB MB standard SB MB comfort...
Page 82: ...82 English Dimension sheet variant SKID with attachment kit WSO...
Page 123: ...Fran ais 123 Fiche de dimensions variante CAB SB MB Standard SB MB Comfort...
Page 124: ...124 Fran ais Fiche de dimensions variante SKID SB MB Standard SB MB Comfort...
Page 125: ...Fran ais 125 Fiche de dimensions variante SKID avec kit de montage WSO...
Page 165: ...Italiano 165 Scheda dimensionale variante CAB SB MB Standard SB MB Comfort...
Page 166: ...166 Italiano Scheda dimensionale variante SKID SB MB Standard SB MB Comfort...
Page 167: ...Italiano 167 Scheda dimensionale variante SKID con kit di fissaggio WSO...
Page 206: ...206 Nederlands Maatblad variant CAB SB MB standaard SB MB comfort...
Page 207: ...Nederlands 207 Maatblad variant SKID SB MB standaard SB MB comfort...
Page 208: ...208 Nederlands Maatblad variant SKID met aanbouwset WSO...
Page 248: ...248 Espa ol Hoja de medidas variante CAB SB MB Standard SB MB Comfort...
Page 249: ...Espa ol 249 Hoja de medidas variante SKID SB MB Standard SB MB Comfort...
Page 250: ...250 Espa ol Hoja de medidas variante SKID con juego de montaje WSO...
Page 289: ...Svenska 289 M ttblad variant CAB SB MB Standard SB MB Comfort...
Page 290: ...290 Svenska M ttblad variant SKID SB MB Standard SB MB Comfort...
Page 291: ...Svenska 291 M ttblad variant SKID med p byggnadssats WSO...
Page 330: ...330 Suomi Mittalehti versio CAB SB MB Standard SB MB Comfort...
Page 331: ...Suomi 331 Mittalehti versio SKID SB MB Standard SB MB Comfort...
Page 332: ...332 Suomi Mittalehti versio SKID liit nt sarjalla WSO...
Page 337: ...337 2 3 4 2 A 3 3 Powerschaum STOP 1 SB MB Comfort 2 SB MB Comfort 3 SB MB Standard 4 5 6...
Page 353: ...353 1 2 2 3 4 5 6 1 7 8 9 10 11 12 13 2 3 4...
Page 354: ...354 1 2 2 3 4 5 6 1 7 8 9 10 11 3 2 3 4 1 2 3 4 5 6 7 8 9 10 11...
Page 355: ...355 SB MB Standard SB MB Comfort RO RO RO RO RO 4 60 C 0 OFF 1 2 K RCHER K RCHER...
Page 358: ...358 SB MB 6 419 070 0 25 C 0 07 0 15 MPa 0 7 1 5 bar 0 5 l min 0 0 5 l min 2 WZ 30 mm 5 C ABS...
Page 360: ...360 1000 WSO Power Power WSO RO 5...
Page 364: ...364 1 2 3 10 C F0144 S5...
Page 365: ...365 1...
Page 366: ...366 1 1 2 3 0 6 mm 4 1 3 mm 5 6 7 8 0 25 MPa 2 5 bar WAT S 202 WAT S 202 2...
Page 367: ...367 0 3 MPa 3 bar RO RO RO RO RO...
Page 373: ...373 CAB SB MB Standard SB MB Comfort...
Page 374: ...374 SKID SB MB Standard SB MB Comfort...
Page 375: ...375 SKID WSO...
Page 376: ...376...
Page 381: ...381 1 2 3 4 5 6 7 8 2 9 1 10 11 12 13 14 1 0 4 0 5 4 5 1 2 3 4 1 DP 1 2 DP 2 3 DP 3 4 DP 4 1 0...
Page 384: ...384 1 2 1 2 3 4 5 6 7 8 9 10 1 1 2 1 2 3 4 5 6 7 8 9 10 Home 1 2 3 4 5 6 Home 7 1 8 2 2 1 2...
Page 391: ...391 1 1 1 1 1 1 2 3 2 3 4 1 0 OFF 1 1 ON 2 3 1 2 1 2 3 4 5 6 7 8 9...
Page 394: ...394 1 2 3 4 5 6 7 8 9 10 11 12 13 1 2 3 4 5 6 7 8 9 10 1 2 48 3 4 24 48 5 6 7 8 1 80 100 2 3...
Page 395: ...395 B C 1 2 3 4 5 6 7 8 9 10 1 11 1 12 13 14 15 16 17 1 2 3 4 5 6 7 8 9 10 11 12 13 14 15...
Page 397: ...397 1 2 2 3 4 5 6 1 7 8 9 10 11 12 13 2 3 4...
Page 398: ...398 1 2 2 3 4 5 6 1 7 8 9 10 11 3 2 3 4 1 2 3 4 5 6 7 8 9 10 11...
Page 399: ...399 SB MB Standard SB MB Comfort 4 60 0 OFF 1 2 K RCHER K RCHER...
Page 401: ...401 1 2 3 WSO 1 6 1 1 6 2 1 2 1 2 3 1 2 3 4 5 6 1 IP 2 3 4 1 1 2 3 4 1 2 3 4...
Page 402: ...402 SB MB 6 419 070 0 25 C 0 07 0 15 0 7 1 5 0 5 0 0 5 2 30 5 C...
Page 404: ...404 200 9 10 90 100 0 5 5 25 6 288 055 0 6 288 072 6 288 116 1000 WSO WSO...
Page 408: ...408 10 C F0144...
Page 409: ...409 1 2 3 S5 1...
Page 410: ...410 1 1 3 0 6 4 1 3 5 6 7 8 0 25 2 5 WAT S 202 WAT S 202 2...
Page 411: ...411 0 3 3...
Page 417: ...417 CAB SB MB Standard SB MB Comfort...
Page 418: ...418 SKID SB MB Standard SB MB Comfort...
Page 419: ...419 SKID WSO...
Page 420: ...420...
Page 422: ......
Page 423: ......