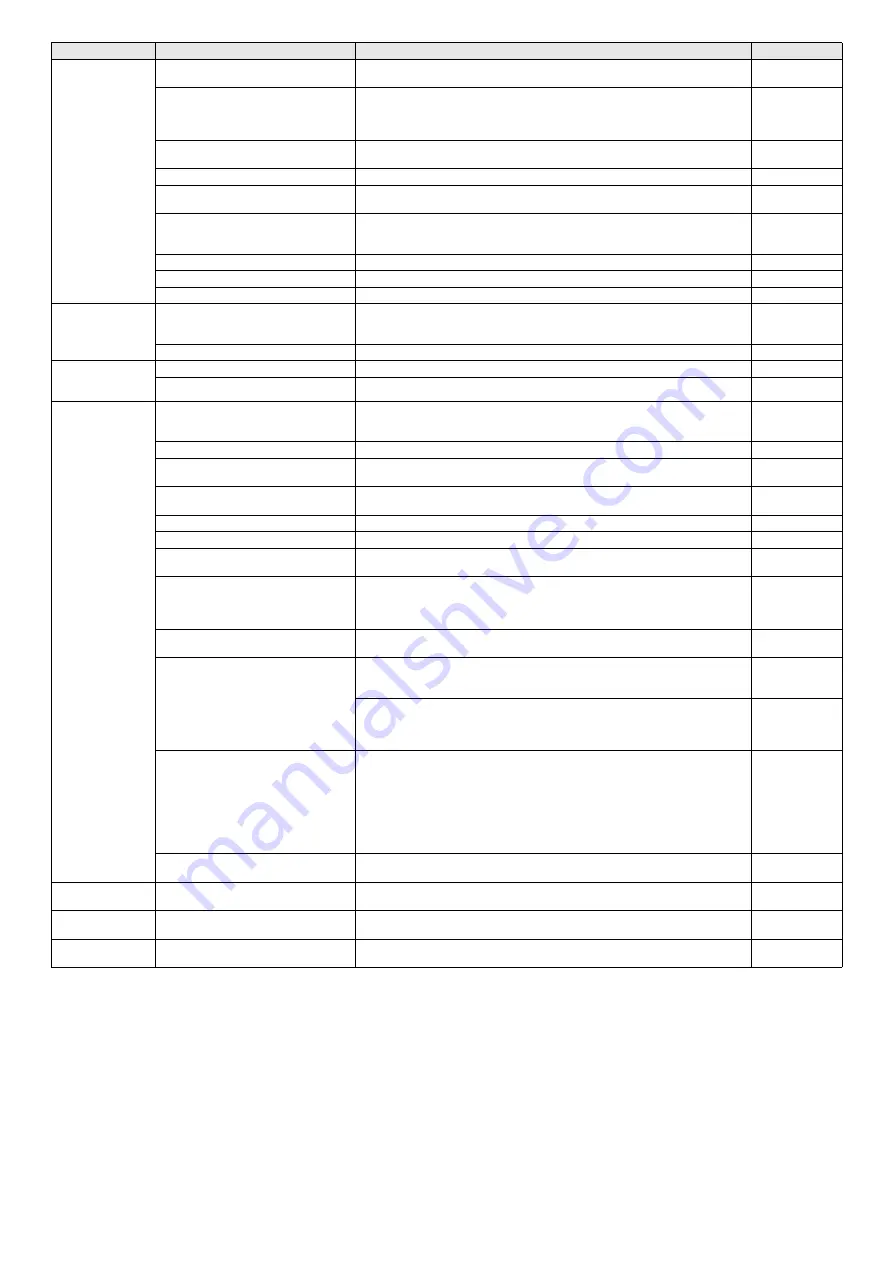
English
67
Daily
Check the high-pressure hoses,
Check the foam hoses (for 2-WZ version)
Examine the high-pressure hoses for mechanical damage such as abrasion damage,
visible hose fabric, kinks and cracked rubber. Replace damage high-pressure hoses.
Operator
Check the washing brushes.
Check the washing brushes for damage, soiling and wear. Replace bristles that are
shorter than 30 mm. In winter at temperatures below –5 °C, check for ice formation
and lock the foam wash if necessary. Replace the combination spray lance with a high-
pressure spray lance for this.
Operator
Check the information notices at the wash-
ing station.
Check that the user information notices are present and legible.
Operator
Check the washing station lighting
Check the function of the washing station lighting, replace defective lamps.
Operator
Check the spray lances
Check for tightness, replace the O-ring if necessary. Nozzle protection and grip tube
OK? Replace if necessary.
Operator
Check the high-pressure guns
Check for tightness, replace the O-ring if necessary. Is the high-pressure hose rotata-
ble and the lever smooth-running? Lubricate if necessary (see section "Maintenance
work").
Operator
Check the tool storage trough
Check from the outside for foreign bodies and dirt. Remove coarse contamination.
Operator
Check the detergent filling level.
Check the filling level and top up if necessary.
Operator
Emptying the coin box
Open the coin acceptor door and empty the coin box.
Operator
daily at first, later ac-
cording to experience
Check the fuel tank filling level
Is the heating oil supply sufficient until the next inspection? Take into account in-
creased consumption due to frost protection devices. Lack of fuel leads to failure and
damage to the system.
Operator
Empty the compressor
Drain the condensation water from the compressor's pressure tank.
Operator
For systems with frost
protection: Daily in the
case of frost
Check the frost protection devices.
Are the hot air blowers in operation (also in the ABS fuel tank, option)?
Operator
Clean the frost protection pump filter
Clean the filter and re-insert.
Operator
After 40 operating
hours or weekly
Check the leak-tightness of the system
Check pump and line system for leaks. Contact Customer Service when oil is present
under the high-pressure pump or when more than 3 drops of water per minute escape
from the high-pressure pump during operation.
Operator
Check the oil level
Milky oil indicates water in the oil. Contact customer service.
Operator
Check the oil level of the high-pressure
pumps
The oil level must lie between the MIN and MAX marks, otherwise refill with oil.
Operator
Checking detergent filter
Visually check the high-pressure jet for the presence of detergent, clean detergent fil-
ter if necessary.
Operator
Check for correction function
Checking the functionality of all washing programs
Operator
Check the salt supply in the salt tank
Is the salt level above the water level? Top up the softening salt if necessary.
Operator
Check the residual hardness of the sof-
tened water
Remove water from the hot water float tank and determine the residual hardness with
test set B (order no. 6.768-003). Target value: Less than 3 °dH.
Operator
Check residual chlorine content after ac-
tive carbon filter
This test is only necessary if the chlorine content in the fresh water is above 0.3 mg/l.
Take a water sample between the active carbon filter and the RO membrane. Deter-
mine the residual chlorine content. If the residual chlorine content of the water sample
exceeds 0.1 mg/l, replace the active carbon filter.
Operator
Briefly switch on the washing station heat-
er
Activate the frost protection pump as described for "Controller/menu Service".
Operator
Clean the outside of the housing (stainless
steel and plastic)
Mix a 10% solution of the "Washing hall and tile cleaner RM 841" detergent, apply to
the surfaces, allow to react for approx. 2 to 3 minutes, do not allow to dry. After the
contact time, rinse thoroughly with the high-pressure jet.
Operator
Mix a 20% solution of "Washing Hall and Tile Cleaner RM 841" detergent, apply to the
surface and allow to react for approx. 2 to 3 minutes. After the contact time, clean the
surfaces with a damp pad or microfibre cloth and then rinse thoroughly with a high-
pressure jet. If desired, the large surfaces can be wiped off with a rubber squeegee.
Operator
Cleaning the splash guard tarpaulins
Mix a 10% solution of the "Washing hall and tile cleaner RM 841" detergent, apply to
the surfaces, allow to react for approx. 2 to 3 minutes, do not allow to dry. After the
contact time, rinse thoroughly with the high-pressure jet.
ATTENTION
Risk of damage
Solvents and detergents containing solvents can damage the splash guard tarpaulins.
Do not clean the splash guard tarpaulins with solvents or detergents containing sol-
vents.
Operator
Maintain the casing exterior (stainless
steel)
Treat with stainless steel care product as required.
Operator
weekly during frost
Check the heating ABS fuel oil tank (op-
tion)
Below 3 °C, check whether the trace heating of the fuel oil line between the heating oil
tank and SB MB is warm.
Operator
Once, 1 month after
initial startup
Changing the WSO fine filter
Shut off the fresh water inlet, unscrew the filter cup, replace the filter insert, refit the
new filter insert and filter cup, open the fresh water inlet.
Operator
After 80 operating
hours or fortnightly
Clean and preserve the stainless steel
parts of the housing.
Remove dirt residues and deposits. Preserve parts with stainless steel care oil.
Operator
Time & date
Activity
Performed
By whom
Summary of Contents for SB MB
Page 39: ...Deutsch 39 Ma blatt Variante CAB SB MB Standard SB MB Comfort...
Page 40: ...40 Deutsch Ma blatt Variante SKID SB MB Standard SB MB Comfort...
Page 41: ...Deutsch 41 Ma blatt Variante SKID mit Anbausatz WSO...
Page 80: ...80 English Dimension sheet variant CAB SB MB standard SB MB comfort...
Page 81: ...English 81 Dimension sheet variant SKID SB MB standard SB MB comfort...
Page 82: ...82 English Dimension sheet variant SKID with attachment kit WSO...
Page 123: ...Fran ais 123 Fiche de dimensions variante CAB SB MB Standard SB MB Comfort...
Page 124: ...124 Fran ais Fiche de dimensions variante SKID SB MB Standard SB MB Comfort...
Page 125: ...Fran ais 125 Fiche de dimensions variante SKID avec kit de montage WSO...
Page 165: ...Italiano 165 Scheda dimensionale variante CAB SB MB Standard SB MB Comfort...
Page 166: ...166 Italiano Scheda dimensionale variante SKID SB MB Standard SB MB Comfort...
Page 167: ...Italiano 167 Scheda dimensionale variante SKID con kit di fissaggio WSO...
Page 206: ...206 Nederlands Maatblad variant CAB SB MB standaard SB MB comfort...
Page 207: ...Nederlands 207 Maatblad variant SKID SB MB standaard SB MB comfort...
Page 208: ...208 Nederlands Maatblad variant SKID met aanbouwset WSO...
Page 248: ...248 Espa ol Hoja de medidas variante CAB SB MB Standard SB MB Comfort...
Page 249: ...Espa ol 249 Hoja de medidas variante SKID SB MB Standard SB MB Comfort...
Page 250: ...250 Espa ol Hoja de medidas variante SKID con juego de montaje WSO...
Page 289: ...Svenska 289 M ttblad variant CAB SB MB Standard SB MB Comfort...
Page 290: ...290 Svenska M ttblad variant SKID SB MB Standard SB MB Comfort...
Page 291: ...Svenska 291 M ttblad variant SKID med p byggnadssats WSO...
Page 330: ...330 Suomi Mittalehti versio CAB SB MB Standard SB MB Comfort...
Page 331: ...Suomi 331 Mittalehti versio SKID SB MB Standard SB MB Comfort...
Page 332: ...332 Suomi Mittalehti versio SKID liit nt sarjalla WSO...
Page 337: ...337 2 3 4 2 A 3 3 Powerschaum STOP 1 SB MB Comfort 2 SB MB Comfort 3 SB MB Standard 4 5 6...
Page 353: ...353 1 2 2 3 4 5 6 1 7 8 9 10 11 12 13 2 3 4...
Page 354: ...354 1 2 2 3 4 5 6 1 7 8 9 10 11 3 2 3 4 1 2 3 4 5 6 7 8 9 10 11...
Page 355: ...355 SB MB Standard SB MB Comfort RO RO RO RO RO 4 60 C 0 OFF 1 2 K RCHER K RCHER...
Page 358: ...358 SB MB 6 419 070 0 25 C 0 07 0 15 MPa 0 7 1 5 bar 0 5 l min 0 0 5 l min 2 WZ 30 mm 5 C ABS...
Page 360: ...360 1000 WSO Power Power WSO RO 5...
Page 364: ...364 1 2 3 10 C F0144 S5...
Page 365: ...365 1...
Page 366: ...366 1 1 2 3 0 6 mm 4 1 3 mm 5 6 7 8 0 25 MPa 2 5 bar WAT S 202 WAT S 202 2...
Page 367: ...367 0 3 MPa 3 bar RO RO RO RO RO...
Page 373: ...373 CAB SB MB Standard SB MB Comfort...
Page 374: ...374 SKID SB MB Standard SB MB Comfort...
Page 375: ...375 SKID WSO...
Page 376: ...376...
Page 381: ...381 1 2 3 4 5 6 7 8 2 9 1 10 11 12 13 14 1 0 4 0 5 4 5 1 2 3 4 1 DP 1 2 DP 2 3 DP 3 4 DP 4 1 0...
Page 384: ...384 1 2 1 2 3 4 5 6 7 8 9 10 1 1 2 1 2 3 4 5 6 7 8 9 10 Home 1 2 3 4 5 6 Home 7 1 8 2 2 1 2...
Page 391: ...391 1 1 1 1 1 1 2 3 2 3 4 1 0 OFF 1 1 ON 2 3 1 2 1 2 3 4 5 6 7 8 9...
Page 394: ...394 1 2 3 4 5 6 7 8 9 10 11 12 13 1 2 3 4 5 6 7 8 9 10 1 2 48 3 4 24 48 5 6 7 8 1 80 100 2 3...
Page 395: ...395 B C 1 2 3 4 5 6 7 8 9 10 1 11 1 12 13 14 15 16 17 1 2 3 4 5 6 7 8 9 10 11 12 13 14 15...
Page 397: ...397 1 2 2 3 4 5 6 1 7 8 9 10 11 12 13 2 3 4...
Page 398: ...398 1 2 2 3 4 5 6 1 7 8 9 10 11 3 2 3 4 1 2 3 4 5 6 7 8 9 10 11...
Page 399: ...399 SB MB Standard SB MB Comfort 4 60 0 OFF 1 2 K RCHER K RCHER...
Page 401: ...401 1 2 3 WSO 1 6 1 1 6 2 1 2 1 2 3 1 2 3 4 5 6 1 IP 2 3 4 1 1 2 3 4 1 2 3 4...
Page 402: ...402 SB MB 6 419 070 0 25 C 0 07 0 15 0 7 1 5 0 5 0 0 5 2 30 5 C...
Page 404: ...404 200 9 10 90 100 0 5 5 25 6 288 055 0 6 288 072 6 288 116 1000 WSO WSO...
Page 408: ...408 10 C F0144...
Page 409: ...409 1 2 3 S5 1...
Page 410: ...410 1 1 3 0 6 4 1 3 5 6 7 8 0 25 2 5 WAT S 202 WAT S 202 2...
Page 411: ...411 0 3 3...
Page 417: ...417 CAB SB MB Standard SB MB Comfort...
Page 418: ...418 SKID SB MB Standard SB MB Comfort...
Page 419: ...419 SKID WSO...
Page 420: ...420...
Page 422: ......
Page 423: ......