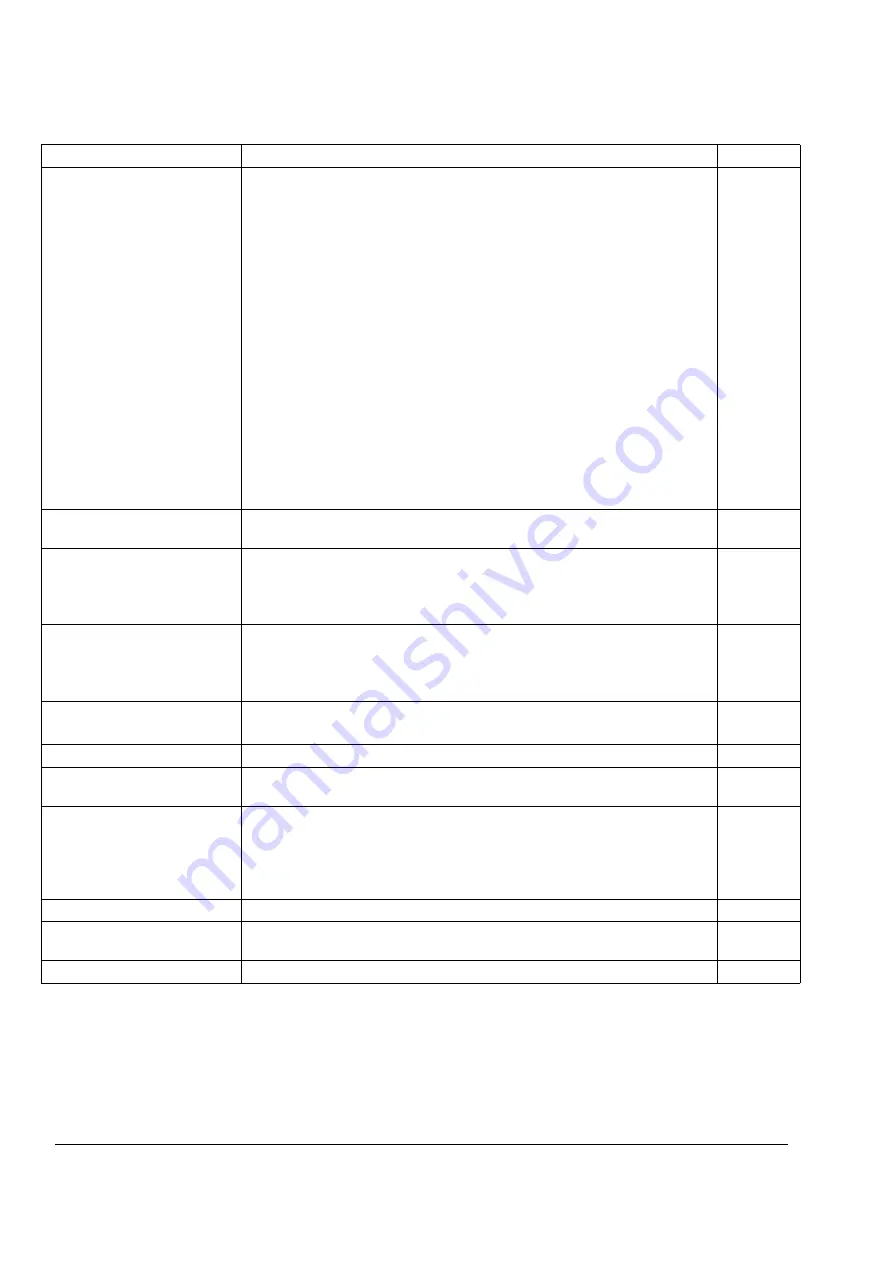
Actual signals and parameters
226
SCALAR
Scalar control is suitable in special cases where the DTC cannot be applied.
The Scalar control mode is recommended:
- for multimotor drives with variable number of motors
- when the nominal current of the motor is less than 1/6 of the nominal output
current of the drive (inverter)
- the drive is used for test purposes with no motor connected.
Note:
The outstanding motor control accuracy of the DTC cannot be achieved
in Scalar control. The differences between the scalar and DTC control modes
are pointed out in this manual in relevant parameter lists. There are some
standard features that are disabled in the Scalar control mode: Motor
identification run (group
), Speed Limits (group
), Torque Limit (group
), DC hold (group
), Speed Controller Tuning (group
), Torque Control (group
), Flux optimisation
(group
), Flux braking (group
),
Underload Function (group
), Motor phase loss
Protection (group
), Motor Stall protection (group
).
For more information, see section
on page
65535
99.05
MOTOR NOM
VOLTAGE
Defines the nominal motor voltage. Must be equal to the value on the motor
rating plate.
1/2 … 2 · UN
Voltage. Allowed range is 1/2 … 2 ·
U
N
of the drive.
Note:
The stress on the motor insulations is always dependent on the drive
supply voltage. This also applies to the case where the motor voltage rating is
lower than the rating of the drive and the supply of the drive.
1 = 1 V
99.06
MOTOR NOM
CURRENT
Defines the nominal motor current. Must be equal to the value on the motor
rating plate.
Note:
Correct motor run requires that the magnetizing current of the motor
does not exceed 90 percent of the nominal current of the inverter.
0 … 2 · I
2hd
Allowed range: approx. 1/6 … 2 ·
I
2hd
of ACS800 (parameter
= DTC).
Allowed range: approx. 0 … 2 ·
I
2hd
of ACS800 (parameter
= SCALAR).
1 = 0.1 A
99.07
MOTOR NOM FREQ
Defines the nominal motor frequency.
8 … 300 Hz
Nominal frequency (50 or 60 Hz typically)
800 …
30000
99.08
MOTOR NOM SPEED Defines the nominal motor speed. Must be equal to the value on the motor
rating plate. The motor synchronous speed or another approximate value must
not be given instead!
Note:
If the value of parameter
is changed, the speed limits in parameter
change automatically as well.
1 … 18000 rpm
Nominal motor speed
1 … 18000
99.09
MOTOR NOM
POWER
Defines the nominal motor power. Set exactly as on the motor rating plate.
0 … 9000 kW
Nominal motor power
0 … 90000
Index
Name/Selection
Description
FbEq
Summary of Contents for ACS 800 Series
Page 1: ...ACS800 Firmware Manual Crane Control Program N697 ...
Page 4: ......
Page 26: ...Start up and control through the I O interface 26 ...
Page 36: ...Quick start up guide 36 ...
Page 52: ...Control panel 52 ...
Page 105: ...Program features 105 Figure Control diagram for Shaft synchronisation executed in 20 ms ...
Page 128: ...Program features 128 ...
Page 150: ...Application macros control location EXT1 EXT2 150 ...
Page 228: ...Actual signals and parameters 228 ...
Page 299: ...Adaptive Programming examples for crane control 299 ...
Page 305: ...Adaptive Programming examples for crane control 305 ...
Page 318: ...Analogue Extension Module 318 ...
Page 332: ...Additional data actual signals and parameters 332 ...
Page 334: ...DriveWindow 334 ...
Page 335: ...Control block diagrams 335 Control block diagrams ...
Page 336: ...Control block diagrams 336 ...
Page 337: ...Control block diagrams 337 ...
Page 338: ...Control block diagrams 338 ...
Page 340: ...www abb com drives www abb com drivespartners Contact us 3AFE68775230 Rev E EN 2012 09 25 ...