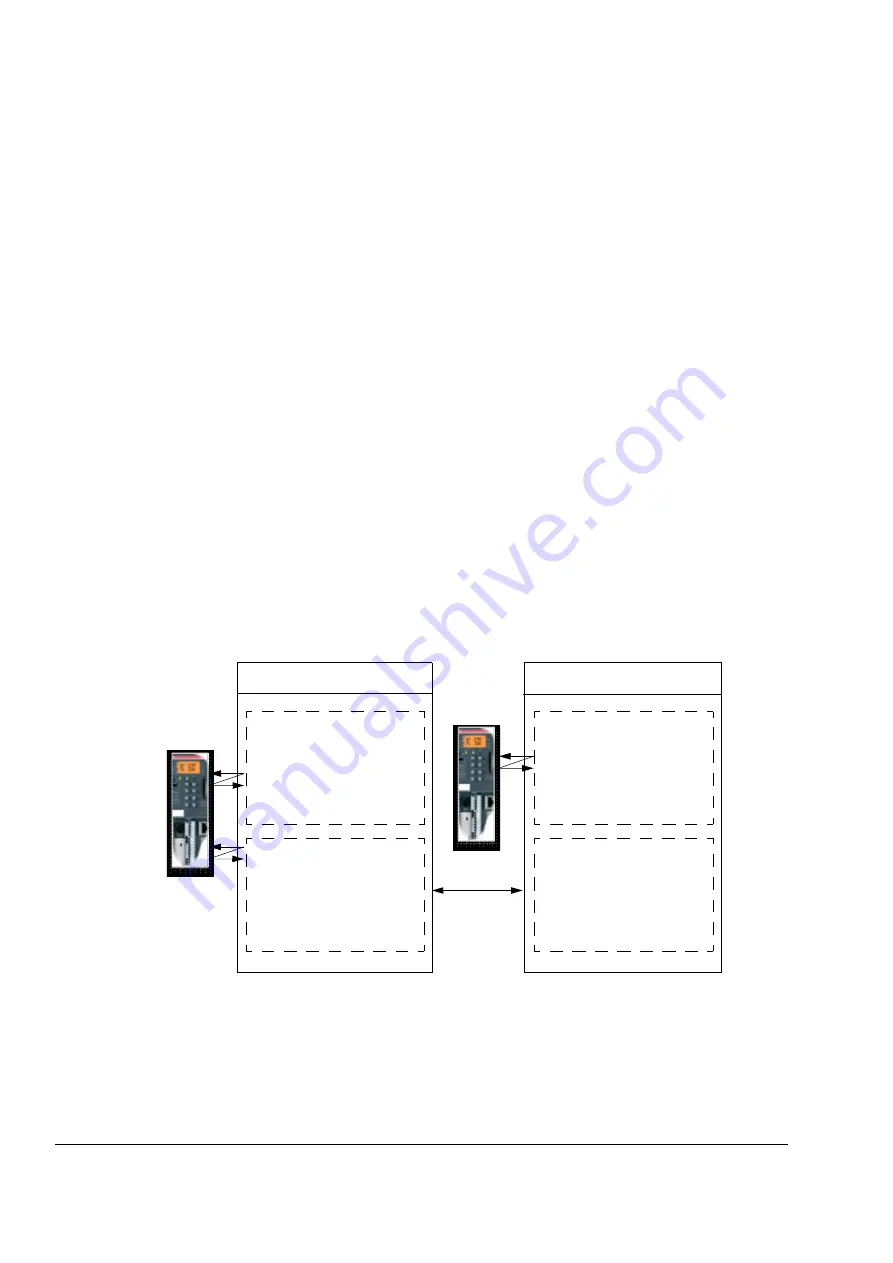
Fieldbus control
256
Fieldbus references in a Master/Follower configuration
When the ABB Drives communication profile is active, the fieldbus interface uses the
following references in the Master drive:
• When the Master is in control location EXT1 (stand-alone, speed-controlled), the
fieldbus interface uses REF1 for the speed reference.
• When the Master is in control location EXT2 (Master/Follower, either speed-
controlled or torque-controlled depending on the selection of Par.
TORQUE
SELECTOR), the fieldbus interface uses REF2 for the speed or torque reference.
When the ABB Drives communication profile is active, the fieldbus interface uses the
following references in the Follower drives:
• When Follower n is in control location EXT1 (stand-alone, speed-controlled), the
fieldbus interface uses REF1 for the speed reference.
Note
: For the fieldbus interface to work in follower drives in EXT1, Par.
MASTER LINK MODE must be set to value NOT IN USE in the follower drives.
Ensure this either through the fieldbus (parameter writing) or DriveAP's Write
block.
• When Follower n is in control location EXT2 (Master/Follower, either speed-
controlled or torque-controlled depending on the selection of Par.
TORQUE
SELECTOR), the fieldbus interface cannot control the references because they
come through the M/F link (CH).
The figure below illustrates the use of fieldbus references in a Master/Follower
configuration.
Follower n
Master
CH2
EXT 1
Stand-alone mode
EXT1 STRT/STP/DIR
EXT REF1 SELECT
EXT 2
Master/Follower
EXT2 STRT/STP/DIR
EXT REF2 SELECT
EXT 1
Stand-alone mode
EXT1 STRT/STP/DIR
EXT REF1 SELECT
EXT 2
Master/Follower
EXT2 STRT/STP/DIR
EXT REF2 SELECT
Note
: In follower drives in EXT1,
Par.
must have value NOT IN
USE for the fieldbus interface to
work.
Summary of Contents for ACS 800 Series
Page 1: ...ACS800 Firmware Manual Crane Control Program N697 ...
Page 4: ......
Page 26: ...Start up and control through the I O interface 26 ...
Page 36: ...Quick start up guide 36 ...
Page 52: ...Control panel 52 ...
Page 105: ...Program features 105 Figure Control diagram for Shaft synchronisation executed in 20 ms ...
Page 128: ...Program features 128 ...
Page 150: ...Application macros control location EXT1 EXT2 150 ...
Page 228: ...Actual signals and parameters 228 ...
Page 299: ...Adaptive Programming examples for crane control 299 ...
Page 305: ...Adaptive Programming examples for crane control 305 ...
Page 318: ...Analogue Extension Module 318 ...
Page 332: ...Additional data actual signals and parameters 332 ...
Page 334: ...DriveWindow 334 ...
Page 335: ...Control block diagrams 335 Control block diagrams ...
Page 336: ...Control block diagrams 336 ...
Page 337: ...Control block diagrams 337 ...
Page 338: ...Control block diagrams 338 ...
Page 340: ...www abb com drives www abb com drivespartners Contact us 3AFE68775230 Rev E EN 2012 09 25 ...