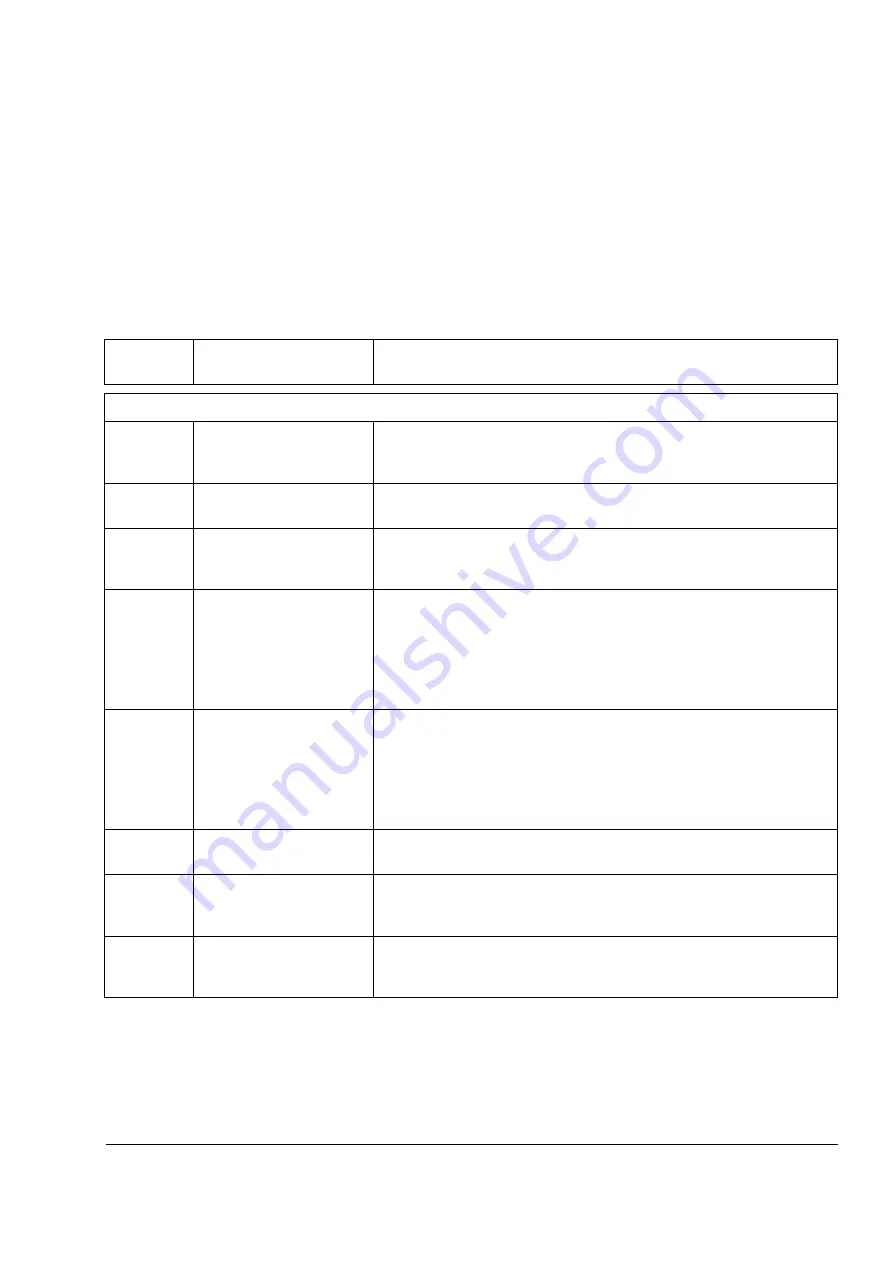
Fieldbus control
237
Drive control parameters
After the fieldbus communication has been set up, the drive control parameters
listed in the table below must be checked and adjusted where necessary.
The
Setting for fieldbus control
column gives the value to use when the fieldbus
interface is the desired source or destination for that particular signal. The
Function/Information
column gives a description of the parameter.
The fieldbus signal routes and message composition are explained later in section
The fieldbus control interface
Parameter
Setting for
fieldbus control
Function/Information
CONTROL COMMAND SOURCE SELECTION
COMM.CW
Enables the fieldbus Control Word (except 03.01 Main Control Word bits 3
and 11) when EXT1 is selected as the active control location. See also par.
10.07.
COMM.CW
Enables the fieldbus Control Word (except 03.01 Main Control Word bits 3
and 11) when EXT2 is selected as the active control location.
FORWARD
REVERSE or
REQUEST
Enables rotation direction control as defined with parameters 10.01 and
10.02. The direction control is explained in section
page
0 or 1
Setting the value to 1 overrides the setting of par. 10.01 so that the fieldbus
Control Word (except 03.01 Main Control Word bit 11) is enabled when
EXT1 is selected as the active control location.
Note 1:
Only visible with the Generic Drive communication profile selected
(see par. 98.07).
Note 2:
Setting not saved into permanent memory.
0 or 1
Setting the value to 1 overrides the setting of par. 11.03 so that Fieldbus
reference REF1 is used when EXT1 is selected as the active control
location.
Note 1:
Only visible with the Generic Drive communication profile selected
(see par. 98.07).
Note 2:
Setting not saved into permanent memory.
COMM.CW
Enables EXT1/EXT2 selection by fieldbus Control Word bit 11 EXT CTRL
LOC.
COMM. REF1
FAST COMM
Fieldbus reference REF1 is used when EXT1 is selected as the active
control location. See section
on page
for information on
the alternative settings.
COMM. REF2
FAST COMM
Fieldbus reference REF2 is used when EXT2 is selected as the active
control location. See section
on page
for information on
the alternative settings.
Summary of Contents for ACS 800 Series
Page 1: ...ACS800 Firmware Manual Crane Control Program N697 ...
Page 4: ......
Page 26: ...Start up and control through the I O interface 26 ...
Page 36: ...Quick start up guide 36 ...
Page 52: ...Control panel 52 ...
Page 105: ...Program features 105 Figure Control diagram for Shaft synchronisation executed in 20 ms ...
Page 128: ...Program features 128 ...
Page 150: ...Application macros control location EXT1 EXT2 150 ...
Page 228: ...Actual signals and parameters 228 ...
Page 299: ...Adaptive Programming examples for crane control 299 ...
Page 305: ...Adaptive Programming examples for crane control 305 ...
Page 318: ...Analogue Extension Module 318 ...
Page 332: ...Additional data actual signals and parameters 332 ...
Page 334: ...DriveWindow 334 ...
Page 335: ...Control block diagrams 335 Control block diagrams ...
Page 336: ...Control block diagrams 336 ...
Page 337: ...Control block diagrams 337 ...
Page 338: ...Control block diagrams 338 ...
Page 340: ...www abb com drives www abb com drivespartners Contact us 3AFE68775230 Rev E EN 2012 09 25 ...