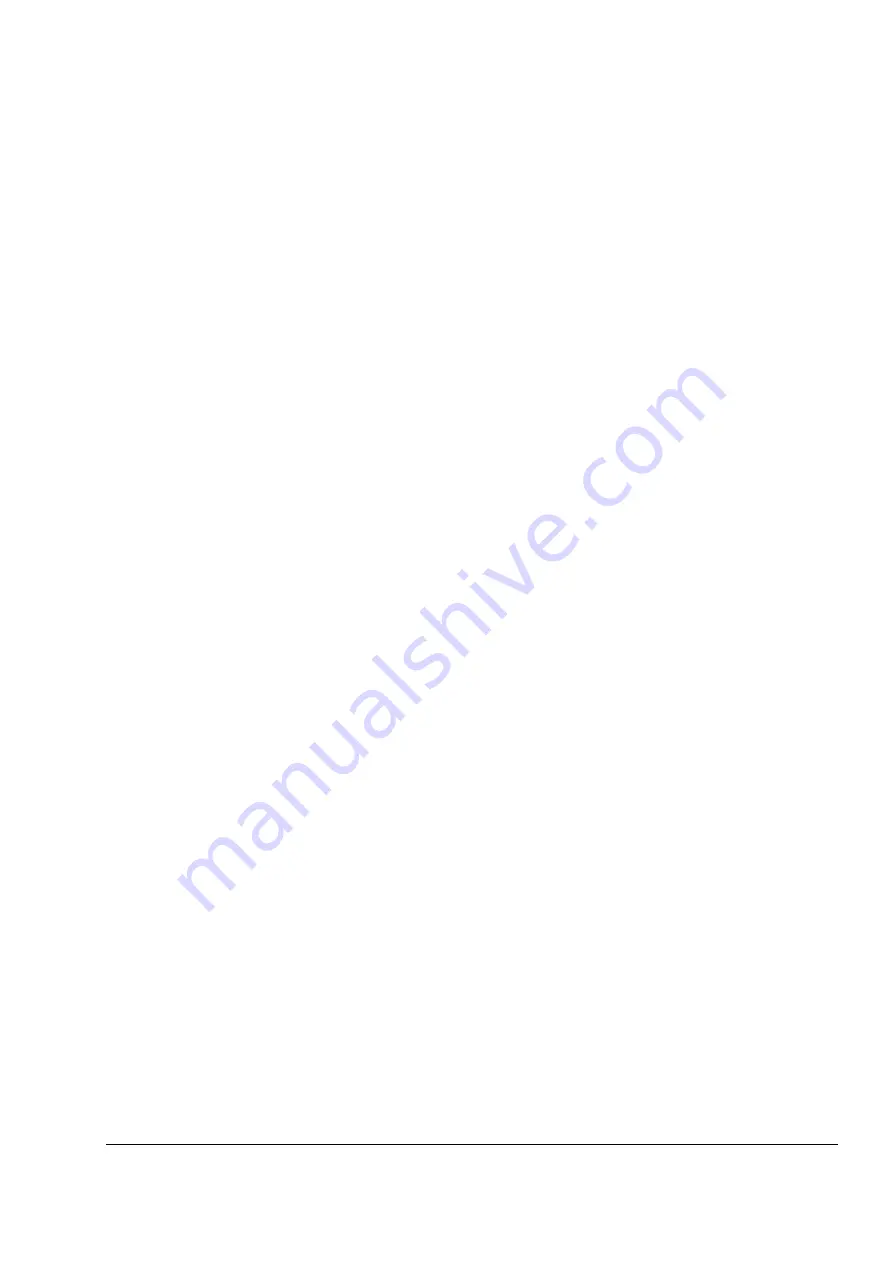
Program features
111
Examples of crane functionalities created with DriveAP
Main contactor control logic
Using Adaptive Programming (AP), you can create a main contactor control logic for
the 3-phase power supply of the ACS800 drive. With the help of the main contactor
control logic, the power supply of the drive is disabled when the crane is not used
(the standby energy-efficiency mode).
For an example how to create the AP file, see
Brake match
Brake match detects mechanical brake slips and downward movement of the load
when Mechanical brake control is in use, the operator has given the stop command
and the target is to close the brake. The slip detection is based on the motor encoder
position signal, and the function works only if an encoder is used. You can use the
function for an automatic restart of the crane or just for a warning (alarm) indication.
For an example how to create the AP file, see section
Redundancy in Master/Follower crane control
In the Master/Follower crane control, redundancy is implemented using a spare drive
unit that is ready to be used as a Master or a Follower. The spare unit usually
replaces the faulty Master or one of the Followers.
Adaptive Programming provides the ability to switch between the Master, Follower or
standby (spare unit) mode. This means that the Master and Follower are no longer
fixed, but can be changed when needed.
Using the Adaptive Programming (AP), you can create a redundancy control logic.
For an example how to create the AP file, see
Redundancy in Master/Follower crane
Scaling actual encoder position signal (mm) to analogue output as mA
The actual encoder position signal
POS ACT PPU (mm) can be scaled to
4 … 20 mA for analogue outputs and sent to other systems as an mA signal, for
example, for supervision or protection purposes.
Using Adaptive Programming (AP), you can create an AP file for scaling the actual
encoder position signal for an analogue output. For an example how to create the
AP file, see
Scaling actual encoder position signal (mm) to analogue output as mA
on page
Slack rope torque detection
Using Adaptive Programming (AP), you can create a function for detecting slackness
of the ropes on the drum. The detection is based on monitoring the motor torque. For
more information, see
Conical rotor motors
Using Adaptive Programming (AP), you can create a file for handling brake control of
conical rotor motors that do not have an external brake. With the help of Adaptive
Programming, the conical rotor motors can be used together with the Crane control
program. For more information, see
.
Summary of Contents for ACS 800 Series
Page 1: ...ACS800 Firmware Manual Crane Control Program N697 ...
Page 4: ......
Page 26: ...Start up and control through the I O interface 26 ...
Page 36: ...Quick start up guide 36 ...
Page 52: ...Control panel 52 ...
Page 105: ...Program features 105 Figure Control diagram for Shaft synchronisation executed in 20 ms ...
Page 128: ...Program features 128 ...
Page 150: ...Application macros control location EXT1 EXT2 150 ...
Page 228: ...Actual signals and parameters 228 ...
Page 299: ...Adaptive Programming examples for crane control 299 ...
Page 305: ...Adaptive Programming examples for crane control 305 ...
Page 318: ...Analogue Extension Module 318 ...
Page 332: ...Additional data actual signals and parameters 332 ...
Page 334: ...DriveWindow 334 ...
Page 335: ...Control block diagrams 335 Control block diagrams ...
Page 336: ...Control block diagrams 336 ...
Page 337: ...Control block diagrams 337 ...
Page 338: ...Control block diagrams 338 ...
Page 340: ...www abb com drives www abb com drivespartners Contact us 3AFE68775230 Rev E EN 2012 09 25 ...