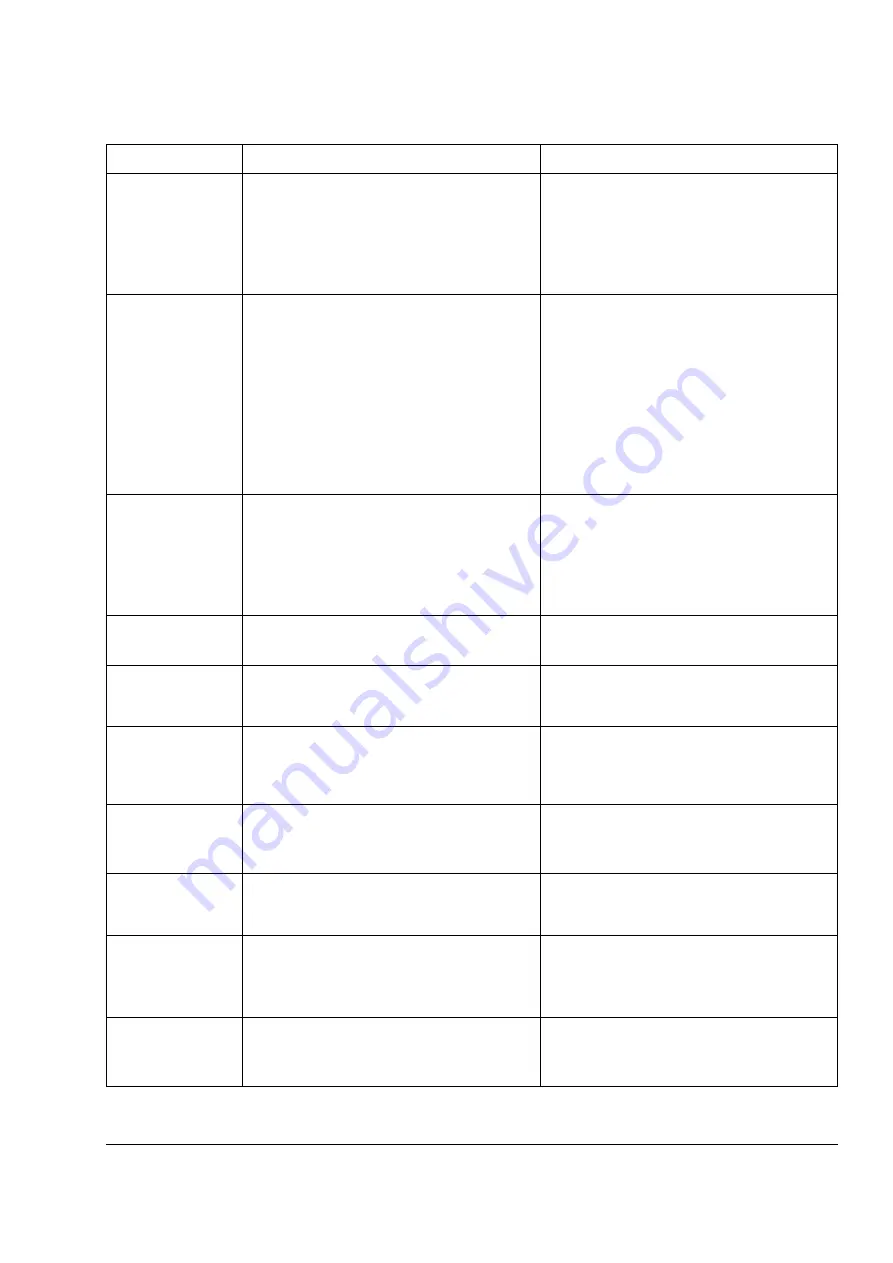
Fault tracing
285
MOT POW LIM
(FF86)
3.18 AW 5 bit 12
(programmable
Fault Function
Drive limits motor power according to limits
defined with parameters
and
.
Informative alarm
Check parameter
P MOTORING LIM
and
P GENERATING LIM settings.
Check Fault Function parameters.
MOT TORQ LIM
(FF85)
3.18 AW 5 bit 11
(programmable
Fault Function
Drive limits motor torque according to
calculated motor pull-out torque limit and
minimum and maximum torque limits defined
with parameters
and
.
Informative alarm
Check parameter
MIN TORQ SEL and
MAX TORQ SEL settings.
Check Fault Function parameters.
If LIMIT WORD 1 bit 0 TORQ MOTOR LIM
is 1,
- check motor parameter settings (parameter
group
- ensure that ID run has been completed
successfully.
PANEL LOSS
(5300)
3.09 AW 2 bit 13
(programmable
Fault Function
Control panel selected as active control
location for drive has ceased communicating.
Check panel connection (see appropriate
hardware manual).
Check control panel connector.
Replace control panel in mounting platform.
Check Fault Function parameters.
POINTER ERROR
(FFD0)
Source selection (pointer) parameter points to
non existing parameter index.
Check source selection (pointer) parameter
settings.
->POWEROFF!
(FF39)
Inverter type (for example, sr0025_3) has been
changed. Inverter type is usually changed at
factory or during drive implementation.
Switch control board power off to validate
inverter type change.
PP OVERLOAD
(5482)
3.18 AW 5 bit 5
Excessive IGBT junction to case temperature.
This can be caused by excessive load at low
frequencies (for example, fast direction change
with excessive load and inertia).
Increase ramp time.
Reduce load.
REPLACE FAN
(4280)
3.18 AW 5 bit 0
Running time of inverter cooling fan has
exceeded its estimated life time.
Replace fan.
Reset fan run time counter
.
SLOW DOWN UP
(FFF4)
Slowdown signal
activated in the Up
direction
Run the motor in the opposite direction and
deactivate the Slowdown signal. Or let the
drive run in the limited speed reference.
SLOW DOWN
DOWN
(FFF5)
Slowdown signal
activated in the down
direction
Run the motor in the opposite direction and
deactivate the Slowdown signal. Or let the
drive run in the limited speed reference.
START INHIBI
(FF7A)
AW 1 bit 0
Optional start inhibit hardware logic is
activated.
Check start inhibit circuit (AGPS board).
WARNING
CAUSE
WHAT TO DO
Summary of Contents for ACS 800 Series
Page 1: ...ACS800 Firmware Manual Crane Control Program N697 ...
Page 4: ......
Page 26: ...Start up and control through the I O interface 26 ...
Page 36: ...Quick start up guide 36 ...
Page 52: ...Control panel 52 ...
Page 105: ...Program features 105 Figure Control diagram for Shaft synchronisation executed in 20 ms ...
Page 128: ...Program features 128 ...
Page 150: ...Application macros control location EXT1 EXT2 150 ...
Page 228: ...Actual signals and parameters 228 ...
Page 299: ...Adaptive Programming examples for crane control 299 ...
Page 305: ...Adaptive Programming examples for crane control 305 ...
Page 318: ...Analogue Extension Module 318 ...
Page 332: ...Additional data actual signals and parameters 332 ...
Page 334: ...DriveWindow 334 ...
Page 335: ...Control block diagrams 335 Control block diagrams ...
Page 336: ...Control block diagrams 336 ...
Page 337: ...Control block diagrams 337 ...
Page 338: ...Control block diagrams 338 ...
Page 340: ...www abb com drives www abb com drivespartners Contact us 3AFE68775230 Rev E EN 2012 09 25 ...