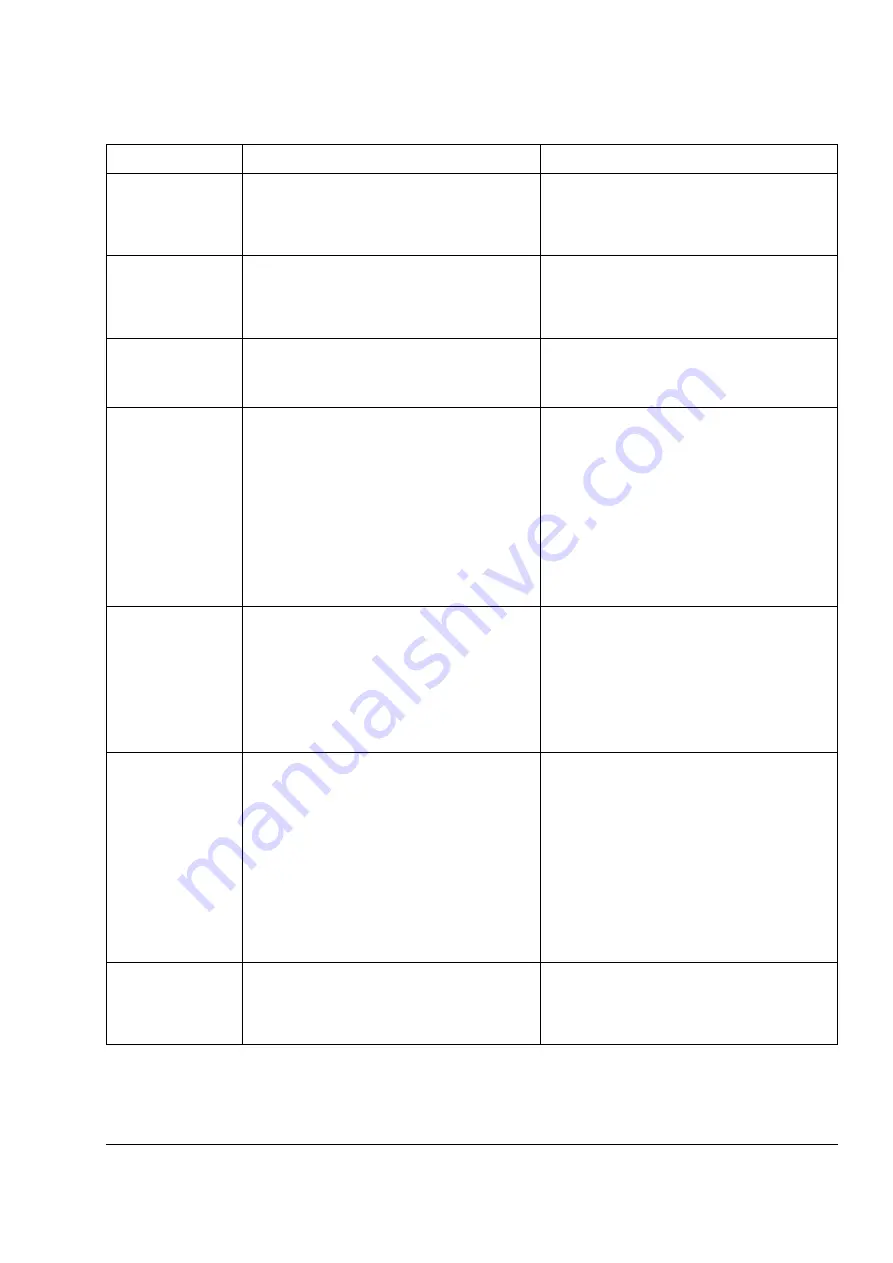
Fault tracing
293
MOTOR 1 TEMP
(4312)
3.15 FW 4 bit 1
Measured motor temperature has exceeded
fault limit set with parameter
.
Check value of fault limit.
Let motor cool down. Ensure proper motor
cooling: Check cooling fan, clean cooling
surfaces, etc.
MOTOR 2 TEMP
(4313)
3.15 FW 4 bit 2
Measured motor temperature has exceeded
fault limit set with parameter
.
Check value of fault limit.
Let motor cool down. Ensure proper motor
cooling: Check cooling fan, clean cooling
surfaces, etc.
NO MOT DATA
(FF52)
3.06 FW 2 bit 1
Motor data is not given or motor data does not
match with inverter data.
Check motor data parameters
…
.
OVERCURR xx
(2310)
3.05 FW 1 bit 1 and
4.01
Overcurrent fault in inverter unit of several
parallel connected inverter modules. xx (1...12)
refers to inverter module number.
Check motor load.
Check acceleration time.
Check motor and motor cable (including
phasing).
Check encoder cable (including phasing).
Check motor nominal values from group
to confirm that motor model
is correct.
Check that there are no power factor correction
or surge absorbers in motor cable.
OVERCURRENT
(2310)
3.05 FW 1 bit 1
Output current exceeds trip limit.
Check motor load.
Check acceleration time.
Check motor and motor cable (including
phasing).
Check that there are no power factor correction
capacitors or surge absorbers in motor cable.
Check encoder cable (including phasing).
OVERFREQ
(7123)
3.05 FW 1 bit 9
Motor is turning faster than highest allowed
speed due to incorrectly set minimum/
maximum speed, insufficient braking torque or
changes in load when using torque reference.
Trip level is 40 Hz over operating range
absolute maximum speed limit (the Direct
torque control mode active) or frequency limit
(Scalar control active). Operating range limits
are set with parameters
and
mode active) or
and
(Scalar
control active).
Check minimum/maximum speed settings.
Check adequacy of motor braking torque.
Check applicability of torque control.
Check need for brake chopper and resistor(s).
OVER SWFREQ
(FF55)
3.06 FW 2 bit 9
Switching frequency is too high.
Check motor parameter settings (parameter
group
Ensure that ID run has been completed
successfully.
FAULT
CAUSE
WHAT TO DO
Summary of Contents for ACS 800 Series
Page 1: ...ACS800 Firmware Manual Crane Control Program N697 ...
Page 4: ......
Page 26: ...Start up and control through the I O interface 26 ...
Page 36: ...Quick start up guide 36 ...
Page 52: ...Control panel 52 ...
Page 105: ...Program features 105 Figure Control diagram for Shaft synchronisation executed in 20 ms ...
Page 128: ...Program features 128 ...
Page 150: ...Application macros control location EXT1 EXT2 150 ...
Page 228: ...Actual signals and parameters 228 ...
Page 299: ...Adaptive Programming examples for crane control 299 ...
Page 305: ...Adaptive Programming examples for crane control 305 ...
Page 318: ...Analogue Extension Module 318 ...
Page 332: ...Additional data actual signals and parameters 332 ...
Page 334: ...DriveWindow 334 ...
Page 335: ...Control block diagrams 335 Control block diagrams ...
Page 336: ...Control block diagrams 336 ...
Page 337: ...Control block diagrams 337 ...
Page 338: ...Control block diagrams 338 ...
Page 340: ...www abb com drives www abb com drivespartners Contact us 3AFE68775230 Rev E EN 2012 09 25 ...