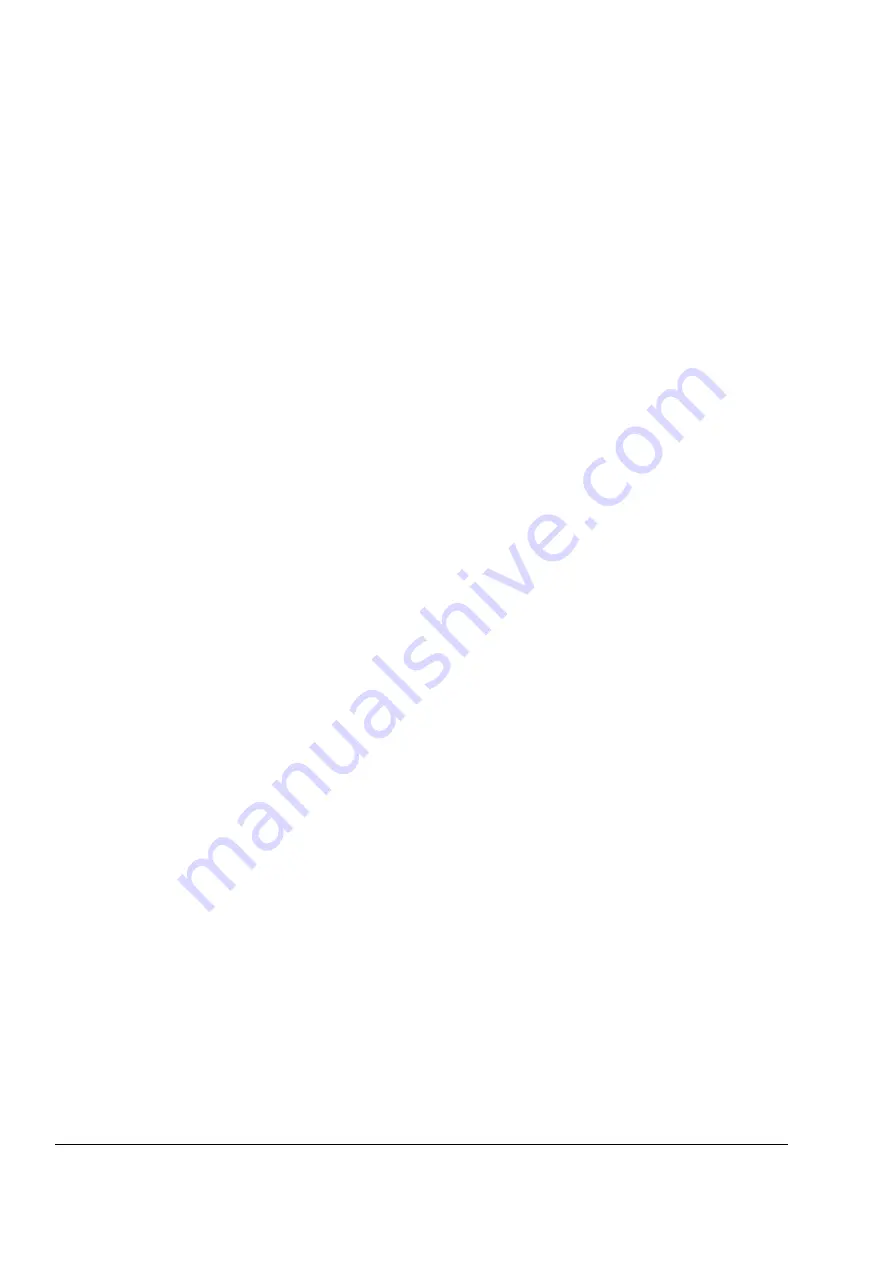
Program features
104
The position can be moved to a predefined value using the
. An
initial position value in mm can be entered in Par.
HOME POSITION to
initialize the actual position to the predefined value. The actual position is initialized
in the respective drives on completion of the homing sequence. Homing is possible
from EXT1 control location only. Therefore, after the homing sequence is done, the
control should be moved to EXT2 and a Synchro command given using Par.
.
Before the Synchro command is given, parameter
be selected.
If an offset of position is required in the Follower, set parameter
to OFFSET
and activate the Synchro command in the Follower when it is at the required
position. The difference in the position between the Master and the Follower when
the Synchro command is activated is taken as a constant offset in this case.
If an offset is not required in the Follower, set parameter
to DIRECT and
activate the Synchro command in the Follower. The difference in the position
between the Master and Follower when the Synchro command is activated is taken
as the position error in this case. The position error will be calculated with the new
position value with respect to the actual Master position.
Example
: Actual position value
is initialized with 1000 mm after a homing
sequence, and the drive is then moved to EXT2 control for synchronisation.
Consider the Master actual position received by Follower drive as 5000 mm. After a
Synchro command is given with parameter
SYNC CORR MODE as DIRECT,
the
SYNC POS ERROR will be (5000 … 1000) 4000 mm. If a Synchro
command is given with parameter
SYNC CORR MODE as OFFSET, the
SYNC POS ERR will be 0 mm, and the difference (5000 … 1000) 4000 mm will be
considered a permanent offset.
Summary of Contents for ACS 800 Series
Page 1: ...ACS800 Firmware Manual Crane Control Program N697 ...
Page 4: ......
Page 26: ...Start up and control through the I O interface 26 ...
Page 36: ...Quick start up guide 36 ...
Page 52: ...Control panel 52 ...
Page 105: ...Program features 105 Figure Control diagram for Shaft synchronisation executed in 20 ms ...
Page 128: ...Program features 128 ...
Page 150: ...Application macros control location EXT1 EXT2 150 ...
Page 228: ...Actual signals and parameters 228 ...
Page 299: ...Adaptive Programming examples for crane control 299 ...
Page 305: ...Adaptive Programming examples for crane control 305 ...
Page 318: ...Analogue Extension Module 318 ...
Page 332: ...Additional data actual signals and parameters 332 ...
Page 334: ...DriveWindow 334 ...
Page 335: ...Control block diagrams 335 Control block diagrams ...
Page 336: ...Control block diagrams 336 ...
Page 337: ...Control block diagrams 337 ...
Page 338: ...Control block diagrams 338 ...
Page 340: ...www abb com drives www abb com drivespartners Contact us 3AFE68775230 Rev E EN 2012 09 25 ...