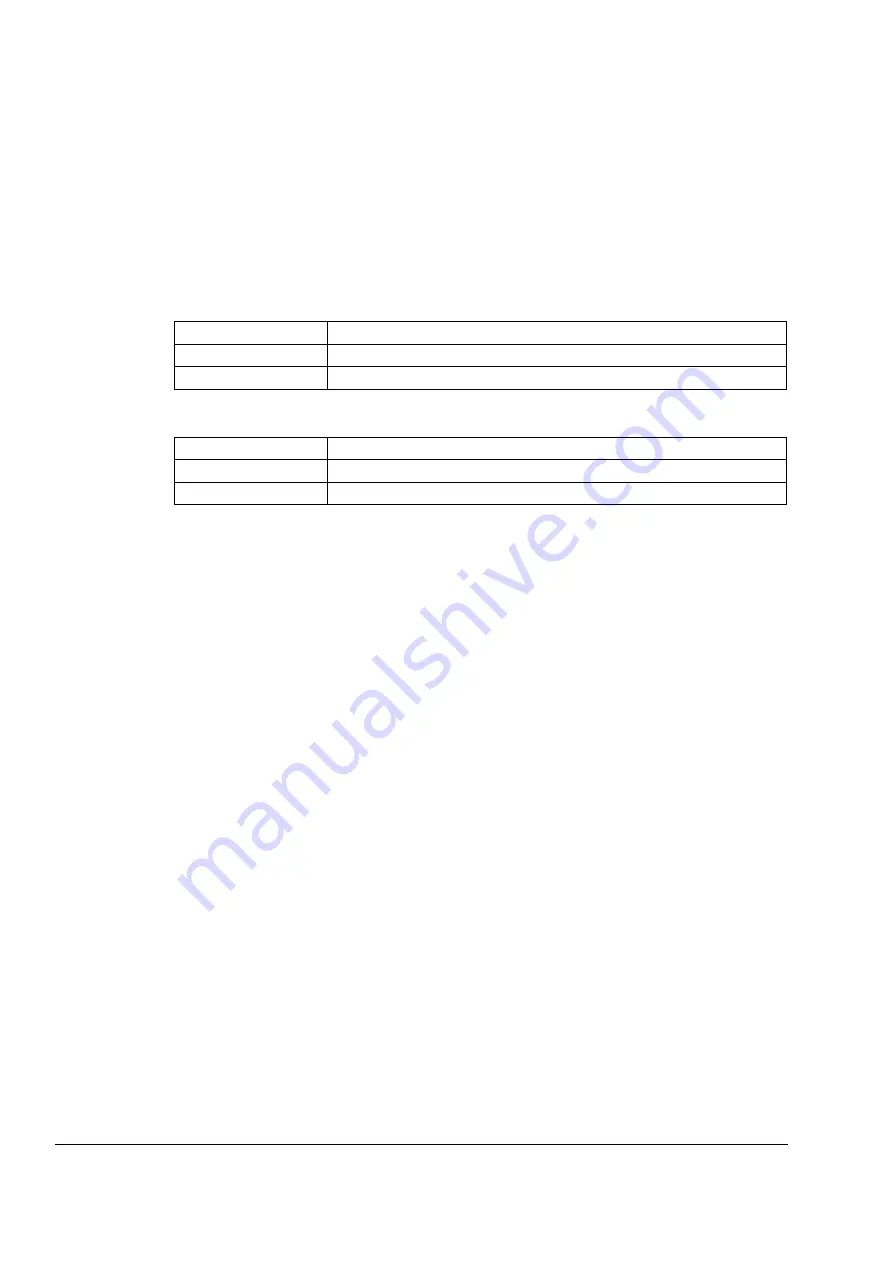
Program features
110
Service counter
The Service counter function supervises the
CRANE OPT TIME and the
BRAKE OPT COUNTS. The two signals can be monitored for the calculation of the
overall crane operation time and the brake open counts. The brake open counts can
be reset using the parameter
BRAKE CTR RESET and the crane operation
time can be reset using the parameter
RESET OPT TIME.
Settings
Diagnostics
Adaptive Programming using the function blocks
Conventionally, you can control the operation of the drive with parameters. Each
parameter has a fixed set of choices or a setting range. The parameters make the
programming easy, but the choices are limited. You cannot customise the operation
any further. The Adaptive Program (AP) makes free customising possible without the
need of a special programming tool or language:
• The program is built of standard function blocks included in the drive application
program.
• The control panel is the programming tool.
• You can document the program by drawing it on block diagram template sheets.
The maximum size of the Adaptive Program is 15 function blocks. The program may
consist of several separate functions. For more information, see the
Application
Guide for Adaptive Program
(3AFE64527274 [English]).
For examples of Adaptive Programming (AP) and creating AP files for new features,
see
Adaptive Programming examples for crane control
Note:
If you use and/or change the AP blocks used in the Crane control program
made by ABB, you are responsible for the software and the application.
DriveAP
DriveAP is a Windows-based tool for Adaptive Programming. With DriveAP it is
possible to upload the Adaptive Program from the drive and edit it with PC.
For more information, see
DriveAP User’s Manual
(3AFE64540998 [English]).
Parameter
Additional information
Reset brake operation counts
Reset crane operation time
Actual signals
Additional information
Crane operation time
Number of brake open counts
Summary of Contents for ACS 800 Series
Page 1: ...ACS800 Firmware Manual Crane Control Program N697 ...
Page 4: ......
Page 26: ...Start up and control through the I O interface 26 ...
Page 36: ...Quick start up guide 36 ...
Page 52: ...Control panel 52 ...
Page 105: ...Program features 105 Figure Control diagram for Shaft synchronisation executed in 20 ms ...
Page 128: ...Program features 128 ...
Page 150: ...Application macros control location EXT1 EXT2 150 ...
Page 228: ...Actual signals and parameters 228 ...
Page 299: ...Adaptive Programming examples for crane control 299 ...
Page 305: ...Adaptive Programming examples for crane control 305 ...
Page 318: ...Analogue Extension Module 318 ...
Page 332: ...Additional data actual signals and parameters 332 ...
Page 334: ...DriveWindow 334 ...
Page 335: ...Control block diagrams 335 Control block diagrams ...
Page 336: ...Control block diagrams 336 ...
Page 337: ...Control block diagrams 337 ...
Page 338: ...Control block diagrams 338 ...
Page 340: ...www abb com drives www abb com drivespartners Contact us 3AFE68775230 Rev E EN 2012 09 25 ...