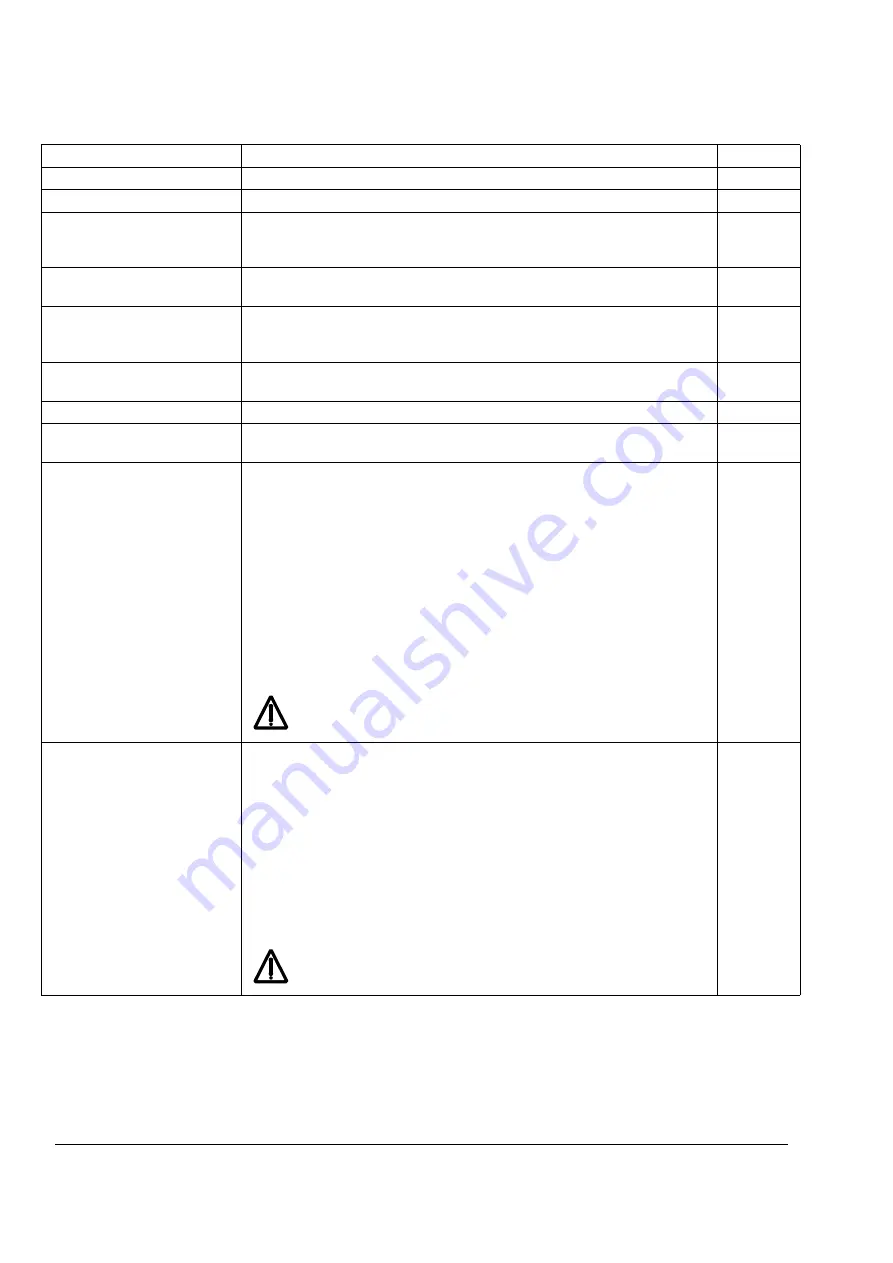
Actual signals and parameters
188
30.03
EXTERNAL FAULT
Selects an interface for an External fault signal.
NOT SEL
Inactive
1
PAR 30.24
External fault indication is given through pointer value in Par.
0: Fault trip. Motor coasts to stop.
1: No External fault.
2
30.04
MOTOR THERM
PROT
Selects how the drive reacts when the motor overtemperature is detected by
the function defined with parameter
FAULT
The drive generates a warning when the temperature exceeds the warning
level (95% of the allowed maximum value). The drive trips on a fault when the
temperature exceeds the fault level (100% of the allowed maximum value).
1
WARNING
The drive generates a warning when the temperature exceeds the warning
level (95% of the allowed maximum value).
2
NO
Inactive
3
30.05
MOT THERM P
MODE
Selects the thermal protection mode of the motor. When overtemperature is
detected, the drive reacts as defined with parameter
.
DTC
The protection is based on the calculated motor thermal model. The following
assumptions are used in the calculation:
- The motor is at the estimated temperature (value of
MOTOR
TEMP EST saved at power switch off) when the power is switched on. With the
first power switch on, the motor is at the ambient temperature (30 °C).
- The motor temperature increases if it operates in the region above the load
curve and decreases if it operates below the curve.
- The motor thermal time constant is an approximate value for a standard self-
ventilated squirrel-cage motor.
It is possible to finetune the model with parameter
.
Note:
The model cannot be used with high power motors (parameter
is
higher than 800 A).
WARNING!
The model does not protect the motor if it does not cool
properly due to dust and dirt.
1
USER MODE
The protection is based on the user-defined motor thermal model and the
following basic assumptions:
- The motor is at the estimated temperature (value of
MOTOR
TEMP EST saved at power switch off) when the power is switched on. With the
first power switch on, the motor is at the ambient temperature (30 °C).
- The motor temperature increases if it operates in the region above the motor
load curve and decreases if it operates below the curve.
The user-defined thermal model uses the motor thermal time constant
(parameter
) and the motor load curve (parameters
,
). User tuning is typically needed only if the ambient temperature differs
from the normal operating temperature specified for the motor.
WARNING!
The model does not protect the motor if it does not cool
properly due to dust and dirt.
2
Index
Name/Selection
Description
FbEq
Summary of Contents for ACS 800 Series
Page 1: ...ACS800 Firmware Manual Crane Control Program N697 ...
Page 4: ......
Page 26: ...Start up and control through the I O interface 26 ...
Page 36: ...Quick start up guide 36 ...
Page 52: ...Control panel 52 ...
Page 105: ...Program features 105 Figure Control diagram for Shaft synchronisation executed in 20 ms ...
Page 128: ...Program features 128 ...
Page 150: ...Application macros control location EXT1 EXT2 150 ...
Page 228: ...Actual signals and parameters 228 ...
Page 299: ...Adaptive Programming examples for crane control 299 ...
Page 305: ...Adaptive Programming examples for crane control 305 ...
Page 318: ...Analogue Extension Module 318 ...
Page 332: ...Additional data actual signals and parameters 332 ...
Page 334: ...DriveWindow 334 ...
Page 335: ...Control block diagrams 335 Control block diagrams ...
Page 336: ...Control block diagrams 336 ...
Page 337: ...Control block diagrams 337 ...
Page 338: ...Control block diagrams 338 ...
Page 340: ...www abb com drives www abb com drivespartners Contact us 3AFE68775230 Rev E EN 2012 09 25 ...