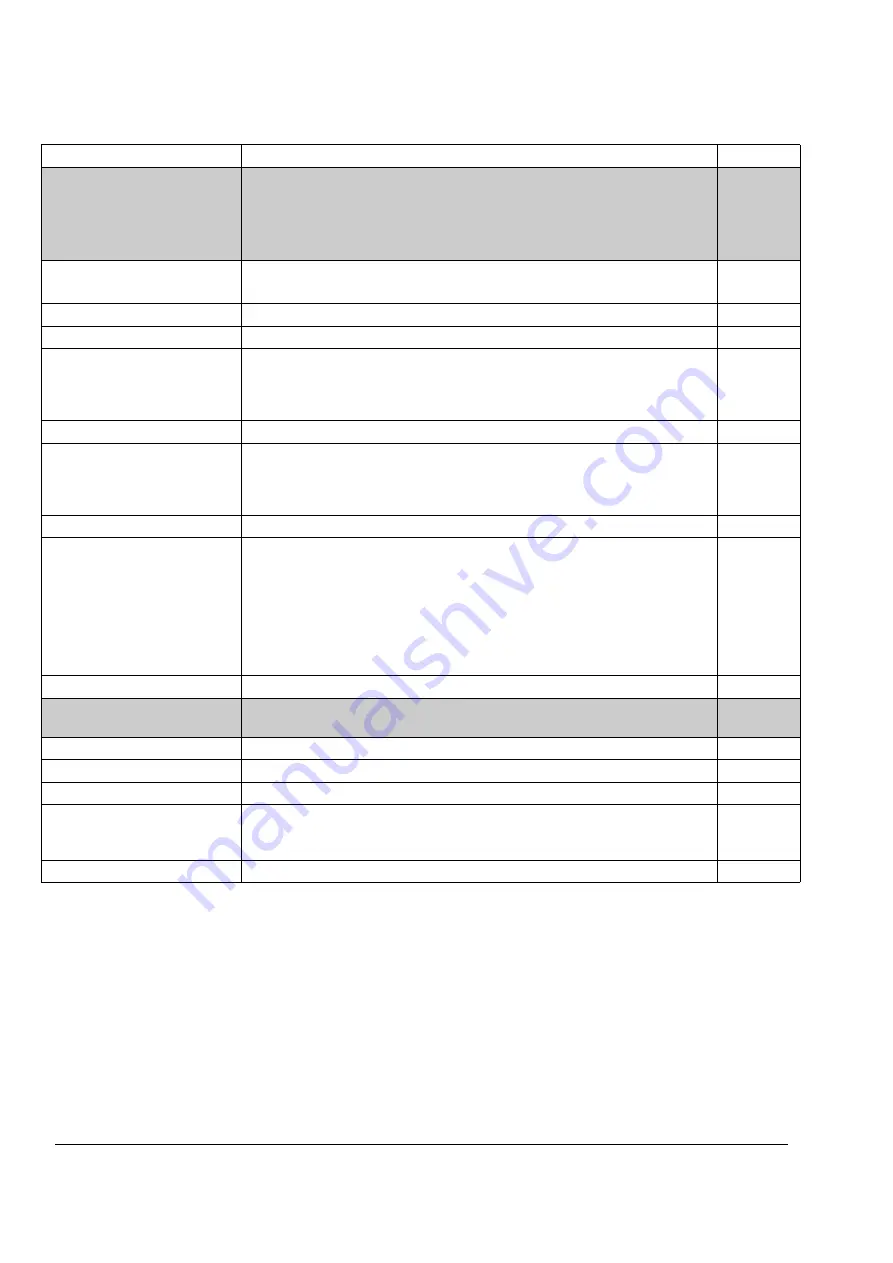
Actual signals and parameters
206
75 SPEED MATCHING
Settings for Speed matching. See section
Speed matching (internal overload
on page
Note:
When Shaft synchronisation is active, avoid using this function as the
speed correction from synchronisation block can do step speed corrections
after the speed ramp.
75.01
SPEED MATCH SEL
Selects whether Speed matching is active or not.
Note:
This function should be activated only for drives running in Speed mode.
TRUE
Active.
FALSE
Inactive.
75.02
SP DEV LEV
Defines the motor speed deviation level in percentage of maximum speed (Par.
) when the drive is running at the set point. Value is applicable in both
forward and reverse direction. A speed above this level when the drive is at set
point, means that the speed error is too high. See also parameter
.
0 … 100 %
Percent.
0 … 1000
75.03
SPD MATCH FLT TD
Defines the Speed match fault delay time when the speed error is higher than
defined in the parameter
SP DEV LEV. The drive trips on SPD MATCH
FLT if the speed error is higher than the SP DEV LEV for more than the delay
time defined.
0 … 60 s
Time. Defines the Speed match fault delay time.
0 … 600
75.04
SPD CHG PER SEC
Defines the Speed matching deviation when the drive is accelerating or
decelerating. While accelerating/decelerating, if the absolute difference
between the rate of ramped speed reference, and the rate of change of actual
speed, is greater the defined value and continues for a period defined in the
Par.
then the drive will trip on SPD MATCH FLT during acceleration/
deceleration. The rate of change of ramped speed reference is calculated
using the active acceleration/deceleration time. See section
(internal overload protection)
for more explanation.
0 … 100 %/s
Percent per second
0 … 1000
76 TORQUE PROVING
Settings for Torque proving. See section
Torque proving (Crane system check)
88.
76.01
TORQ PROV SEL
Selects whether Torque proving is active or not.
TRUE
Active.
FALSE
Inactive.
76.02
TORQ PROV FLT TD Defines the Torque proving fault delay time. The drive trips on TORQ PROVE
FLT if actual motor torque of 30% has not been attained in the time interval
defined.
0 … 100 s
Time. Defines the Torque proving fault delay time.
0 … 1000
Index
Name/Selection
Description
FbEq
Summary of Contents for ACS 800 Series
Page 1: ...ACS800 Firmware Manual Crane Control Program N697 ...
Page 4: ......
Page 26: ...Start up and control through the I O interface 26 ...
Page 36: ...Quick start up guide 36 ...
Page 52: ...Control panel 52 ...
Page 105: ...Program features 105 Figure Control diagram for Shaft synchronisation executed in 20 ms ...
Page 128: ...Program features 128 ...
Page 150: ...Application macros control location EXT1 EXT2 150 ...
Page 228: ...Actual signals and parameters 228 ...
Page 299: ...Adaptive Programming examples for crane control 299 ...
Page 305: ...Adaptive Programming examples for crane control 305 ...
Page 318: ...Analogue Extension Module 318 ...
Page 332: ...Additional data actual signals and parameters 332 ...
Page 334: ...DriveWindow 334 ...
Page 335: ...Control block diagrams 335 Control block diagrams ...
Page 336: ...Control block diagrams 336 ...
Page 337: ...Control block diagrams 337 ...
Page 338: ...Control block diagrams 338 ...
Page 340: ...www abb com drives www abb com drivespartners Contact us 3AFE68775230 Rev E EN 2012 09 25 ...