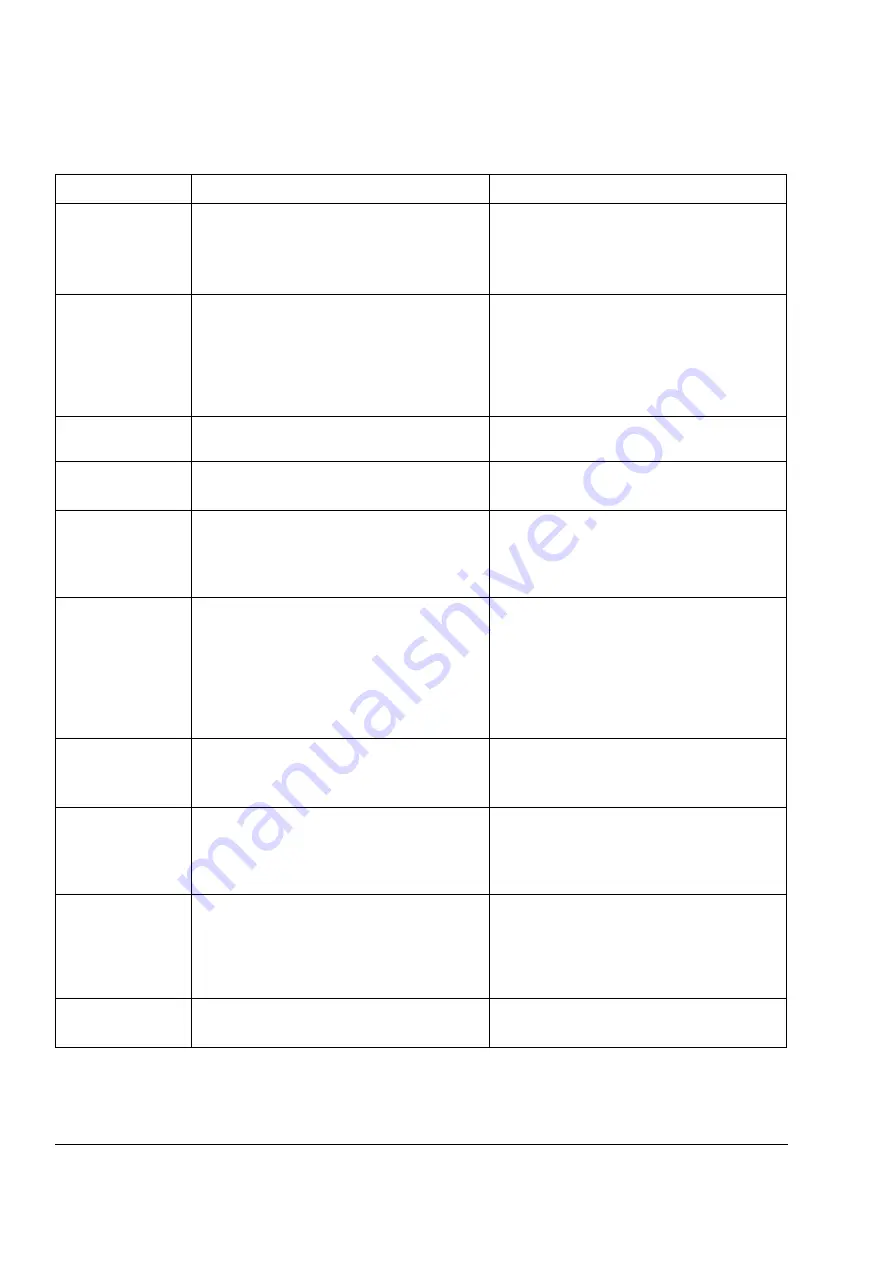
Fault tracing
280
Warning messages generated by the drive
WARNING
CAUSE
WHAT TO DO
ACS800 TEMP
(4210)
3.08 AW 1 bit 4
Drive IGBT temperature is excessive. Fault trip
limit is 100%.
Check ambient conditions.
Check air flow and fan operation.
Check heatsink fins for dust pick-up.
Check motor power against unit power.
AI < MIN FUNC
(8110)
3.09 AW 2 bit 10
(programmable
Fault Function
Analogue control signal is below minimum
allowed value due to incorrect signal level or
failure in control wiring.
Check for proper analogue control signal
levels.
Check control wiring.
Check Fault Function parameters.
AP [message]
Message generated by an EVENT block in the
Adaptive Program.
Consult the documentation or author of the
Adaptive Program.
BACKUP USED
(FFA3)
PC stored backup of drive parameters is
downloaded into use.
Wait until download is completed.
BATT FAILURE
(5581)
3.18 AW 5 bit 15
APBU branching unit memory backup battery
error caused by
- incorrect APBU switch S3 setting
- too low battery voltage.
With parallel connected inverters, enable
backup battery by setting actuator 6 of switch
S3 to ON.
Replace backup battery.
BC OVERHEAT
(7114)
3.18 AW 5 bit 3
Brake chopper overload
Stop drive. Let chopper cool down.
Check parameter settings of resistor overload
protection function (see parameter group
).
Check that braking cycle meets allowed limits.
Check that drive supply AC voltage is not
excessive.
BRAKE ACKN
(FF74)
3.16 AW 4 bit 3
Unexpected state of brake acknowledge signal
See
parameter group
Check connection of brake acknowledgement
signal.
BRK LONG TIME
(FFFC)
3.32 Crane SW bit 9
Brake acknowledge active after brake close
delay has elapsed. Drive active with zero
speed reference.
See
parameter group
Check connection of brake acknowledgement
signal.
Check mechanical brake.
BR OVERHEAT
(7112)
3.18 AW 5 bit 2
Brake resistor overload
Stop drive. Let resistor cool down.
Check parameter settings of resistor overload
protection function (see parameter group
).
Check that braking cycle meets allowed limits.
CALIBRA DONE
(FF37)
Calibration of output current transformers is
completed.
Continue normal operation.
Summary of Contents for ACS 800 Series
Page 1: ...ACS800 Firmware Manual Crane Control Program N697 ...
Page 4: ......
Page 26: ...Start up and control through the I O interface 26 ...
Page 36: ...Quick start up guide 36 ...
Page 52: ...Control panel 52 ...
Page 105: ...Program features 105 Figure Control diagram for Shaft synchronisation executed in 20 ms ...
Page 128: ...Program features 128 ...
Page 150: ...Application macros control location EXT1 EXT2 150 ...
Page 228: ...Actual signals and parameters 228 ...
Page 299: ...Adaptive Programming examples for crane control 299 ...
Page 305: ...Adaptive Programming examples for crane control 305 ...
Page 318: ...Analogue Extension Module 318 ...
Page 332: ...Additional data actual signals and parameters 332 ...
Page 334: ...DriveWindow 334 ...
Page 335: ...Control block diagrams 335 Control block diagrams ...
Page 336: ...Control block diagrams 336 ...
Page 337: ...Control block diagrams 337 ...
Page 338: ...Control block diagrams 338 ...
Page 340: ...www abb com drives www abb com drivespartners Contact us 3AFE68775230 Rev E EN 2012 09 25 ...