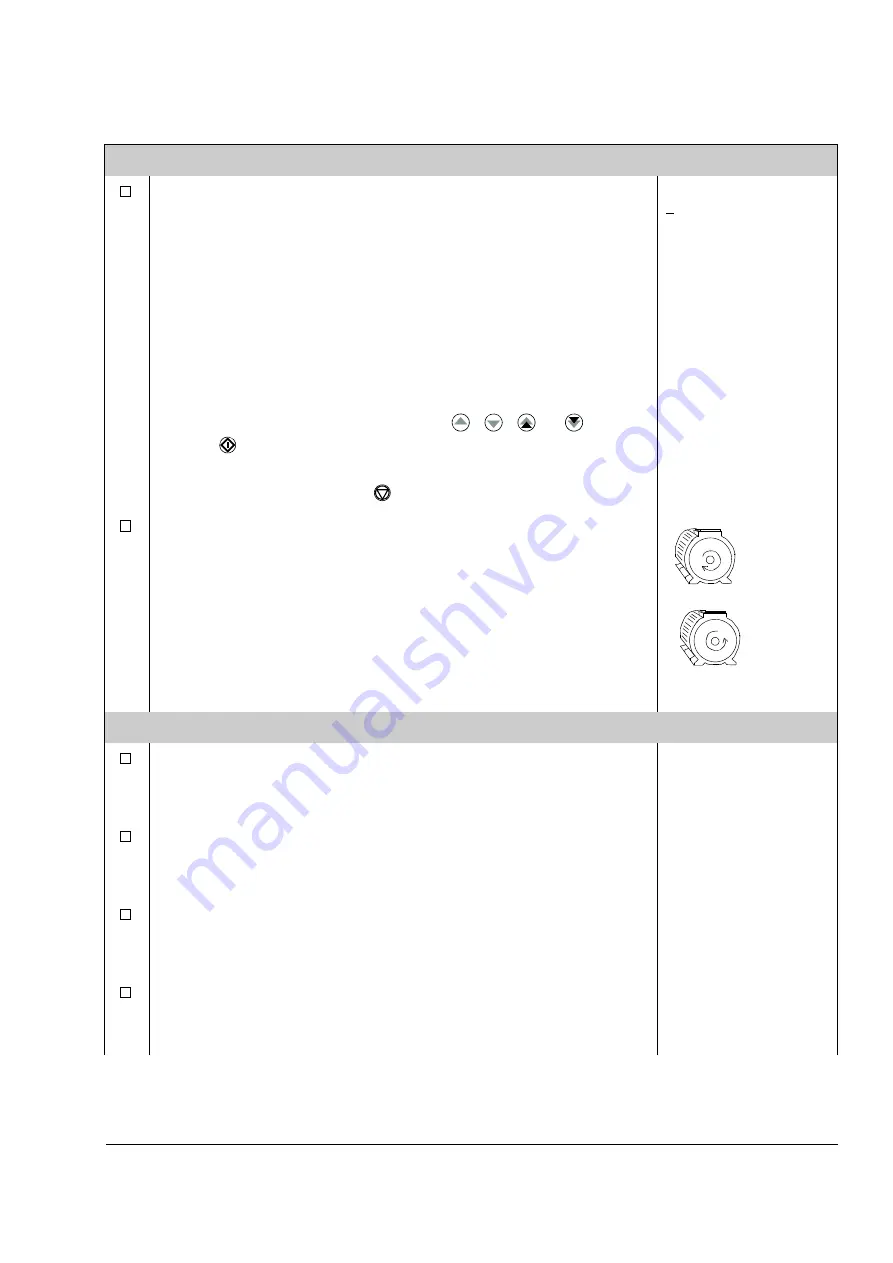
Start-up and control through the I/O interface
21
DIRECTION OF ROTATION OF THE MOTOR
Check the direction of rotation of the motor.
Note
:
In the crane application,
- the forward direction (positive) must be the UP direction.
- the reverse direction (negative) must be the DOWN direction.
This is important because the torque memory uses the positive
direction in starts.
- Press
ACT
to get the status row visible.
- Increase the speed reference from zero to a small value by
pressing
REF
and then the arrow keys (
,
,
or
).
- Press
to start the motor.
- Check that the motor is running in the desired direction.
- Stop the motor by pressing
.
1 L->[xxx] rpm I
FREQ xxx Hz
CURRENT xx A
POWER xx %
To change the direction of rotation of the motor:
- Disconnect mains power from the drive, and wait 5 minutes for the
intermediate circuit capacitors to discharge. Measure the voltage
between each input terminal (U1, V1 and W1) and earth with a
multimeter to ensure that the frequency converter is discharged.
- Exchange the position of two motor cable phase conductors at the
motor terminals or at the motor connection box.
- Verify your work by applying mains power and repeating the check
as described above.
SPEED LIMITS AND ACCELERATION/DECELERATION TIMES
Set the minimum speed. This value will be used as the speed limit
in the reverse direction.
1 L-> 0.0 rpm O
20 LIMITS
01 MINIMUM SPEED
[ ]
Set the maximum speed. This value will be used as the speed limit
in the forward direction.
1 L-> 0.0 rpm O
20 LIMITS
02 MAXIMUM SPEED
[ ]
Set the acceleration time 1.
1 L-> 0.0 rpm O
22 ACCEL/DECEL
02 ACCEL TIME 1
[ ]
Set the acceleration time 2.
1 L-> 0.0 rpm O
22 ACCEL/DECEL
04 ACCEL TIME 2
[ ]
forward
direction
reverse
direction
Summary of Contents for ACS 800 Series
Page 1: ...ACS800 Firmware Manual Crane Control Program N697 ...
Page 4: ......
Page 26: ...Start up and control through the I O interface 26 ...
Page 36: ...Quick start up guide 36 ...
Page 52: ...Control panel 52 ...
Page 105: ...Program features 105 Figure Control diagram for Shaft synchronisation executed in 20 ms ...
Page 128: ...Program features 128 ...
Page 150: ...Application macros control location EXT1 EXT2 150 ...
Page 228: ...Actual signals and parameters 228 ...
Page 299: ...Adaptive Programming examples for crane control 299 ...
Page 305: ...Adaptive Programming examples for crane control 305 ...
Page 318: ...Analogue Extension Module 318 ...
Page 332: ...Additional data actual signals and parameters 332 ...
Page 334: ...DriveWindow 334 ...
Page 335: ...Control block diagrams 335 Control block diagrams ...
Page 336: ...Control block diagrams 336 ...
Page 337: ...Control block diagrams 337 ...
Page 338: ...Control block diagrams 338 ...
Page 340: ...www abb com drives www abb com drivespartners Contact us 3AFE68775230 Rev E EN 2012 09 25 ...