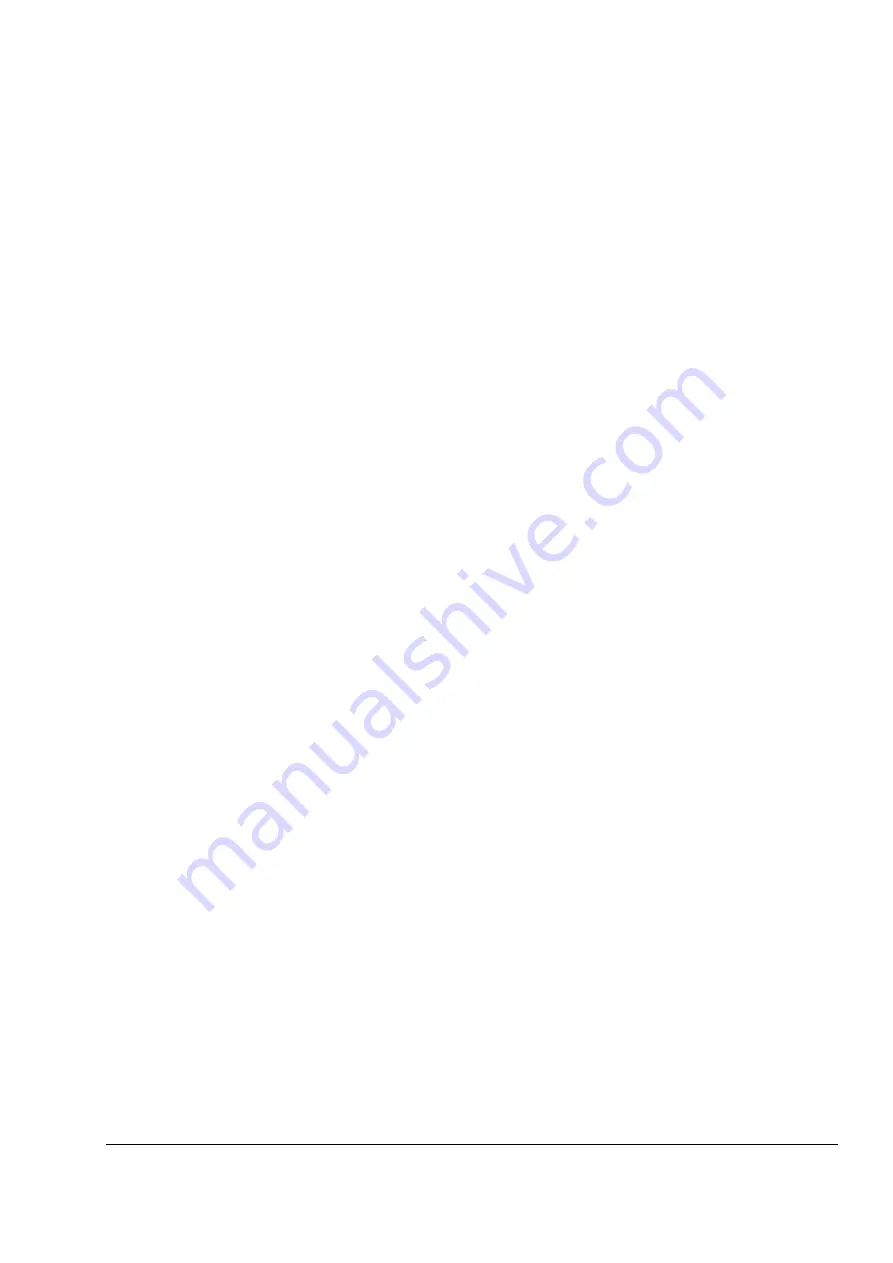
Program features
123
Load speed control
This function is used for running the motor above the base speed if the motor is able
to provide a sufficient torque with respect to the load condition. The function allows
you to run the motor at a higher speed above the base speed according to the motor
current at the base speed with the load. It is assumed that the load at which the
motor crosses the base speed remains constant until the motor stops, and then a
new Start command is given.
The user defines a set of current (A) and speed (rpm) parameters, which specify the
curve to be used to calculate the motor speed limit according to the current at the
base speed Par.
. The motor current at the base speed Par.
is checked
for a predefined time period of Par.
HOLD RAMP, so that the motor current
would have settled down to a less oscillating value.
Parameter
LOAD SPD CTRL SEL defines the activation command for the
Load speed control function. Parameter
HOLD RAMP defines the time period
after which the motor has crossed the base speed to check for the motor current.
This motor current after this time period delay is regarded by the function as the
base speed current for the particular load used. Parameters
base speed versus current graph in both the forward and reverse direction and are
further used to limit the speed according to the base speed current.
If parameters
are not configured properly in the correct sequence, the
speed is always limited to Par.
BASE SPEED, and the error bit (signal
bit 10) is set to 1. Parameters
…
are to be configured as follows:
• The current values for the forward direction to be entered in parameters
,
and
have to be entered in the increasing order.
• The speed limit values for the forward direction to be entered in parameters
have to be entered in the decreasing order.
• The current values for the reverse direction to be entered in parameters
,
and
have to be entered in the increasing order.
• The speed limit values for the reverse direction to be entered in parameters
have to be entered in the decreasing order.
Summary of Contents for ACS 800 Series
Page 1: ...ACS800 Firmware Manual Crane Control Program N697 ...
Page 4: ......
Page 26: ...Start up and control through the I O interface 26 ...
Page 36: ...Quick start up guide 36 ...
Page 52: ...Control panel 52 ...
Page 105: ...Program features 105 Figure Control diagram for Shaft synchronisation executed in 20 ms ...
Page 128: ...Program features 128 ...
Page 150: ...Application macros control location EXT1 EXT2 150 ...
Page 228: ...Actual signals and parameters 228 ...
Page 299: ...Adaptive Programming examples for crane control 299 ...
Page 305: ...Adaptive Programming examples for crane control 305 ...
Page 318: ...Analogue Extension Module 318 ...
Page 332: ...Additional data actual signals and parameters 332 ...
Page 334: ...DriveWindow 334 ...
Page 335: ...Control block diagrams 335 Control block diagrams ...
Page 336: ...Control block diagrams 336 ...
Page 337: ...Control block diagrams 337 ...
Page 338: ...Control block diagrams 338 ...
Page 340: ...www abb com drives www abb com drivespartners Contact us 3AFE68775230 Rev E EN 2012 09 25 ...