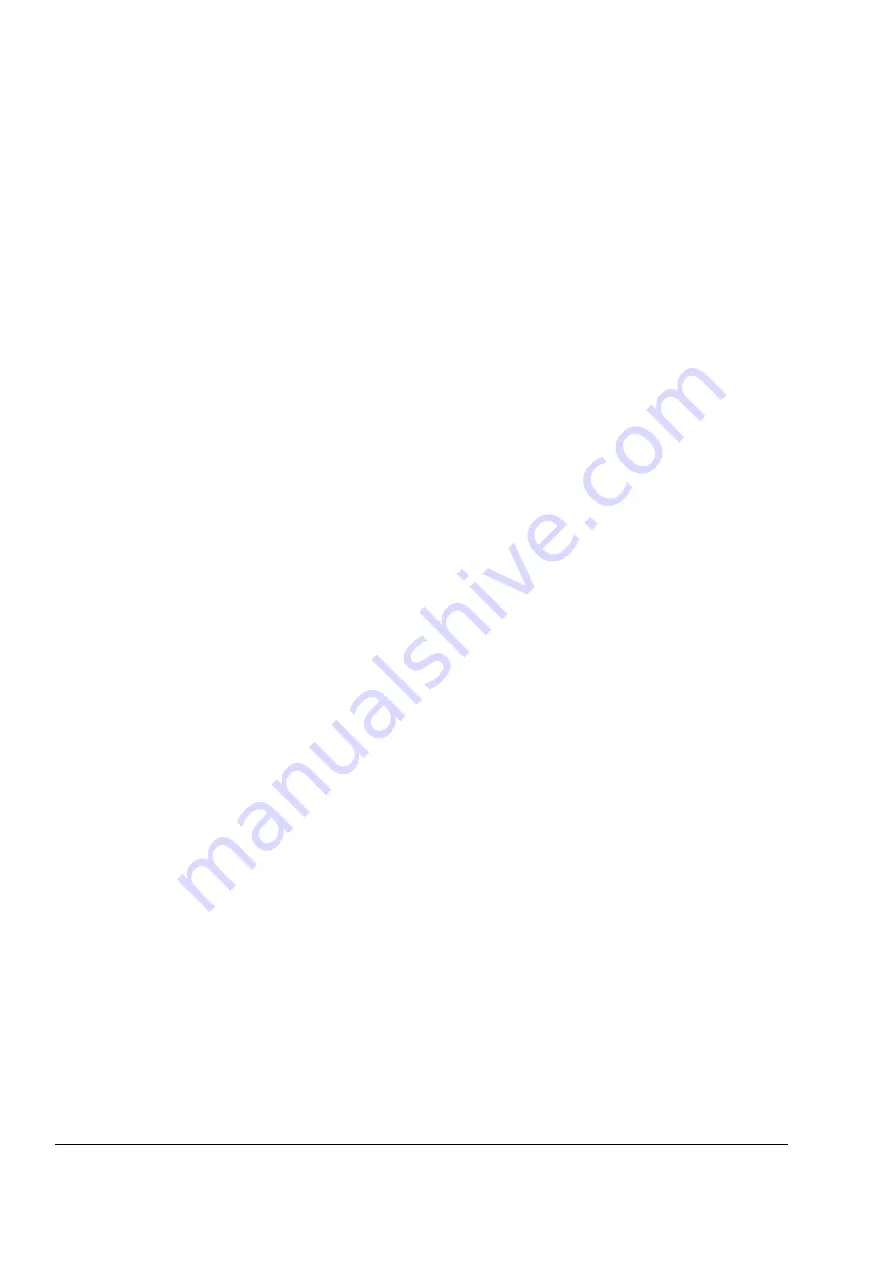
Fieldbus control
242
The Control Word and the Status Word
The Control Word (CW) is the principal means of controlling the drive from a fieldbus
system. It is effective when the active control location (EXT1 or EXT2, see
parameters 10.01 and 10.02) is set to COMM.CW, or if Par. 10.07 is set to 1 (with
Generic Drive communication profile only).
The Control Word is sent by the fieldbus controller to the drive. The drive switches
between its states according to the bit-coded instructions of the Control Word.
The Status Word (SW) is a word containing status information, sent by the drive to
the fieldbus controller.
on page
for information on the composition
of the Control Word and the Status Word.
References
References (REF) are 16-bit signed integers. A negative reference (indicating
reversed direction of rotation) is formed by calculating the two’s complement from
the corresponding positive reference value.
Fieldbus reference selection
Fieldbus reference (called COMM. REF in signal selection contexts) is selected by
setting a Reference selection parameter – 11.03 or 11.06 – to COMM. REFx or FAST
COMM. (With Generic Drive communication profile, fieldbus reference is also
selected when Par. 10.08 is set to 1.)
COMM. REF1 (in 11.03) or COMM. REF2 (in 11.06)
The fieldbus reference is forwarded.
FAST COMM
The fieldbus reference is forwarded. The reference is read every 2 milliseconds if
either of the following conditions is met:
• Control location is
EXT1
, Par. 99.04 MOTOR CTRL MODE is
DTC
• Control location is
EXT2
, Par. 99.04 MOTOR CTRL MODE is
DTC
and a
torque
reference
is used.
In any other event, the fieldbus reference is read every 6 milliseconds.
Reference handling
The control of rotation direction is configured for each control location (EXT1 and
EXT2) using the parameters in group 10. Fieldbus references are bipolar, that is they
can be negative or positive. The following diagrams illustrate how group 10
parameters and the sign of the fieldbus reference interact to produce the reference
REF1/REF2.
Notes:
• With the ABB Drives communication profile, 100% reference is defined with
parameters
(REF1) and
Summary of Contents for ACS 800 Series
Page 1: ...ACS800 Firmware Manual Crane Control Program N697 ...
Page 4: ......
Page 26: ...Start up and control through the I O interface 26 ...
Page 36: ...Quick start up guide 36 ...
Page 52: ...Control panel 52 ...
Page 105: ...Program features 105 Figure Control diagram for Shaft synchronisation executed in 20 ms ...
Page 128: ...Program features 128 ...
Page 150: ...Application macros control location EXT1 EXT2 150 ...
Page 228: ...Actual signals and parameters 228 ...
Page 299: ...Adaptive Programming examples for crane control 299 ...
Page 305: ...Adaptive Programming examples for crane control 305 ...
Page 318: ...Analogue Extension Module 318 ...
Page 332: ...Additional data actual signals and parameters 332 ...
Page 334: ...DriveWindow 334 ...
Page 335: ...Control block diagrams 335 Control block diagrams ...
Page 336: ...Control block diagrams 336 ...
Page 337: ...Control block diagrams 337 ...
Page 338: ...Control block diagrams 338 ...
Page 340: ...www abb com drives www abb com drivespartners Contact us 3AFE68775230 Rev E EN 2012 09 25 ...