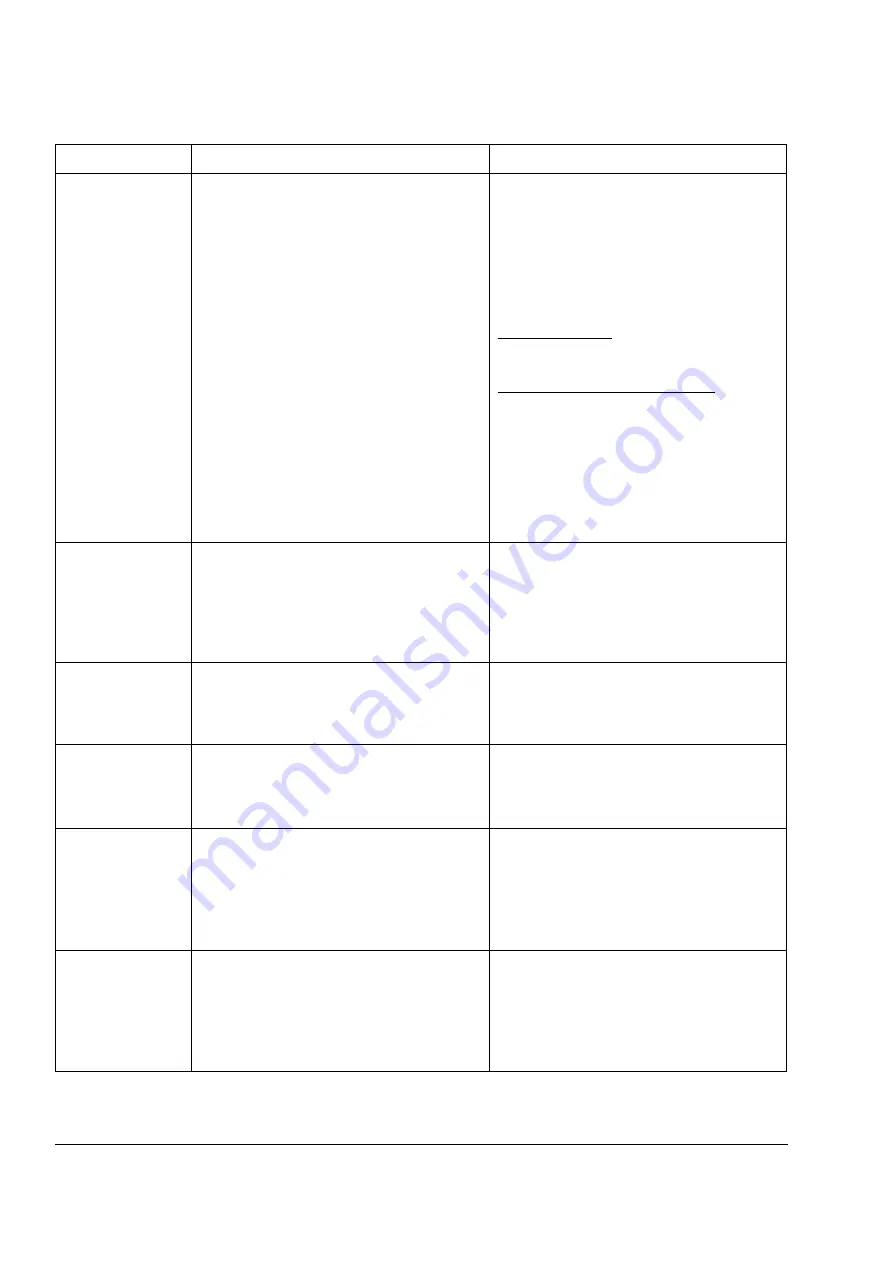
Fault tracing
292
INV OVERTEMP
(4290)
3.17 FW 5 bit 13
Converter module temperature is excessive.
Check ambient temperature. If it exceeds
40°C, ensure that load current does not
exceed derated load capacity of drive. See
appropriate hardware manual.
Check that ambient temperature setting is
correct (parameter
).
Check converter module cooling air flow and
fan operation.
Cabinet installation: Check cabinet air inlet
filters. Change when necessary. See
appropriate hardware manual.
Modules installed in cabinet by user: Check
that cooling air circulation in cabinet has been
prevented with air baffles. See module
installation instructions.
Check inside of cabinet and heatsink of
converter module for dust pick-up. Clean when
necessary.
Reset and restart after problem is solved and
let converter module cool down.
I/O COMM ERR
(7000)
3.06 FW 2 bit 6
Communication error on control board,
channel CH1
Electromagnetic interference
Check connections of fibre optic cables on
channel CH1.
Check all I/O modules (if present) connected to
channel CH1.
Check for proper earthing of equipment. Check
for highly emissive components nearby.
LINE CONV
(FF51)
Fault on line side converter
Shift panel from motor side converter control
board to line side converter control board.
See line side converter manual for fault
description.
MOTOROVER
SPD
(FFF0)
3.33 CRANE FW bit 0
The speed exceeds the MOT OVERSPEED
LEV (Par.
)
Check Torque and Current limit settings
Check motor and motor cables
Check pulse encoder connections if used
MOTOR PHASE
(FF56)
3.06 FW 2 bit 15
(programmable
Fault Function
One of motor phases is lost due to fault in
motor, motor cable, thermal relay (if used) or
internal fault.
Check motor and motor cable.
Check thermal relay (if used).
Check Fault Function parameters. Disable this
protection.
MOTOR TEMP
(4310)
3.05 FW 1 bit 6
(programmable
Fault Function
…
Motor temperature is too high (or appears to be
too high) due to excessive load, insufficient
motor power, inadequate cooling or incorrect
start-up data.
Check motor ratings and load.
Check start-up data.
Check Fault Function parameters.
FAULT
CAUSE
WHAT TO DO
Summary of Contents for ACS 800 Series
Page 1: ...ACS800 Firmware Manual Crane Control Program N697 ...
Page 4: ......
Page 26: ...Start up and control through the I O interface 26 ...
Page 36: ...Quick start up guide 36 ...
Page 52: ...Control panel 52 ...
Page 105: ...Program features 105 Figure Control diagram for Shaft synchronisation executed in 20 ms ...
Page 128: ...Program features 128 ...
Page 150: ...Application macros control location EXT1 EXT2 150 ...
Page 228: ...Actual signals and parameters 228 ...
Page 299: ...Adaptive Programming examples for crane control 299 ...
Page 305: ...Adaptive Programming examples for crane control 305 ...
Page 318: ...Analogue Extension Module 318 ...
Page 332: ...Additional data actual signals and parameters 332 ...
Page 334: ...DriveWindow 334 ...
Page 335: ...Control block diagrams 335 Control block diagrams ...
Page 336: ...Control block diagrams 336 ...
Page 337: ...Control block diagrams 337 ...
Page 338: ...Control block diagrams 338 ...
Page 340: ...www abb com drives www abb com drivespartners Contact us 3AFE68775230 Rev E EN 2012 09 25 ...