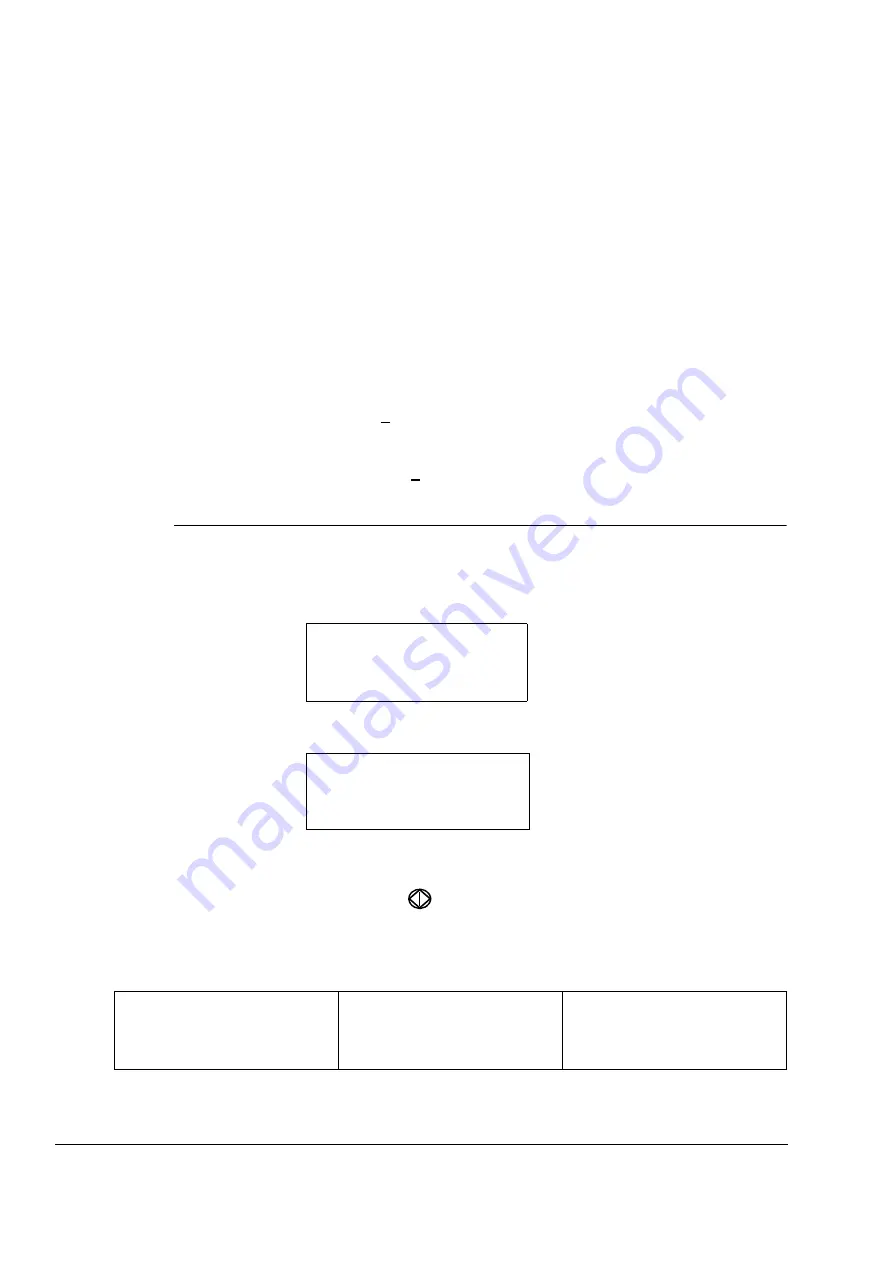
Start-up and control through the I/O interface
24
How to perform the ID run
The drive performs the ID Magnetisation automatically at the first start. In most
applications there is no need to perform a separate ID run. The ID run (STANDARD)
should be selected if:
• The operation point is near zero speed, and/or
• Operation at torque range above the motor nominal torque within a wide speed
range and without any measured speed feedback is required.
ID run procedure
Note:
If parameter values (Group 10 … 98) are changed before the ID run, check
that the new settings meet the following conditions:
• 20.01 MINIMUM SPEED < 0 rpm
• 20.02 MAXIMUM SPEED > 80% of motor rated speed
• 20.03 MAXIMUM CURRENT > 100% ·
I
hd
• 20.04 TORQ MAX LIM1 > 50%
• Ensure that the panel is in the local control mode (L displayed on the status row).
Press the
LOC/REM
key to switch between modes.
• Change the ID run selection to STANDARD.
• Press
ENTER
to verify the selection. The following message is displayed:
• If brake control is active, the brake is opened when STANDARD ID run is
selected.
• To start the ID run, press the
key. The Run Enable signal must be active (see
parameter
RUN ENABLE).
Warning when the ID run is
started
Warning during the ID run
Warning after a successfully
completed ID Run
1 L -> 1242.0 rpm I
ACS800
**WARNING**
MOTOR STARTS
1 L -> 1242.0 rpm I
ACS800
**WARNING**
ID RUN
1 L -> 1242.0 rpm I
ACS800
**WARNING**
ID DONE
99 START-UP DATA
10 MOTOR ID RUN
[STANDARD]
1 L ->1242.0 rpm O
1 L ->1242.0 rpm O
ACS800
**WARNING**
ID RUN SEL
Summary of Contents for ACS 800 Series
Page 1: ...ACS800 Firmware Manual Crane Control Program N697 ...
Page 4: ......
Page 26: ...Start up and control through the I O interface 26 ...
Page 36: ...Quick start up guide 36 ...
Page 52: ...Control panel 52 ...
Page 105: ...Program features 105 Figure Control diagram for Shaft synchronisation executed in 20 ms ...
Page 128: ...Program features 128 ...
Page 150: ...Application macros control location EXT1 EXT2 150 ...
Page 228: ...Actual signals and parameters 228 ...
Page 299: ...Adaptive Programming examples for crane control 299 ...
Page 305: ...Adaptive Programming examples for crane control 305 ...
Page 318: ...Analogue Extension Module 318 ...
Page 332: ...Additional data actual signals and parameters 332 ...
Page 334: ...DriveWindow 334 ...
Page 335: ...Control block diagrams 335 Control block diagrams ...
Page 336: ...Control block diagrams 336 ...
Page 337: ...Control block diagrams 337 ...
Page 338: ...Control block diagrams 338 ...
Page 340: ...www abb com drives www abb com drivespartners Contact us 3AFE68775230 Rev E EN 2012 09 25 ...