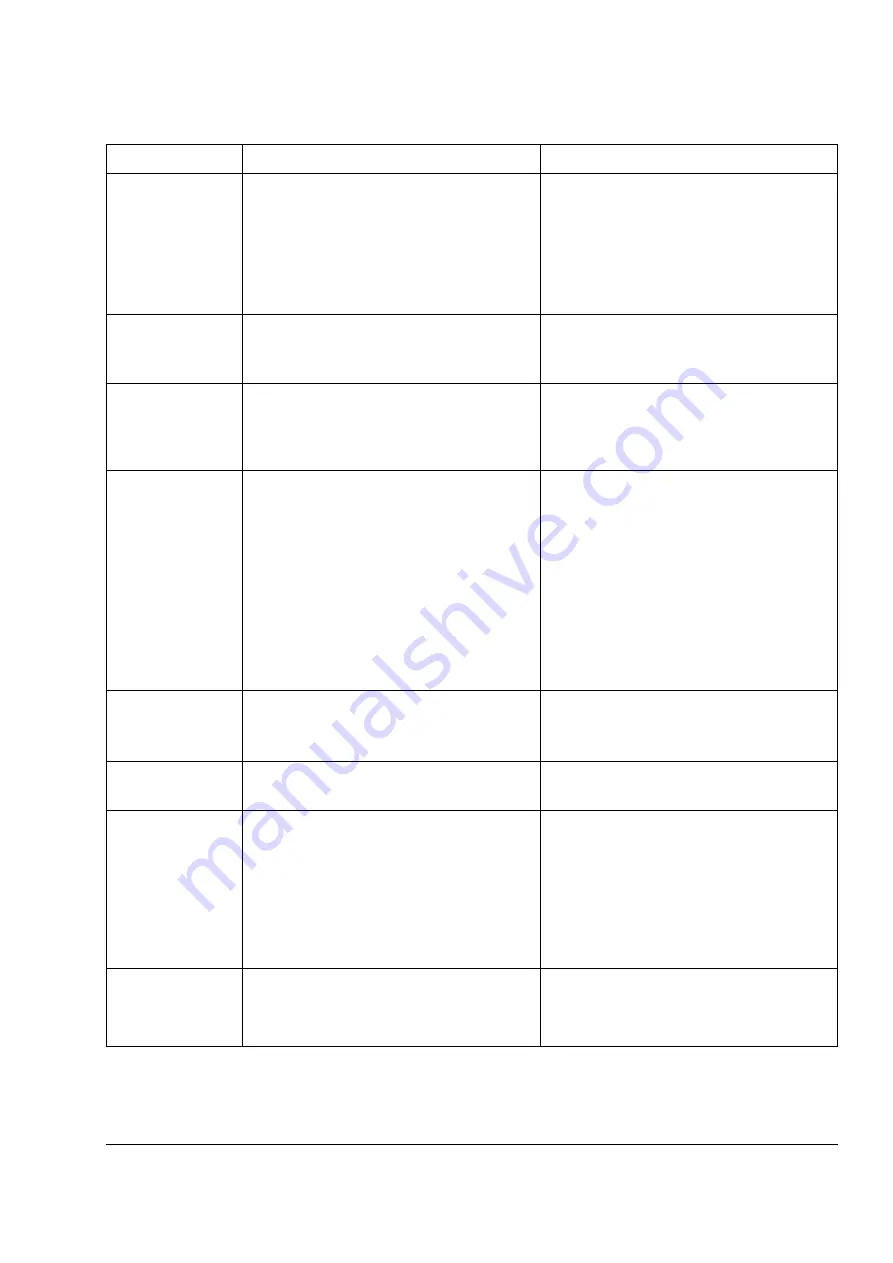
Fault tracing
289
BR OVERHEAT
(7112)
3.17 FW 5 bit 3
Brake resistor overload
Let resistor cool down.
Check parameter settings of resistor overload
protection function (see parameter group
).
Check that braking cycle meets allowed limits.
Check that drive supply AC voltage is not
excessive.
BR WIRING
(7111)
3.17 FW 5 bit 1
Wrong connection of brake resistor
Check resistor connection.
Ensure brake resistor is not damaged.
CHOKE OTEMP
(FF82)
Excessive temperature of drive output filter.
Supervision is in use in step-up drives.
Let drive cool down.
Check ambient temperature.
Check filter fan rotates in correct direction and
air flows freely.
COMM MODULE
(7510)
3.06 FW 2 bit 12
(programmable
Fault Function
)
Cyclical communication between drive and
master is lost.
Check status of fieldbus communication. See
chapter
, or appropriate
fieldbus adapter manual.
Check parameter settings:
- group
(for fieldbus
(for
Standard Modbus Link).
Check Fault Function parameters.
Check cable connections.
Check if master can communicate.
CTRL B TEMP
(4110)
3.06 FW 2 bit 7
Control board temperature is above 88°C.
Check ambient conditions.
Check air flow.
Check main and additional cooling fans.
CURR MEAS
(2211)
Current transformer failure in output current
measurement circuit
Check current transformer connections to Main
Circuit Interface Board, INT.
CUR UNBAL xx
(2330)
3.05 FW 1 bit 4 and
4.01
(programmable
Fault Function
Drive has detected excessive output current
unbalance in inverter unit of several parallel
connected inverter modules. This can be
caused by external fault (earth fault, motor,
motor cabling, etc.) or internal fault (damaged
inverter component). xx (1...12) refers to
inverter module number.
Check there are no power factor correction
capacitors or surge absorbers in motor cable.
Check that there is no earth fault in motor or
motor cables:
- measure insulation resistances of motor and
motor cable.
If no earth fault can be detected, contact your
local ABB representative.
DC HIGH RUSH
(FF80)
Drive supply voltage is excessive. When
supply voltage is over 124% of unit voltage
rating (415, 500 or 690 V), motor speed rushes
to trip level (40% of nominal speed).
Check supply voltage level, drive rated voltage
and allowed voltage range of drive.
FAULT
CAUSE
WHAT TO DO
Summary of Contents for ACS 800 Series
Page 1: ...ACS800 Firmware Manual Crane Control Program N697 ...
Page 4: ......
Page 26: ...Start up and control through the I O interface 26 ...
Page 36: ...Quick start up guide 36 ...
Page 52: ...Control panel 52 ...
Page 105: ...Program features 105 Figure Control diagram for Shaft synchronisation executed in 20 ms ...
Page 128: ...Program features 128 ...
Page 150: ...Application macros control location EXT1 EXT2 150 ...
Page 228: ...Actual signals and parameters 228 ...
Page 299: ...Adaptive Programming examples for crane control 299 ...
Page 305: ...Adaptive Programming examples for crane control 305 ...
Page 318: ...Analogue Extension Module 318 ...
Page 332: ...Additional data actual signals and parameters 332 ...
Page 334: ...DriveWindow 334 ...
Page 335: ...Control block diagrams 335 Control block diagrams ...
Page 336: ...Control block diagrams 336 ...
Page 337: ...Control block diagrams 337 ...
Page 338: ...Control block diagrams 338 ...
Page 340: ...www abb com drives www abb com drivespartners Contact us 3AFE68775230 Rev E EN 2012 09 25 ...