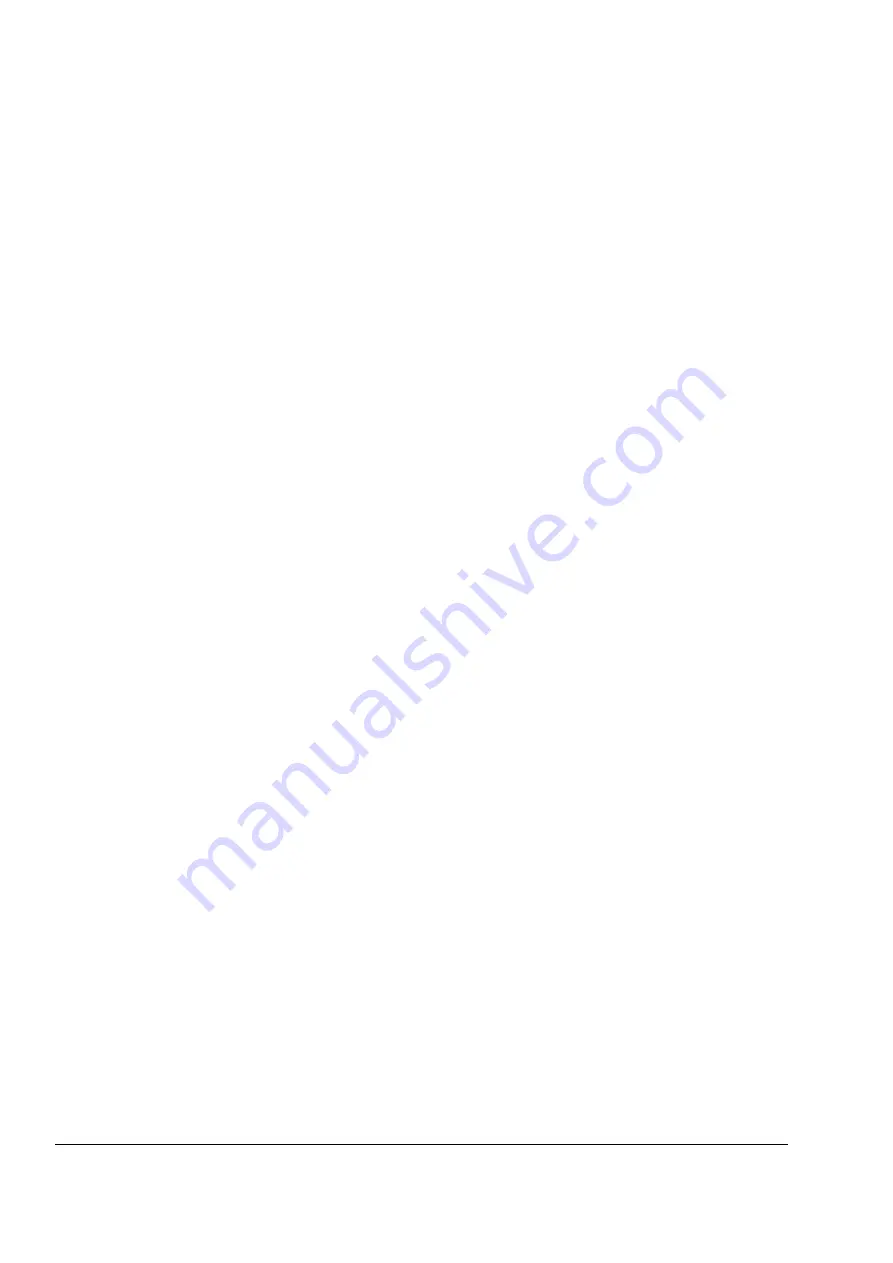
Program features
94
Master/Follower use of several drives (Only in EXT2 Control)
In a Master/Follower application, the system is run by several drives, the motor
shafts of which are coupled to each other. The Master and Follower drives
communicate via a fibre optic link. For the Master/Follower configuration to work, the
drive has to be in EXT2 control. If the Master/Follower configuration is used in EXT1,
the drive works as a stand-alone drive.
The Master drive communicates with the Follower drive through channel 2. The
channel 2 addresses are set internally in the Follower drives. The fault, torque prove
OK, safety control bits and the drive ready bits of the Follower drives are used for the
interlock in the Master drive. These interlocks work only when the drive is in EXT2
control. In EXT1 control none of these interlocks are checked and the drive works
like a stand-alone drive. The Follower drive uses the data set 44 for transmitting the
interlock status word. The Master also sends the interlock bits to the slave using data
set 43. The Master monitors if any of the Follower drives goes into the fault or limit
state and the FLWRx LIM/FLT message (where x is the Follower drive number) is
displayed in such condition. The detailed description of the fault or limit will be
available in the Follower drive.
Note
: Even though the Master/Follower interlock functions are checked only in EXT2
control, the Master/Follower communication link should be active in both EXT1 and
EXT2 control. Otherwise the drives will trip on Communication fault.
The user defines the number of Follower drives in the Master drive. One Master
drive can have a maximum of four Follower drives. Note that you must configure the
Follower drives in a sequential order. In other words, if the configuration includes
one Follower drive, it is configured as Follower 1, not as Follower 2, Follower 3, or
Follower 4. Similarly, if the configuration includes two Follower drives, the correct
configuration is Follower 1 and Follower 2, not Follower 2 and Follower 3, or any
other combination. A follower drive is configured as Follower 4 only when the
configuration includes four Follower drives.
Summary of Contents for ACS 800 Series
Page 1: ...ACS800 Firmware Manual Crane Control Program N697 ...
Page 4: ......
Page 26: ...Start up and control through the I O interface 26 ...
Page 36: ...Quick start up guide 36 ...
Page 52: ...Control panel 52 ...
Page 105: ...Program features 105 Figure Control diagram for Shaft synchronisation executed in 20 ms ...
Page 128: ...Program features 128 ...
Page 150: ...Application macros control location EXT1 EXT2 150 ...
Page 228: ...Actual signals and parameters 228 ...
Page 299: ...Adaptive Programming examples for crane control 299 ...
Page 305: ...Adaptive Programming examples for crane control 305 ...
Page 318: ...Analogue Extension Module 318 ...
Page 332: ...Additional data actual signals and parameters 332 ...
Page 334: ...DriveWindow 334 ...
Page 335: ...Control block diagrams 335 Control block diagrams ...
Page 336: ...Control block diagrams 336 ...
Page 337: ...Control block diagrams 337 ...
Page 338: ...Control block diagrams 338 ...
Page 340: ...www abb com drives www abb com drivespartners Contact us 3AFE68775230 Rev E EN 2012 09 25 ...