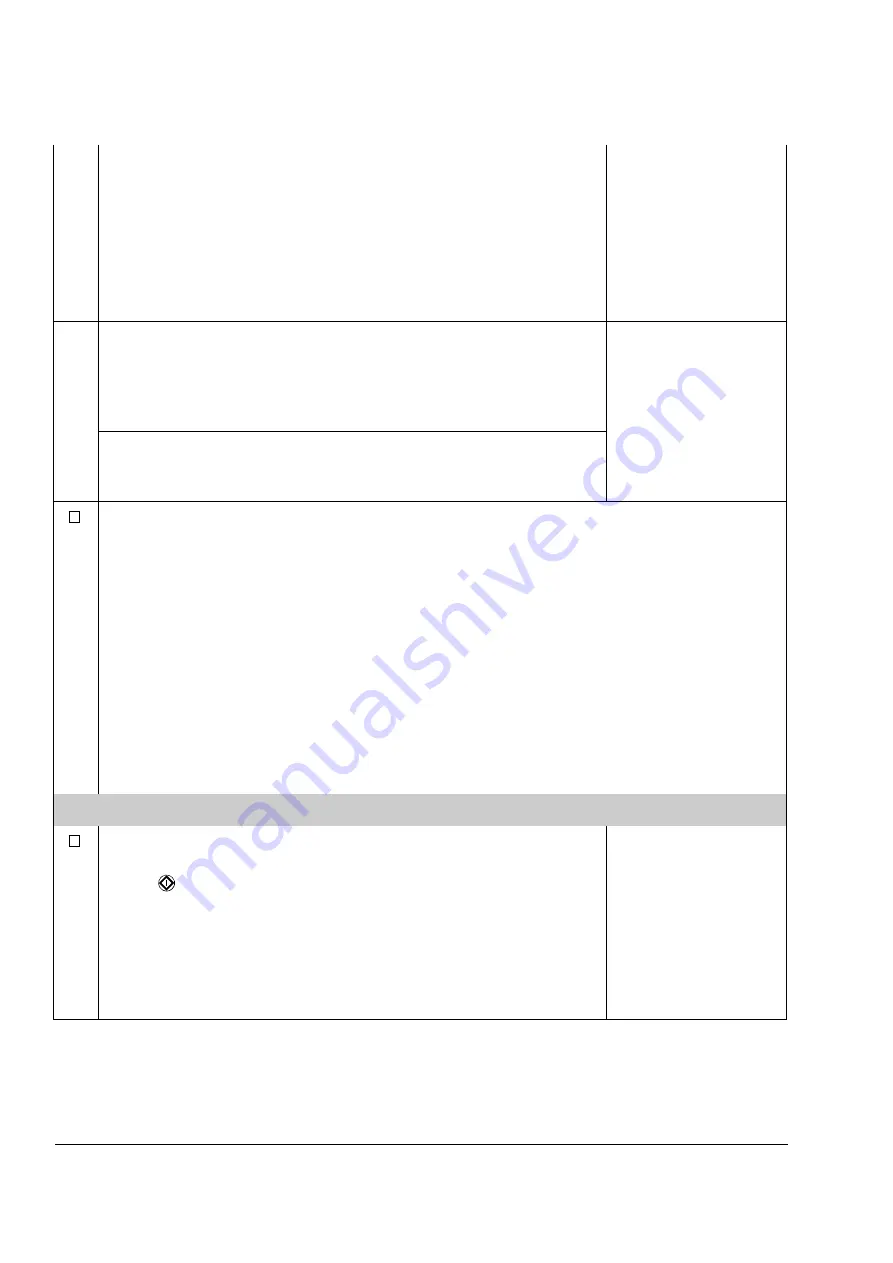
Start-up and control through the I/O interface
20
When the motor data has been entered, two displays (warning and
information) start to alternate. Move to next step without pressing
any key.
1 -> 0.0 rpm O
ACS800
** WARNING **
ID MAGN REQ
1 L-> 0.0 rpm I
*** Information ***
Press green button
to start ID MAGN
Note:
The POWER ON acknowledge (DI_L) must be active
(closed) before the drive is ready to continue with the next steps.
The drive is ready when “0” appears in the upper right corner of the
control panel display. For more information, see section
acknowledge and internal fault reset
on page
.
Note:
The mechanical brake is controlled as default from the RMIO
board relay output RO1. For more information, see section
Select the motor identification method.
The default value ID MAGN (ID Magnetisation) is suitable for most applications. It is applied
in this basic start-up procedure. If your selection is ID Magnetisation, move to next step
without pressing any key.
The ID run (STANDARD) should be selected if:
- the operation point is near zero speed, and/or
- operation at torque range above the motor nominal torque within a wide speed range and
without any measured speed feedback is required.
Note:
If STANDARD ID run is selected, the brake is opened when the Start command is
given and remains open until the STANDARD ID run is completed. If ID MAGN is selected,
the brake is kept closed during the ID run sequence.
If your selection is ID run, continue by following the separate instructions given a few pages
ahead in section
IDENTIFICATION MAGNETISATION (with Motor ID run selection ID MAGN)
Press the
LOC/REM
key to change to local control (L shown on the
first row).
Press
to start the identification magnetisation. The motor is
magnetised at zero speed for 20 to 60 s. Three warnings are
displayed:
The first warning is displayed when the magnetisation starts.
The second warning is displayed while the magnetisation is on.
The third warning is displayed after the magnetisation is completed.
1 L -> 1242.0 rpm I
** WARNING **
MOTOR STARTS
1 L-> 0.0 rpm I
** WARNING **
ID MAGN
1 L-> 0.0 rpm O
** WARNING **
ID DONE
Summary of Contents for ACS 800 Series
Page 1: ...ACS800 Firmware Manual Crane Control Program N697 ...
Page 4: ......
Page 26: ...Start up and control through the I O interface 26 ...
Page 36: ...Quick start up guide 36 ...
Page 52: ...Control panel 52 ...
Page 105: ...Program features 105 Figure Control diagram for Shaft synchronisation executed in 20 ms ...
Page 128: ...Program features 128 ...
Page 150: ...Application macros control location EXT1 EXT2 150 ...
Page 228: ...Actual signals and parameters 228 ...
Page 299: ...Adaptive Programming examples for crane control 299 ...
Page 305: ...Adaptive Programming examples for crane control 305 ...
Page 318: ...Analogue Extension Module 318 ...
Page 332: ...Additional data actual signals and parameters 332 ...
Page 334: ...DriveWindow 334 ...
Page 335: ...Control block diagrams 335 Control block diagrams ...
Page 336: ...Control block diagrams 336 ...
Page 337: ...Control block diagrams 337 ...
Page 338: ...Control block diagrams 338 ...
Page 340: ...www abb com drives www abb com drivespartners Contact us 3AFE68775230 Rev E EN 2012 09 25 ...