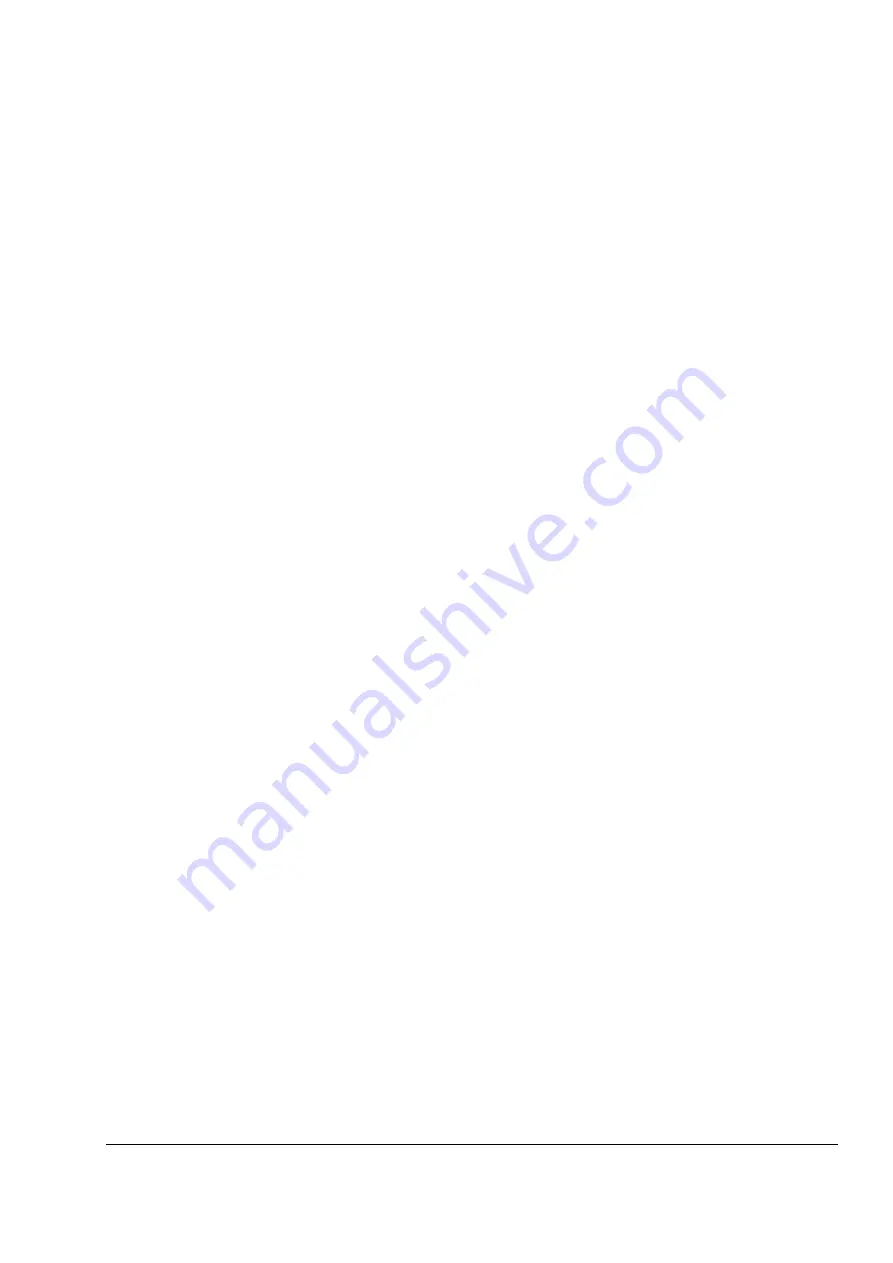
Quick start-up guide
31
• Select the acceleration/deceleration function (Par.
).
• Set the acceleration times (Par.
,
• Set the deceleration times (Par.
Brake control configuration
This section explains how the brake control configuration has to be done.
Checklist for the brake control configuration
• Select the brake control (Par.
• Select the brake acknowledge function (Par.
• Set brake open and close delays (Par.
).
• Set the brake closing speed (Par.
).
• Select the brake fault function (Par.
• Select Torque proving (Par.
).
• Set the torque prove fault delay (Par.
• Select start torque reference (Par.
,
• Set the motor slip speed (Par.
).
• Set the slip fault delay (Par.
).
• Set the brake long flt delay (Par.
• Set the brake reopen delay (Par.
• Set the brake chopper if it is used (group 27).
See section
for more information.
Master/Follower configuration
This section explains how to configure the drive as a Master or a Follower. A
maximum of four Followers can be configured on a Master drive using the CH 2
communication link. The Master/Follower configuration has to be used with EXT2
control. If the Master/Follower configuration is used with EXT1 control, the drive acts
as a stand-alone drive.
Checklist for Master/Follower configuration
• Switch off the power from the drives to be configured as Master/Follower, and
build the optic fibre link using the communication channel 2. The link should be
made in a ring topology.
• Switch on the power for the drive.
• Select the drive as a Master or a Follower (Par.
Set the following parameters in the Master drive.
• Select the control location as EXT2 (Par.
• Select the drive as a Master (Par.
).
Summary of Contents for ACS 800 Series
Page 1: ...ACS800 Firmware Manual Crane Control Program N697 ...
Page 4: ......
Page 26: ...Start up and control through the I O interface 26 ...
Page 36: ...Quick start up guide 36 ...
Page 52: ...Control panel 52 ...
Page 105: ...Program features 105 Figure Control diagram for Shaft synchronisation executed in 20 ms ...
Page 128: ...Program features 128 ...
Page 150: ...Application macros control location EXT1 EXT2 150 ...
Page 228: ...Actual signals and parameters 228 ...
Page 299: ...Adaptive Programming examples for crane control 299 ...
Page 305: ...Adaptive Programming examples for crane control 305 ...
Page 318: ...Analogue Extension Module 318 ...
Page 332: ...Additional data actual signals and parameters 332 ...
Page 334: ...DriveWindow 334 ...
Page 335: ...Control block diagrams 335 Control block diagrams ...
Page 336: ...Control block diagrams 336 ...
Page 337: ...Control block diagrams 337 ...
Page 338: ...Control block diagrams 338 ...
Page 340: ...www abb com drives www abb com drivespartners Contact us 3AFE68775230 Rev E EN 2012 09 25 ...