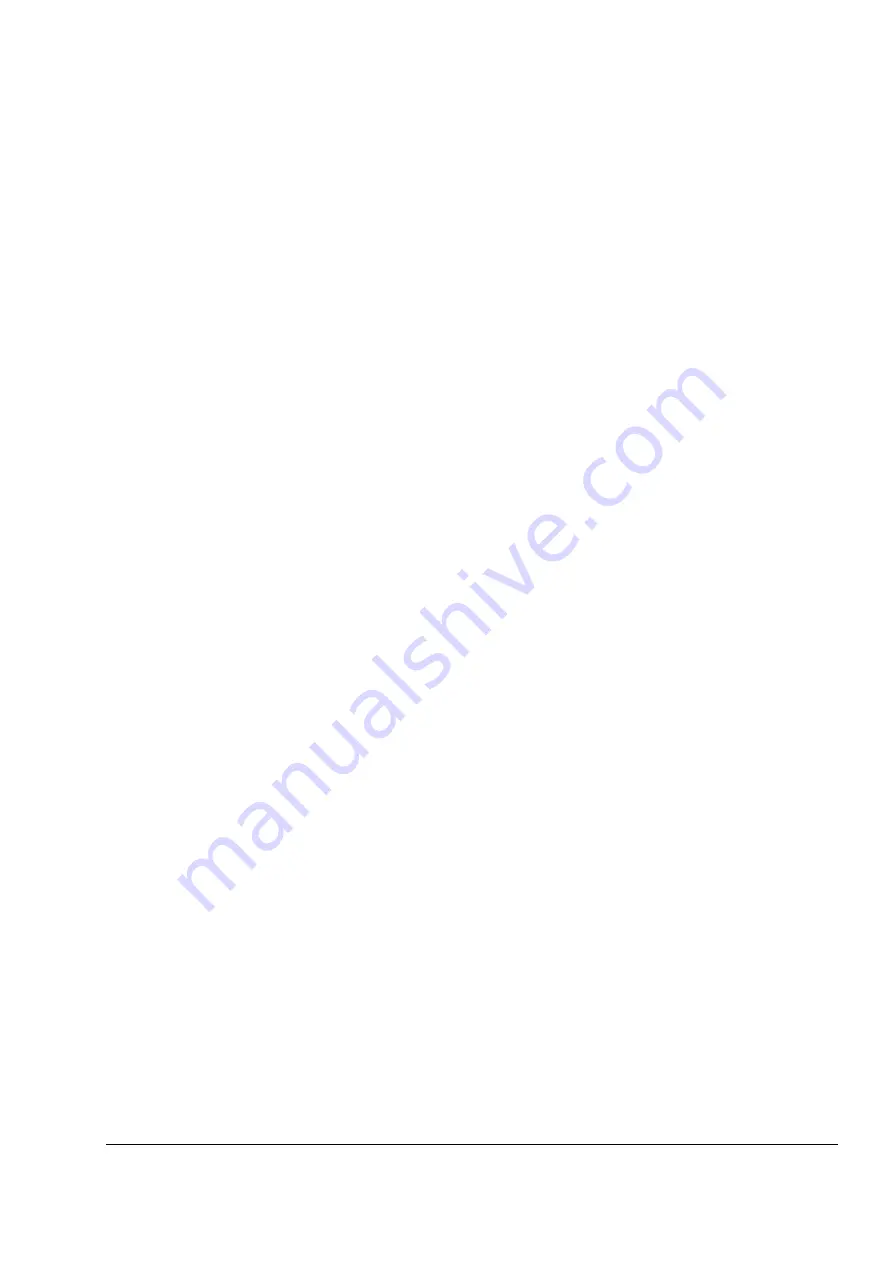
Adaptive Programming examples for crane control
301
Brake match
Brake match detects mechanical brake slips and downward movement of the load
when Mechanical brake control is in use, the operator has given the stop command
and the target is to close the brake. The slip detection is based on the motor encoder
position signal, and the function works only if an encoder is used. You can use the
function for an automatic restart of the crane or just for a warning (alarm) indication.
Working logic
The logic checks whether the motor is rotating when the mechanical brake should be
closed. The rotation is detected by comparing two successive position signal
samples (
POS ACT PPU). Therefore, the system needs to be equipped with a
pulse encoder. The logic works during the normal Stop command, extended run
time, and also, when the drive is in the standby (spare unit) mode.
If the position differs between the two successive samples more than set with
parameter
CONSTANT1, and the motor torque is less than the preset value,
Brake match is activated. By means of pointer parameter
ZERO SPEED PTR,
the drive will start with a zero speed reference, and a brake match warning is shown
on the control panel and in the fault logger. You can reset the warning by giving a
new start command: DI1 forward or DI2 reverse. While brake match is active, the
mechanical brake open command is prevented.
For Brake match to work, you need to connect the output of AP block number 10 to
hidden parameter
ZERO SPEED PTR. You can open group 97 by entering
pass code 5600 into parameter
PASS CODE.
The following figures present an example AP file solution for Brake match.
Note:
When creating the actual AP files, you must be pay attention to safety issues
and carefully check the logic case by case.
Summary of Contents for ACS 800 Series
Page 1: ...ACS800 Firmware Manual Crane Control Program N697 ...
Page 4: ......
Page 26: ...Start up and control through the I O interface 26 ...
Page 36: ...Quick start up guide 36 ...
Page 52: ...Control panel 52 ...
Page 105: ...Program features 105 Figure Control diagram for Shaft synchronisation executed in 20 ms ...
Page 128: ...Program features 128 ...
Page 150: ...Application macros control location EXT1 EXT2 150 ...
Page 228: ...Actual signals and parameters 228 ...
Page 299: ...Adaptive Programming examples for crane control 299 ...
Page 305: ...Adaptive Programming examples for crane control 305 ...
Page 318: ...Analogue Extension Module 318 ...
Page 332: ...Additional data actual signals and parameters 332 ...
Page 334: ...DriveWindow 334 ...
Page 335: ...Control block diagrams 335 Control block diagrams ...
Page 336: ...Control block diagrams 336 ...
Page 337: ...Control block diagrams 337 ...
Page 338: ...Control block diagrams 338 ...
Page 340: ...www abb com drives www abb com drivespartners Contact us 3AFE68775230 Rev E EN 2012 09 25 ...