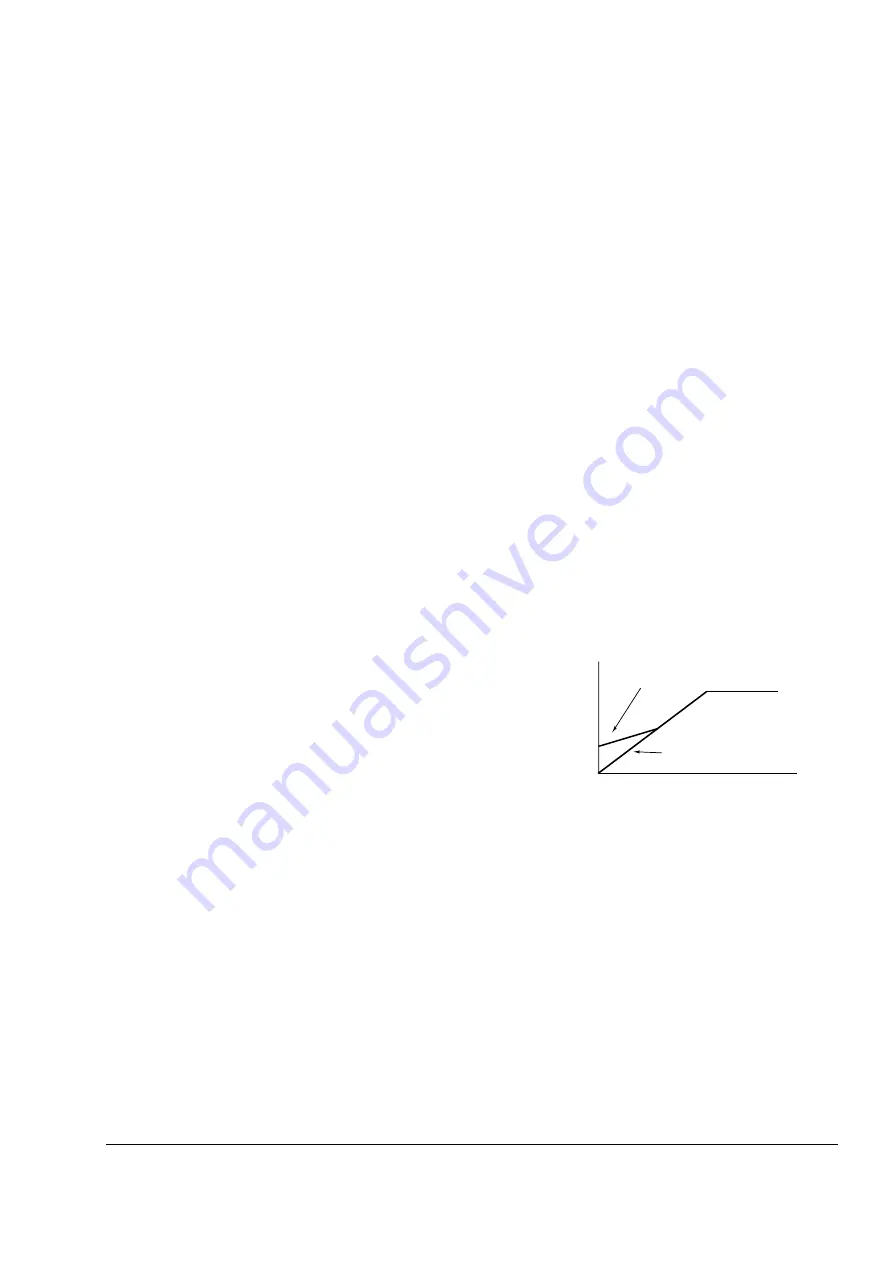
Program features
73
Scalar control
It is possible to select Scalar control as the motor control method instead of Direct
torque control (DTC). In the Scalar control mode, the drive is controlled with a
frequency reference. The outstanding performance of the default motor control
method, Direct torque control, is not achieved in Scalar control.
It is recommended to activate the Scalar control mode in the following special
applications:
• In multimotor drives: 1) if the load is not equally shared between the motors, 2) if
the motors are of different sizes, or 3) if the motors are going to be changed after
the motor identification
• If the nominal current of the motor is less than 1/6 of the nominal output current of
the drive
• If the drive is used without a motor connected (for example, for test purposes)
• The drive runs a medium voltage motor via a step-up transformer.
In the Scalar control mode, some standard features are not available.
Settings
Parameter
.
IR compensation for a scalar-controlled drive
IR compensation is active only when the motor
control mode is Scalar (see section
on page
. When IR compensation is activated,
the drive gives an extra voltage boost to the
motor at low speeds. IR compensation is useful in
applications that require high breakaway torque.
In Direct torque control, no IR compensation is
possible/needed.
Settings
Parameter
.
f
(Hz)
Motor Voltage
No compensation
IR compensation
Summary of Contents for ACS 800 Series
Page 1: ...ACS800 Firmware Manual Crane Control Program N697 ...
Page 4: ......
Page 26: ...Start up and control through the I O interface 26 ...
Page 36: ...Quick start up guide 36 ...
Page 52: ...Control panel 52 ...
Page 105: ...Program features 105 Figure Control diagram for Shaft synchronisation executed in 20 ms ...
Page 128: ...Program features 128 ...
Page 150: ...Application macros control location EXT1 EXT2 150 ...
Page 228: ...Actual signals and parameters 228 ...
Page 299: ...Adaptive Programming examples for crane control 299 ...
Page 305: ...Adaptive Programming examples for crane control 305 ...
Page 318: ...Analogue Extension Module 318 ...
Page 332: ...Additional data actual signals and parameters 332 ...
Page 334: ...DriveWindow 334 ...
Page 335: ...Control block diagrams 335 Control block diagrams ...
Page 336: ...Control block diagrams 336 ...
Page 337: ...Control block diagrams 337 ...
Page 338: ...Control block diagrams 338 ...
Page 340: ...www abb com drives www abb com drivespartners Contact us 3AFE68775230 Rev E EN 2012 09 25 ...