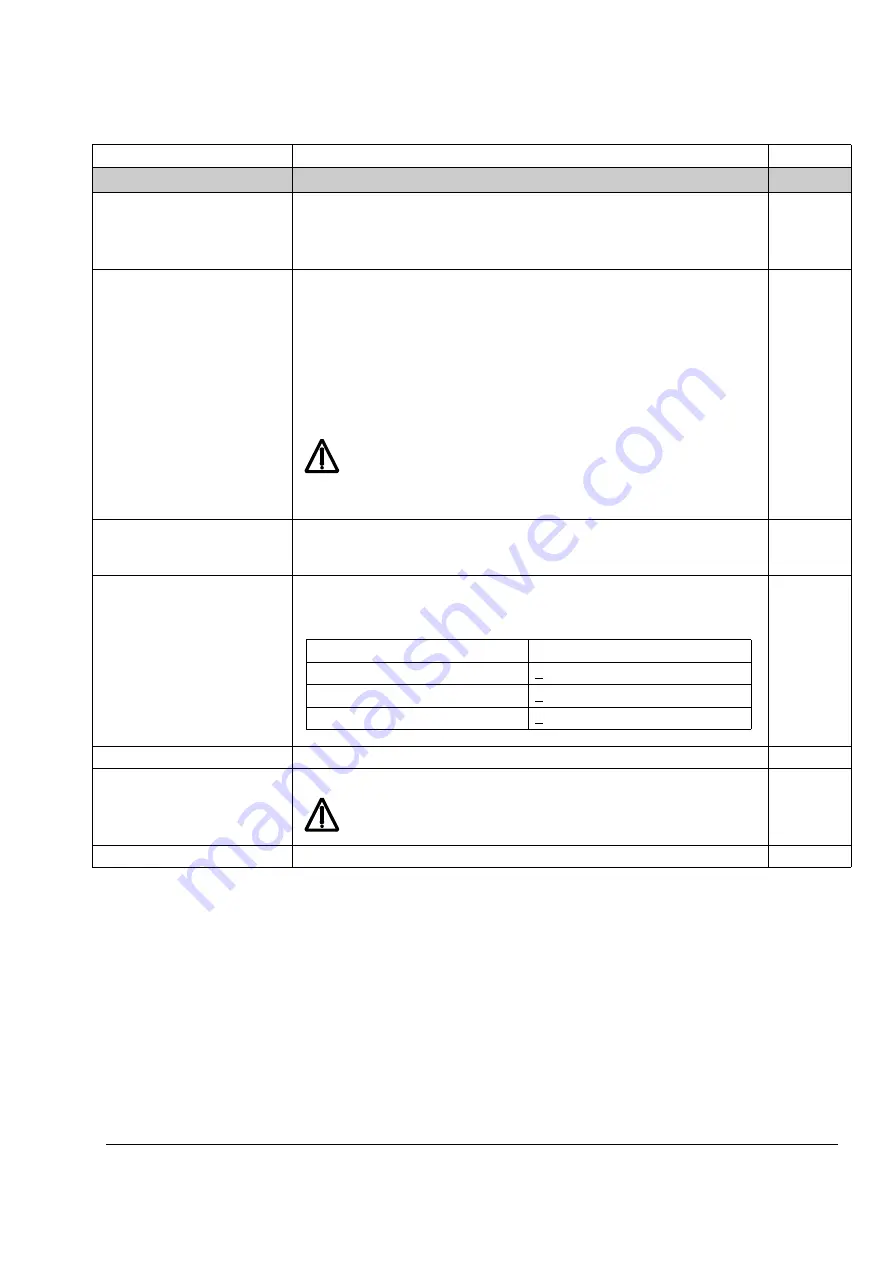
Actual signals and parameters
177
21 START/STOP
Start and stop modes of the motor.
21.01
START FUNCTION
Selects the motor starting method.
In special crane applications like slew-motion cranes, its possible to enable the
auto start function mode. For more information, contact your local ABB
representative.
CNST DC MAGN
In the crane applications, this parameter is fixed to CNST DC MAGN. Constant
DC magnetising is needed when constant pre-magnetising time is required
(For example, if the motor start must be simultaneous with a mechanical brake
release). CNST DC MAGN also guarantees the highest possible break-away
torque when the pre-magnetising time is set long enough. The pre-magnetising
time is defined with parameter
.
Note:
Starting to a rotating machine is not possible when DC magnetising is
selected.
Note:
DC magnetising cannot be selected if parameter
= SCALAR.
WARNING!
The drive will start after the set magnetising time has
passed although the motor magnetisation is not completed. Ensure
always in applications where a full break-away torque is essential, that
the constant magnetising time is long enough to allow generation of full
magnetisation and torque.
3
21.02
CONST MAGN TIME
Defines the magnetising time in the constant magnetising mode. See
parameter
. After the Start command, the drive automatically pre-
magnetises the motor the set time.
30.0 … 10000.0 ms
Magnetising time. To ensure full magnetising, set this value to the same value
as or higher than the rotor time constant. If not known, use the rule-of-thumb
value given in the table below:
30 … 10000
21.03
STOP FUNCTION
Selects the motor stop function.
COAST
Stop by cutting of the motor power supply. The motor coasts to a stop.
WARNING!
If the mechanical brake control function is on, the
application program uses ramp stop in spite of the selection COAST
(see parameter group
).
1
RAMP
Stop along a ramp. See parameter group
.
2
Index
Name/Selection
Description
FbEq
Motor Rated Power
Constant Magnetising Time
< 10 kW
> 100 to 200 ms
10 to 200 kW
> 200 to 1000 ms
200 to 1000 kW
> 1000 to 2000 ms
Summary of Contents for ACS 800 Series
Page 1: ...ACS800 Firmware Manual Crane Control Program N697 ...
Page 4: ......
Page 26: ...Start up and control through the I O interface 26 ...
Page 36: ...Quick start up guide 36 ...
Page 52: ...Control panel 52 ...
Page 105: ...Program features 105 Figure Control diagram for Shaft synchronisation executed in 20 ms ...
Page 128: ...Program features 128 ...
Page 150: ...Application macros control location EXT1 EXT2 150 ...
Page 228: ...Actual signals and parameters 228 ...
Page 299: ...Adaptive Programming examples for crane control 299 ...
Page 305: ...Adaptive Programming examples for crane control 305 ...
Page 318: ...Analogue Extension Module 318 ...
Page 332: ...Additional data actual signals and parameters 332 ...
Page 334: ...DriveWindow 334 ...
Page 335: ...Control block diagrams 335 Control block diagrams ...
Page 336: ...Control block diagrams 336 ...
Page 337: ...Control block diagrams 337 ...
Page 338: ...Control block diagrams 338 ...
Page 340: ...www abb com drives www abb com drivespartners Contact us 3AFE68775230 Rev E EN 2012 09 25 ...