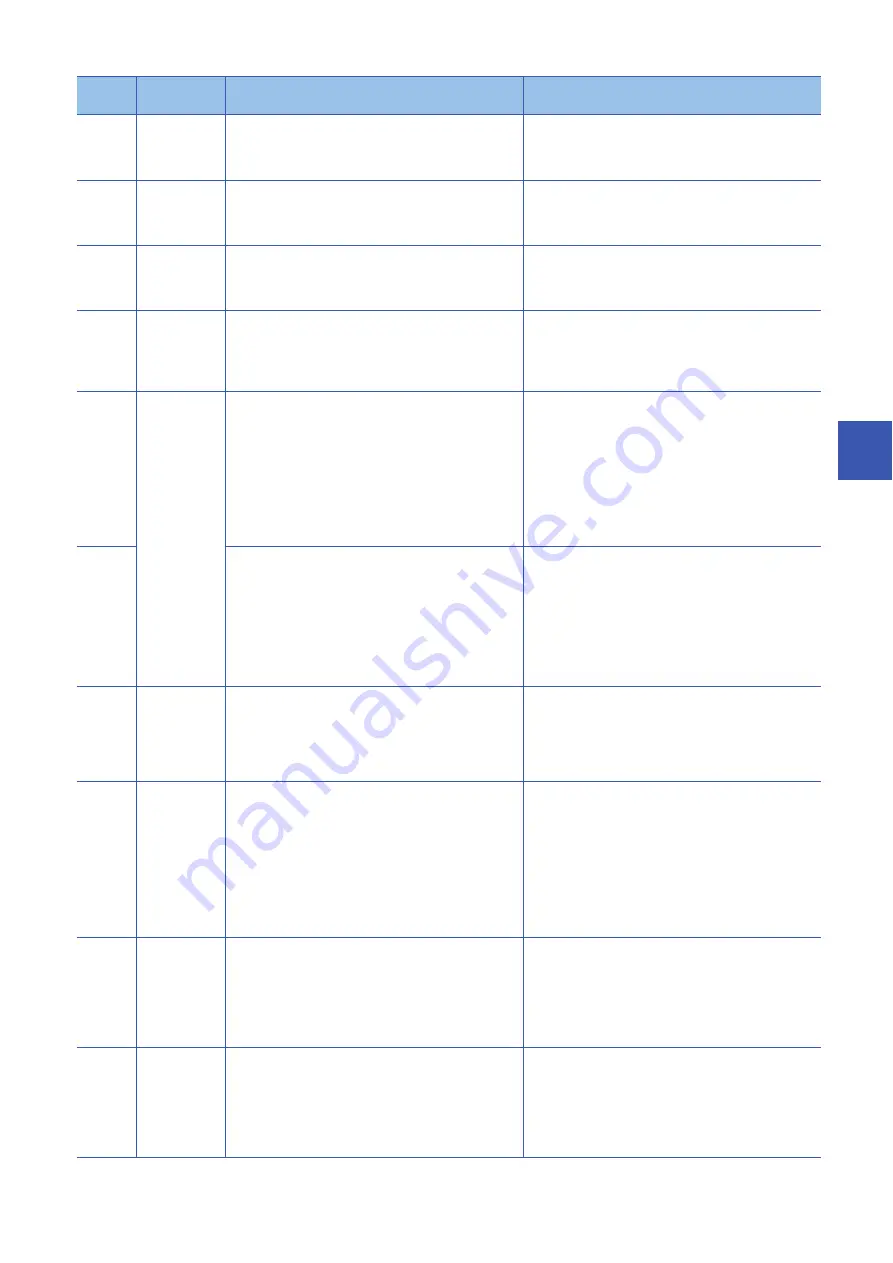
14 TROUBLESHOOTING
14.5 List of Error Codes
533
14
19A0H
M code ON
signal ON start
The positioning has been performed while M code ON signal
[X4, X5, X6, X7] is on.
[Operation of when the error has occurred]
The operation is not performed.
Start the positioning after M code ON signal [X4, X5, X6, X7]
has turned off. For details, refer to
19A1H
PLC READY
OFF start
The positioning has been performed while PLC READY signal
[Y0] is off.
[Operation of when the error has occurred]
The operation is not performed.
Check the program with which PLC READY signal [Y0] is
turned on or off and start the positioning after PLC READY
signal [Y0] is turned on.
19A2H
READY OFF
start
The positioning has been performed while RD75 READY
signal [X0] is off.
[Operation of when the error has occurred]
The operation is not performed.
Start the positioning after RD75 READY signal [X0] has
turned on.
19A3H
Outside start
No. range
At the positioning start, the setting value of Positioning start
No. of axis control data is other than 1 to 600, 7000 to 7004,
and 9001 to 9004.
[Operation of when the error has occurred]
The operation is not performed.
Correct the value of the positioning start No. For details, refer
to
Page 470 [Cd.3] Positioning start No..
19A4H
Illegal setting of
ABS direction in
unit of degree
A value outside the setting range is set in [Cd.40] ABS
direction in degrees when the software stroke limit is invalid
and the unit is degree.
[Operation of when the error has occurred]
■
At the start of operation
The operation is not performed.
■
During operation
The operation stops according to the setting of [Pr.39] Stop
group 3 sudden stop selection of detailed parameter 2
(deceleration stop/sudden stop).
Correct the value in [Cd.40] ABS direction in degrees within
the setting range. For details, refer to
19A5H
A value other than 0 is set in [Cd.40] ABS direction in degrees
when the software stroke limit is valid and the unit is degree.
[Operation of when the error has occurred]
■
At the start of operation
The operation is not performed.
■
During operation
The operation stops according to the setting of [Pr.39] Stop
group 3 sudden stop selection of detailed parameter 2
(deceleration stop/sudden stop).
• Set 0 in [Cd.40] ABS direction in degrees. For details, refer
to
Page 482 [Cd.40] ABS direction in degrees.
• Invalidate the software stroke limit. (The stroke limit is
invalidated when Software stroke limit upper limit value =
Software stroke limit lower limit value.)
19A6H
Start error at
OPR completion
The positioning has been performed with OPR request flag
being on when 0: Do not execute the positioning control is set
in [Pr.58] Setting of operation during uncompleted OPR.
[Operation of when the error has occurred]
The operation is not performed.
• Start the positioning after OPR is completed.
• For the system where positioning control is possible with
OPR request flag being on, set 1 to [Pr.58] Setting of
operation during uncompleted OPR. For details, refer to
Page 419 [Pr.58] Setting of operation during
19F0H
Illegal condition
data No.
The positioning of block start using condition data has been
performed by the special start instruction (condition start, wait
start, simultaneous start, repeated start (FOR condition))
when the condition data No. is outside the setting range. (1
Condition data No.
10)
[Operation of when the error has occurred]
■
At the start of operation
The operation is not performed.
■
During operation
The operation ends.
Correct the condition data No. For details, refer to
19F1H
Error before
simultaneous
start
The partner axis for the simultaneous start of block start is in
BUSY state.
[Operation of when the error has occurred]
■
At the start of operation
The operation is not performed.
■
During operation
The operation ends.
• Correct the condition operator. For details, refer to
Page 440 [Da.16] Condition operator.
• Start the operation after BUSY state of the simultaneous
starting axis is cleared.
19F2H
Special start
instruction error
The special start instruction is not corresponding to the
operation.
[Operation of when the error has occurred]
■
At the start of operation
The operation is not performed.
■
During operation
The operation ends.
Correct the special start instruction. For details, refer to
Page 437 [Da.13] Special start instruction.
Error
code
Error name
Cause and description
Action
Содержание MELSEC iQ-R RD75P4
Страница 1: ...MELSEC iQ R Positioning Module User s Manual Application RD75P2 RD75P4 RD75D2 RD75D4 ...
Страница 2: ......
Страница 13: ...11 MEMO ...
Страница 19: ...17 CONTENTS INDEX 588 REVISIONS 592 WARRANTY 593 TRADEMARKS 594 ...
Страница 498: ...496 13 PROGRAMMING 13 2 List of Labels Used ...
Страница 503: ...13 PROGRAMMING 13 4 Program Example 501 13 ...
Страница 511: ...13 PROGRAMMING 13 4 Program Example 509 13 Torque change program Step operation program Skip program ...
Страница 512: ...510 13 PROGRAMMING 13 4 Program Example Teaching program Continuous operation interrupt program ...
Страница 513: ...13 PROGRAMMING 13 4 Program Example 511 13 Target position change program Absolute position restoration program ...
Страница 514: ...512 13 PROGRAMMING 13 4 Program Example Restart program Parameter data initialization program ...
Страница 515: ...13 PROGRAMMING 13 4 Program Example 513 13 Flash ROM write program Error reset program ...
Страница 516: ...514 13 PROGRAMMING 13 4 Program Example Stop program ...
Страница 565: ...APPENDICES Appendix 4 Operation Examples of When the Remote Head Module Is Mounted 563 A ...
Страница 568: ...566 APPENDICES Appendix 4 Operation Examples of When the Remote Head Module Is Mounted Common program ...
Страница 584: ...582 APPENDICES Appendix 4 Operation Examples of When the Remote Head Module Is Mounted Restart program ...
Страница 587: ...APPENDICES Appendix 4 Operation Examples of When the Remote Head Module Is Mounted 585 A Stop program ...
Страница 597: ......