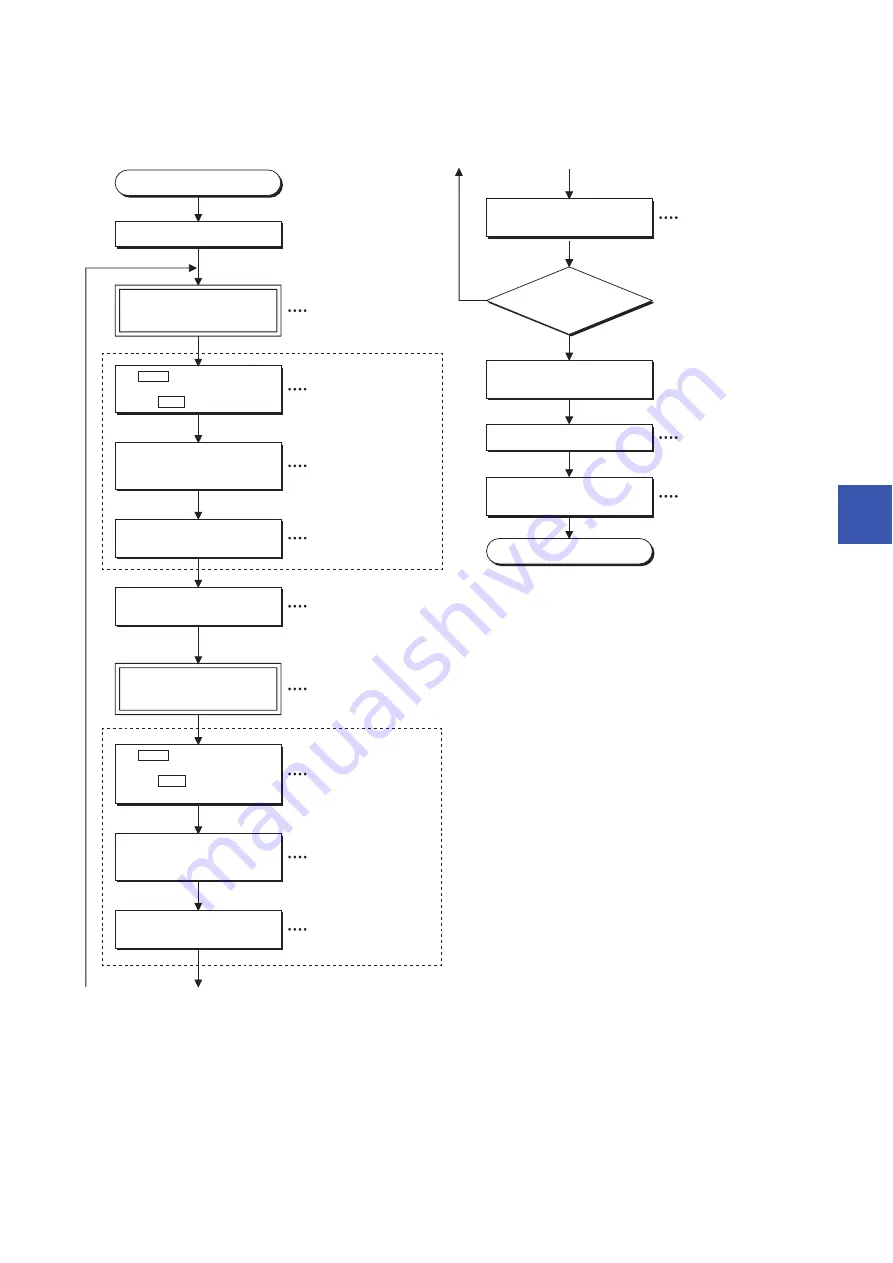
7 CONTROL SUB FUNCTIONS
7.9 Other Functions
287
7
■
When the teaching is first performed for [Da.7] Arc address and successively performed for
[Da.6] Positioning address/movement amount (example for the 2-axis circular interpolation
control with a sub point specified on the axis 1 and 2)
YES
NO
(1)
(2)
(1)
(2)
Start
Perform machine OPR on axis 1
and axis 2.
Move the object to the sub point
of circular interpolation with
a manual operation.
*1
Set Cd.38 Teaching data
selection to write the current feed
value to Da.7 Arc address.
Set the positioning data No.
where the teaching is carried out.
Using a JOG operation,
inching operation, or manual
pulse generator operation.
Set 1 in the buffer memory
address [1548].
Set the positioning data
No. in the buffer memory
address [1549].
Check that the teaching is
completed.
Check that 0 is set
in the buffer memory
address [1549].
Carry out the teaching of arc sub
point address on axis 2.
Use the buffer memory addresses
[1648] and [1649], and follow
the same procedure with axis 1.
Move the object to the end point
of circular interpolation with
a manual operation.
*2
Using a JOG operation,
inching operation, or manual
pulse generator operation.
Set Cd.38 Teaching data
selection to write the current feed
value to Da.6 Positioning
address/movement amount.
Set 0 in the buffer memory
address [1548].
Set the positioning data No.
where the teaching is carried out.
Set the positioning data
No. in the buffer memory
address [1549].
Check that the teaching is
completed.
Check that 0 is set
in the buffer memory
address [1549].
Teaching of arc sub point address on axis 1
Teaching of arc end point address on axis 1
End the teaching?
Turn off PLC READY signal [Y0].
Perform the module data backup.
End
Check that the module data
backup is completed.
Carry out the teaching of arc sub
point address on axis 2.
Use the buffer memory
addresses [1648] and
[1649], and follow
the same procedure
with axis 1.
Set 1 in the buffer memory
address [1900].
Check that 0 is set
in the buffer memory
address [1900].
Содержание MELSEC iQ-R RD75P4
Страница 1: ...MELSEC iQ R Positioning Module User s Manual Application RD75P2 RD75P4 RD75D2 RD75D4 ...
Страница 2: ......
Страница 13: ...11 MEMO ...
Страница 19: ...17 CONTENTS INDEX 588 REVISIONS 592 WARRANTY 593 TRADEMARKS 594 ...
Страница 498: ...496 13 PROGRAMMING 13 2 List of Labels Used ...
Страница 503: ...13 PROGRAMMING 13 4 Program Example 501 13 ...
Страница 511: ...13 PROGRAMMING 13 4 Program Example 509 13 Torque change program Step operation program Skip program ...
Страница 512: ...510 13 PROGRAMMING 13 4 Program Example Teaching program Continuous operation interrupt program ...
Страница 513: ...13 PROGRAMMING 13 4 Program Example 511 13 Target position change program Absolute position restoration program ...
Страница 514: ...512 13 PROGRAMMING 13 4 Program Example Restart program Parameter data initialization program ...
Страница 515: ...13 PROGRAMMING 13 4 Program Example 513 13 Flash ROM write program Error reset program ...
Страница 516: ...514 13 PROGRAMMING 13 4 Program Example Stop program ...
Страница 565: ...APPENDICES Appendix 4 Operation Examples of When the Remote Head Module Is Mounted 563 A ...
Страница 568: ...566 APPENDICES Appendix 4 Operation Examples of When the Remote Head Module Is Mounted Common program ...
Страница 584: ...582 APPENDICES Appendix 4 Operation Examples of When the Remote Head Module Is Mounted Restart program ...
Страница 587: ...APPENDICES Appendix 4 Operation Examples of When the Remote Head Module Is Mounted 585 A Stop program ...
Страница 597: ......