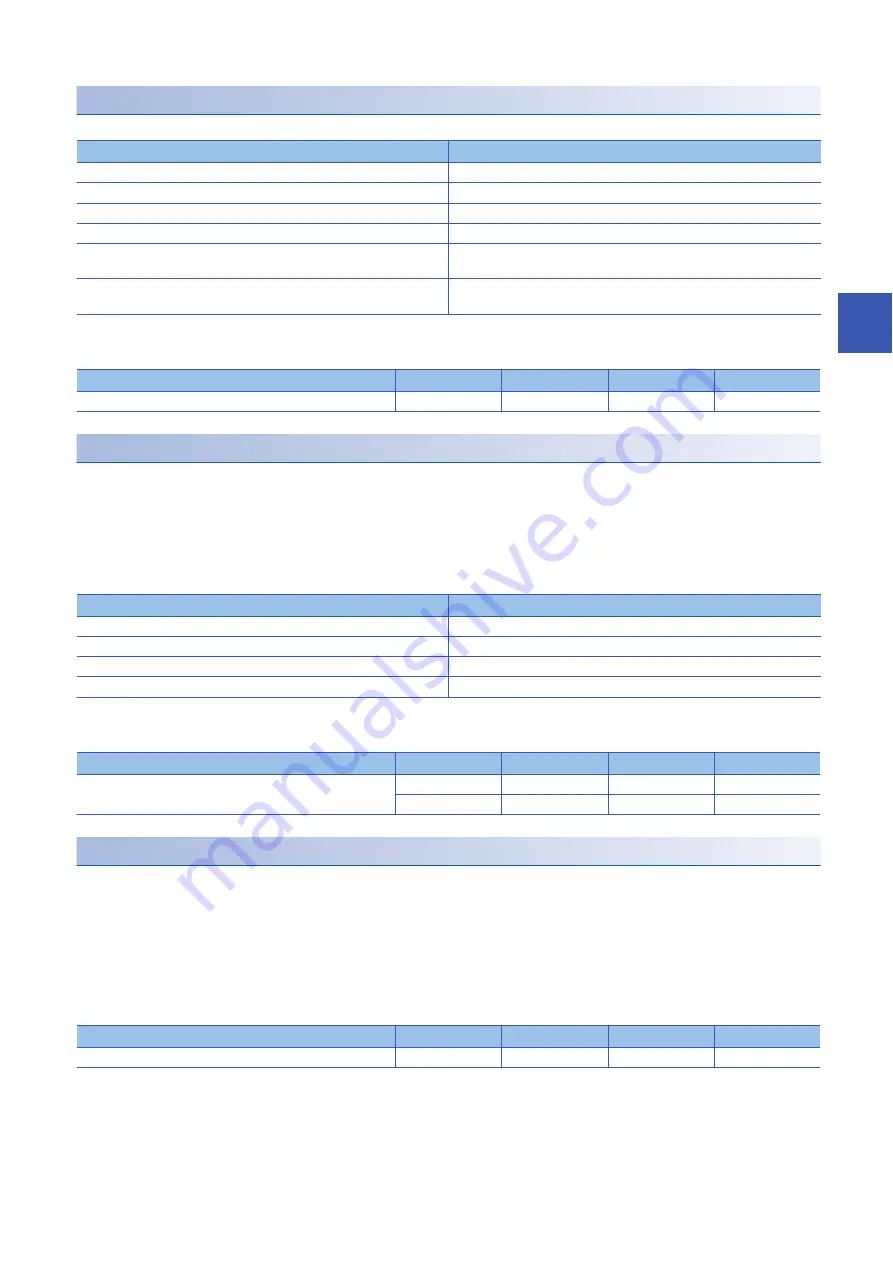
12 DATA USED FOR POSITIONING CONTROL
12.7 Monitor Data
461
12
[Md.64] Positioning control complete factor
This area stores the complete factor of OPR control and major positioning control.
■
Buffer memory address
The following table shows the buffer memory address of this area.
[Md.34] Movement amount after near-point dog ON
• This area stores 0 when machine OPR starts.
• After machine OPR starts, the movement amount from the near-point dog ON to the machine OPR completion is stored.
The movement amount indicates the amount machine to OPR completion using near-point dog ON as 0. The OP shift
amount is excluded.
• For the stopper method 1, 2, or 3, 0 is always stored.
Multiplying the stored value by the following converted value enables the monitoring of the converted value in each unit.
■
Buffer memory address
The following table shows the buffer memory address of this area.
[Md.35] Torque limit stored value
This area stores the value set in [Pr.17] Torque limit setting value or [Cd.22] New torque value.
• During positioning start, JOG operation start, manual pulse generator operation (when [Cd.21] Manual pulse generator
enable flag is turned on), the value set in [Pr.17] Torque limit setting value is stored.
• When a value other than 0 is set in [Cd.22] New torque value, the value set in [Cd.22] New torque value is stored.
• When the creep speed is reached with the OPR, the value set in [Pr.54] OPR torque limit value is stored.
■
Buffer memory address
The following table shows the buffer memory address of this area.
Positioning control end cause
Stored value
Operation does not start after power-on or operation is being performed
0
Normal completion (Positioning control is completed correctly)
1
Normal completion (Positioning control is completed by a stop signal)
2
Normal completion (Positioning control is completed by the external stop)
3
Error completion (Positioning control is completed by an error occurrence at
start)
4
Error completion (Positioning control is completed by an error occurrence
during an operation)
5
Buffer memory name
Axis 1
Axis 2
Axis 3
Axis 4
[Md.64] Positioning control complete factor
823
923
1023
1123
Unit
Converted value
m
10
-1
inch
10
-5
degree
10
-5
pulse
1
Buffer memory name
Axis 1
Axis 2
Axis 3
Axis 4
[Md.34] Movement amount after near-point dog ON
824
924
1024
1124
825
925
1025
1125
Buffer memory name
Axis 1
Axis 2
Axis 3
Axis 4
[Md.35] Torque limit stored value
826
926
1026
1126
Содержание MELSEC iQ-R RD75P4
Страница 1: ...MELSEC iQ R Positioning Module User s Manual Application RD75P2 RD75P4 RD75D2 RD75D4 ...
Страница 2: ......
Страница 13: ...11 MEMO ...
Страница 19: ...17 CONTENTS INDEX 588 REVISIONS 592 WARRANTY 593 TRADEMARKS 594 ...
Страница 498: ...496 13 PROGRAMMING 13 2 List of Labels Used ...
Страница 503: ...13 PROGRAMMING 13 4 Program Example 501 13 ...
Страница 511: ...13 PROGRAMMING 13 4 Program Example 509 13 Torque change program Step operation program Skip program ...
Страница 512: ...510 13 PROGRAMMING 13 4 Program Example Teaching program Continuous operation interrupt program ...
Страница 513: ...13 PROGRAMMING 13 4 Program Example 511 13 Target position change program Absolute position restoration program ...
Страница 514: ...512 13 PROGRAMMING 13 4 Program Example Restart program Parameter data initialization program ...
Страница 515: ...13 PROGRAMMING 13 4 Program Example 513 13 Flash ROM write program Error reset program ...
Страница 516: ...514 13 PROGRAMMING 13 4 Program Example Stop program ...
Страница 565: ...APPENDICES Appendix 4 Operation Examples of When the Remote Head Module Is Mounted 563 A ...
Страница 568: ...566 APPENDICES Appendix 4 Operation Examples of When the Remote Head Module Is Mounted Common program ...
Страница 584: ...582 APPENDICES Appendix 4 Operation Examples of When the Remote Head Module Is Mounted Restart program ...
Страница 587: ...APPENDICES Appendix 4 Operation Examples of When the Remote Head Module Is Mounted 585 A Stop program ...
Страница 597: ......