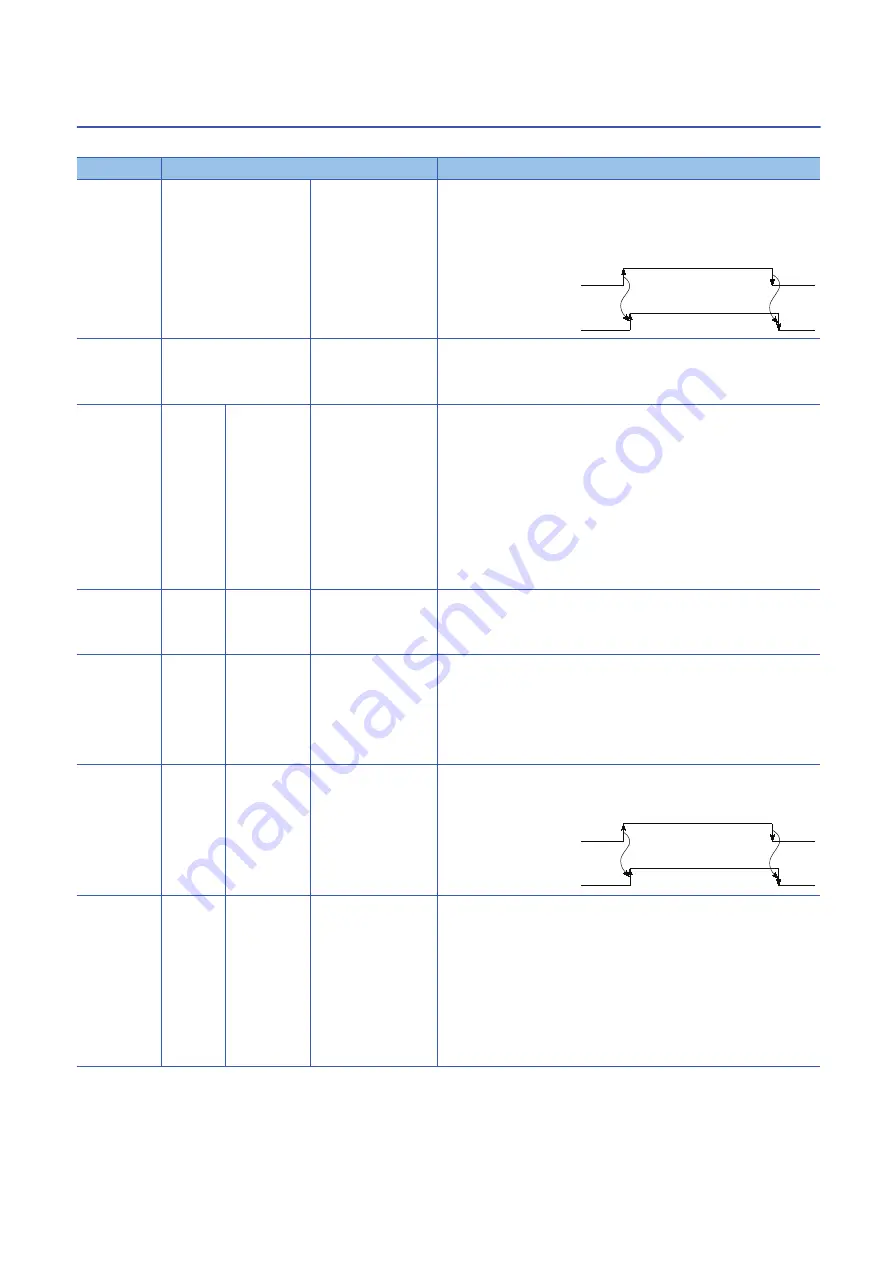
344
11 SPECIFICATIONS OF I/O SIGNALS WITH CPU MODULE
11.2 Details of Input Signals
11.2
Details of Input Signals
The following tables shows the ON/OFF timing and conditions of the input signals.
*1 BUSY signal turns on even when the position control of a movement amount 0 is executed. However, since the ON time is short, the ON
status may not be detected in the program.
*2 Positioning complete of the RD75 refers to the point when the pulse output from the RD75 is completed. Thus, even if Positioning
complete signal of the RD75 turns on, the system may continue operation.
Device No.
Signal name
Description
X0
RD75 READY signal
On: READY
Off: Not READY/
Watchdog timer
error
• When PLC READY signal [Y0] is turned off and on, the parameter setting
range is checked. If no error is found, this signal turns on.
• When PLC READY signal [Y0] is turned off, this signal turns off.
• When a watchdog timer error occurs, this signal turns off.
• This signal is used for interlock in a program and others.
X1
Module access flag
Off: Module access
disabled
On: Module access
enabled
• After the CPU module is set to RUN, this signal turns on with the status that
allows the access from the CPU module to the RD75. This signal turns off
while the CPU module is in the STOP status.
• This signal is used for interlock in a program and others.
X4
X5
X6
X7
Axis 1
Axis 2
Axis 3
Axis 4
M code ON
Off: M code is not set
On: M code is set
• In the WITH mode, this signal turns on when the positioning data operation is
started. In the AFTER mode, this signal turns on when the positioning data
operation is completed.
• This signal turns off with [Cd.7] M code ON signal OFF request.
• When no M code is specified (When [Da.10] M code is 0), this signal remains
off.
• With using continuous path control for the positioning operation, the
positioning continues even when this signal does not turn off. However, M
code ON signal ON (Warning code: 0992H) will occur.
• When PLC READY signal [Y0] is turned off, this signal also turns off. If the
operation is started while the M code is on, M code ON signal ON start (Error
code: 19A0H) will occur.
X8
X9
XA
XB
Axis 1
Axis 2
Axis 3
Axis 4
Error detection
Off: No error
On: Error occurrence
• This signal turns on when an error occurs, and turns off when the error is reset
on [Cd.5] Axis error reset.
XC
XD
XE
XF
Axis 1
Axis 2
Axis 3
Axis 4
BUSY
Off: Not BUSY
On: BUSY
• This signal turns on at the start of the positioning, OPR, or JOG operation.
This signal turns off when the time set in [Da.9] Dwell time has passed after
the positioning operation stops. (This signal remains on during positioning.)
• This signal turns off when the positioning is stopped with step operation.
• During manual pulse generator operation, this signal turns on while [Cd.21]
Manual pulse generator enable flag is on.
• This signal turns off at error completion or positioning stop.
X10
X11
X12
X13
Axis 1
Axis 2
Axis 3
Axis 4
Start complete
Off: Start incomplete
On: Start complete
• This signal turns on when the RD75 starts the positioning processing since
Positioning start signal is turned on. (Start complete signal also turns on
during OPR control.)
X14
X15
X16
X17
Axis 1
Axis 2
Axis 3
Axis 4
Positioning
complete
Off: Positioning
incomplete
On: Positioning
complete
• This signal turns on for the time set in [Pr.40] Positioning complete signal
output time from the instant when the positioning control for each positioning
data No. is completed. For the interpolation control, Positioning complete
signal of the interpolation axis turns on for the time set to the reference axis.
(This signal does not turn on when [Pr.40] Positioning complete signal output
time is 0.)
• This signal will turn off if the positioning (including OPR), JOG operation,
inching operation, or manual pulse generator operation is started while this
signal is on.
• This signal will not turn on when the speed control or positioning is canceled
midway.
OFF
ON
OFF
ON
PLC READY signal [Y0]
RD75 READY signal [X0]
OFF
ON
OFF
ON
Positioning start signal [Y10]
Start complete signal [X10]
Содержание MELSEC iQ-R RD75P4
Страница 1: ...MELSEC iQ R Positioning Module User s Manual Application RD75P2 RD75P4 RD75D2 RD75D4 ...
Страница 2: ......
Страница 13: ...11 MEMO ...
Страница 19: ...17 CONTENTS INDEX 588 REVISIONS 592 WARRANTY 593 TRADEMARKS 594 ...
Страница 498: ...496 13 PROGRAMMING 13 2 List of Labels Used ...
Страница 503: ...13 PROGRAMMING 13 4 Program Example 501 13 ...
Страница 511: ...13 PROGRAMMING 13 4 Program Example 509 13 Torque change program Step operation program Skip program ...
Страница 512: ...510 13 PROGRAMMING 13 4 Program Example Teaching program Continuous operation interrupt program ...
Страница 513: ...13 PROGRAMMING 13 4 Program Example 511 13 Target position change program Absolute position restoration program ...
Страница 514: ...512 13 PROGRAMMING 13 4 Program Example Restart program Parameter data initialization program ...
Страница 515: ...13 PROGRAMMING 13 4 Program Example 513 13 Flash ROM write program Error reset program ...
Страница 516: ...514 13 PROGRAMMING 13 4 Program Example Stop program ...
Страница 565: ...APPENDICES Appendix 4 Operation Examples of When the Remote Head Module Is Mounted 563 A ...
Страница 568: ...566 APPENDICES Appendix 4 Operation Examples of When the Remote Head Module Is Mounted Common program ...
Страница 584: ...582 APPENDICES Appendix 4 Operation Examples of When the Remote Head Module Is Mounted Restart program ...
Страница 587: ...APPENDICES Appendix 4 Operation Examples of When the Remote Head Module Is Mounted 585 A Stop program ...
Страница 597: ......