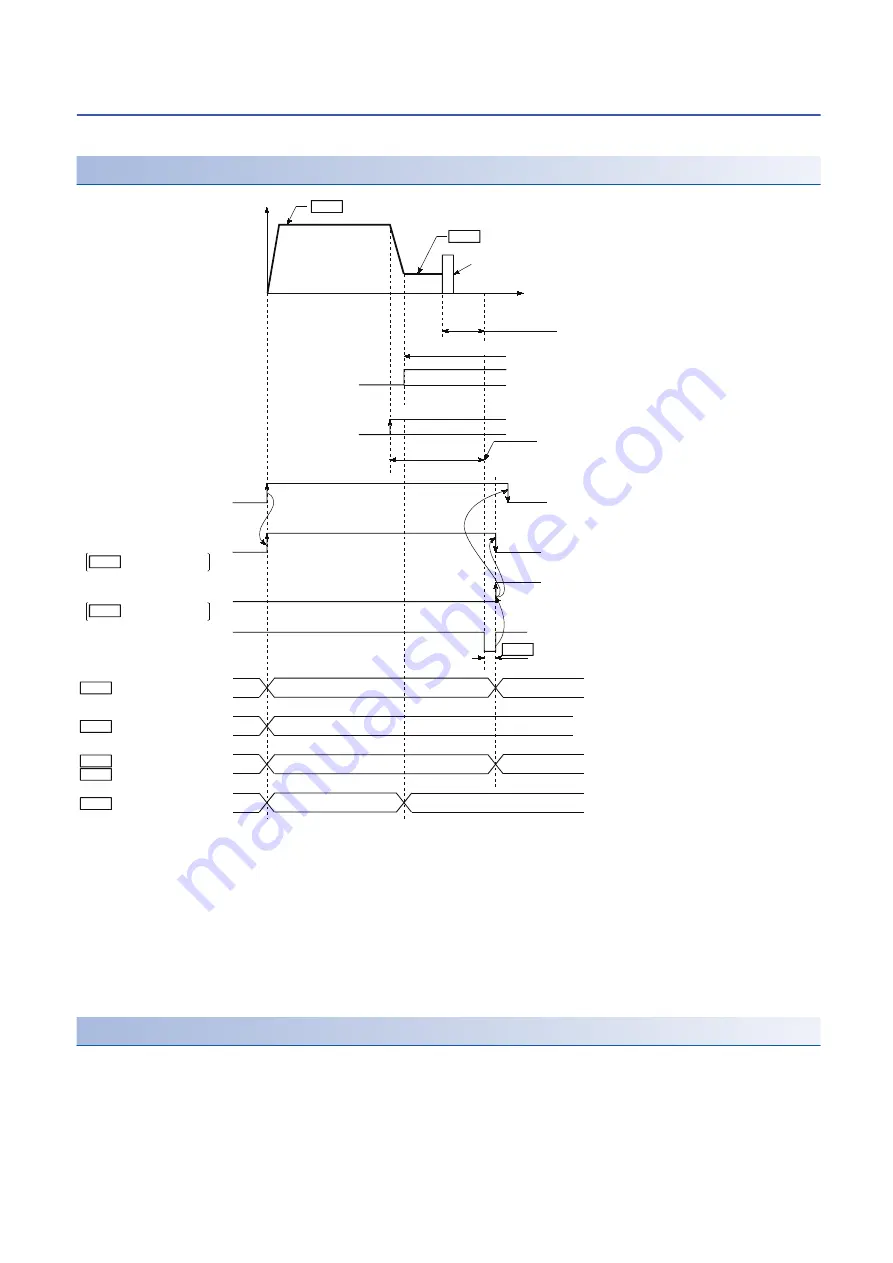
44
2 OPR CONTROL
2.2 Machine OPR
Stopper method 1
The following shows an operation overview of the stopper method 1, one of the OPR methods.
Operation chart
Restrictions
Always limit the servomotor torque after the speed reaches the speed set in [Pr.47] Creep speed.
Otherwise the servomotor may be damaged when the workpiece hits to the stopper. (
Page 232 Torque limit function)
(1) The machine OPR is started.
(The machine starts accelerating according to the setting of [Pr.51] OPR acceleration time selection in the direction specified in [Pr.44] OPR direction, and
moves at the speed set in [Pr.46] OPR speed when the acceleration is completed.)
(2) When the on state of the near-point dog is detected, the machine starts decelerating.
(3) The machine decelerates to the speed set in [Pr.47] Creep speed and moves at the creep speed after that.
(The torque must be limited for this operation. Otherwise the servomotor may be damaged in step (4).)
(4) The machine presses the workpiece against the stopper at the creep speed and stops.
(5) When the time set in [Pr.49] OPR dwell time has elapsed after the near-point dog was turned on, the RD75 stops outputting pulses and produces Deviation
counter clear output to the drive unit.
(Deviation counter clear signal output time is set in [Pr.55].)
(6) After Deviation counter clear output is completed, OPR complete flag ([Md.31] Status: b4) turns on and OPR request flag ([Md.31] Status: b3) turns off.
0
t
ON
OFF
ON
OFF
OFF
ON
V
OFF
Pr.46
Pr.47
Md.34
Md.20
Md.21
Md.26
Md.31
Md.31
Pr.55
Md.35
ON
(1)
(2)
(3)
(4)
(5)(6)
Range in which the servomotor rotation is
forcibly stopped with a stopper
Standby
OPR
Standby
Inconsistent
Inconsistent
A value of the movement amount is stored.
OP address
Inconsistent
Torque limit setting value
OPR torque limit value
Current feed value
OPR speed
Creep speed
Stops with a stopper.
Torque limit
OPR request flag
OPR complete flag
Near-point dog
Deviation counter clear output
Machine feed value
Dwell time
measurement
Machine OPR start
(Positioning start signal)
[Y10, Y11, Y12, Y13]
Status: b3
Status: b4
Axis operation status
Movement amount
after near-point dog
ON
Torque limit stored
value
Deviation counter clear signal
output time
Time out of dwell time
Torque limit valid range
Содержание MELSEC iQ-R RD75P4
Страница 1: ...MELSEC iQ R Positioning Module User s Manual Application RD75P2 RD75P4 RD75D2 RD75D4 ...
Страница 2: ......
Страница 13: ...11 MEMO ...
Страница 19: ...17 CONTENTS INDEX 588 REVISIONS 592 WARRANTY 593 TRADEMARKS 594 ...
Страница 498: ...496 13 PROGRAMMING 13 2 List of Labels Used ...
Страница 503: ...13 PROGRAMMING 13 4 Program Example 501 13 ...
Страница 511: ...13 PROGRAMMING 13 4 Program Example 509 13 Torque change program Step operation program Skip program ...
Страница 512: ...510 13 PROGRAMMING 13 4 Program Example Teaching program Continuous operation interrupt program ...
Страница 513: ...13 PROGRAMMING 13 4 Program Example 511 13 Target position change program Absolute position restoration program ...
Страница 514: ...512 13 PROGRAMMING 13 4 Program Example Restart program Parameter data initialization program ...
Страница 515: ...13 PROGRAMMING 13 4 Program Example 513 13 Flash ROM write program Error reset program ...
Страница 516: ...514 13 PROGRAMMING 13 4 Program Example Stop program ...
Страница 565: ...APPENDICES Appendix 4 Operation Examples of When the Remote Head Module Is Mounted 563 A ...
Страница 568: ...566 APPENDICES Appendix 4 Operation Examples of When the Remote Head Module Is Mounted Common program ...
Страница 584: ...582 APPENDICES Appendix 4 Operation Examples of When the Remote Head Module Is Mounted Restart program ...
Страница 587: ...APPENDICES Appendix 4 Operation Examples of When the Remote Head Module Is Mounted 585 A Stop program ...
Страница 597: ......