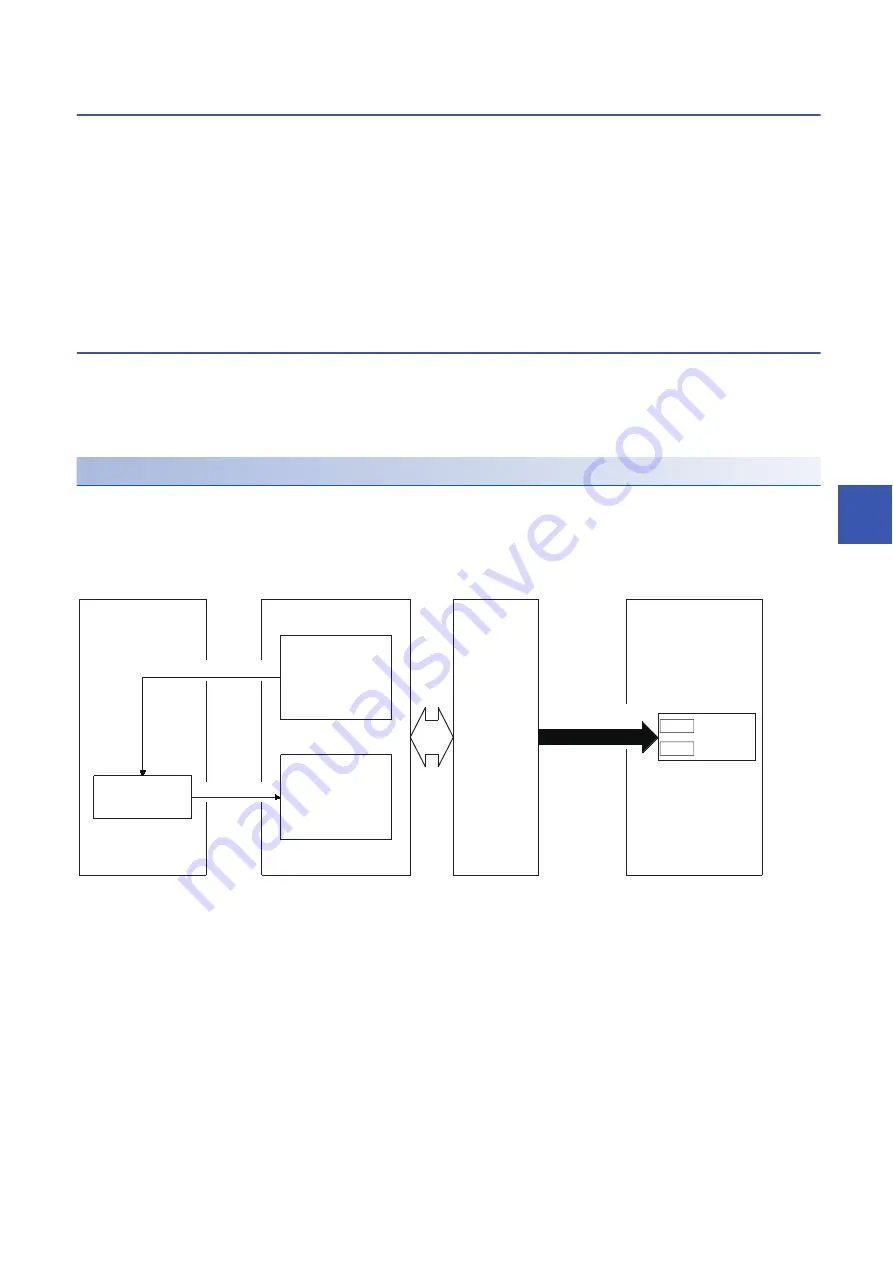
7 CONTROL SUB FUNCTIONS
7.7 Absolute Position Restoration Function
265
7
Overview of the absolute position detection system
The detector comprises an encoder for the detection of position in one rotation in addition to the A, B, and Z phase signals for
the position control in normal operation and an accumulative revolution counter for the detection of the number of rotations.
The absolute position detection system detects the absolute position of the machine constantly and stores it with the backup
of the battery irrespective of the state of the power supply to the programmable controller system. Therefore, once the OP
initial setting is performed at the time of the installation of the machine, no OPR is required even when the power is turned on
later. The restoration of the system can be performed easily even when an instantaneous power failure or an emergency stop
occurs.
In addition, because the absolute position data is backed up by a super capacitor in the detector, the absolute position data
will be hold for a specified time even if a cable is disconnected or broken.
Transmission procedure for absolute position signal
The following figure shows the overview of the absolute position signal transmission procedure between a servo amplifier and
a programmable controller system (CPU module, RD75, and I/O modules).
For details on the communication between the servo amplifier and programmable controller system, refer to the manual for
the servo amplifier used.
Errors during communication
• If a time-out occurs during communication, ABS transmission time out (Error code: 1949H) occurs.
• If transmission data causes a sum error, ABS transmission SUM (Error code: 194AH) occurs.
For corrective actions on errors, refer to the following.
RD75
Md.20
G.ABRST1
G.ABRST2
G.ABRST3
G.ABRST4
Md.21
Servo amplifier
I/O module
CPU module
Current position
data
Absolute position detection request
Data transmission
⋅
⋅
⋅
Servo ON signal
ABS transmission
mode
ABS request
⋅
⋅
⋅
ABS transmission
data ready
ABS bit 0
ABS bit 1
[Dedicated
instruction]
Current position data
Current feed
value
Machine feed
value
Содержание MELSEC iQ-R RD75P4
Страница 1: ...MELSEC iQ R Positioning Module User s Manual Application RD75P2 RD75P4 RD75D2 RD75D4 ...
Страница 2: ......
Страница 13: ...11 MEMO ...
Страница 19: ...17 CONTENTS INDEX 588 REVISIONS 592 WARRANTY 593 TRADEMARKS 594 ...
Страница 498: ...496 13 PROGRAMMING 13 2 List of Labels Used ...
Страница 503: ...13 PROGRAMMING 13 4 Program Example 501 13 ...
Страница 511: ...13 PROGRAMMING 13 4 Program Example 509 13 Torque change program Step operation program Skip program ...
Страница 512: ...510 13 PROGRAMMING 13 4 Program Example Teaching program Continuous operation interrupt program ...
Страница 513: ...13 PROGRAMMING 13 4 Program Example 511 13 Target position change program Absolute position restoration program ...
Страница 514: ...512 13 PROGRAMMING 13 4 Program Example Restart program Parameter data initialization program ...
Страница 515: ...13 PROGRAMMING 13 4 Program Example 513 13 Flash ROM write program Error reset program ...
Страница 516: ...514 13 PROGRAMMING 13 4 Program Example Stop program ...
Страница 565: ...APPENDICES Appendix 4 Operation Examples of When the Remote Head Module Is Mounted 563 A ...
Страница 568: ...566 APPENDICES Appendix 4 Operation Examples of When the Remote Head Module Is Mounted Common program ...
Страница 584: ...582 APPENDICES Appendix 4 Operation Examples of When the Remote Head Module Is Mounted Restart program ...
Страница 587: ...APPENDICES Appendix 4 Operation Examples of When the Remote Head Module Is Mounted 585 A Stop program ...
Страница 597: ......