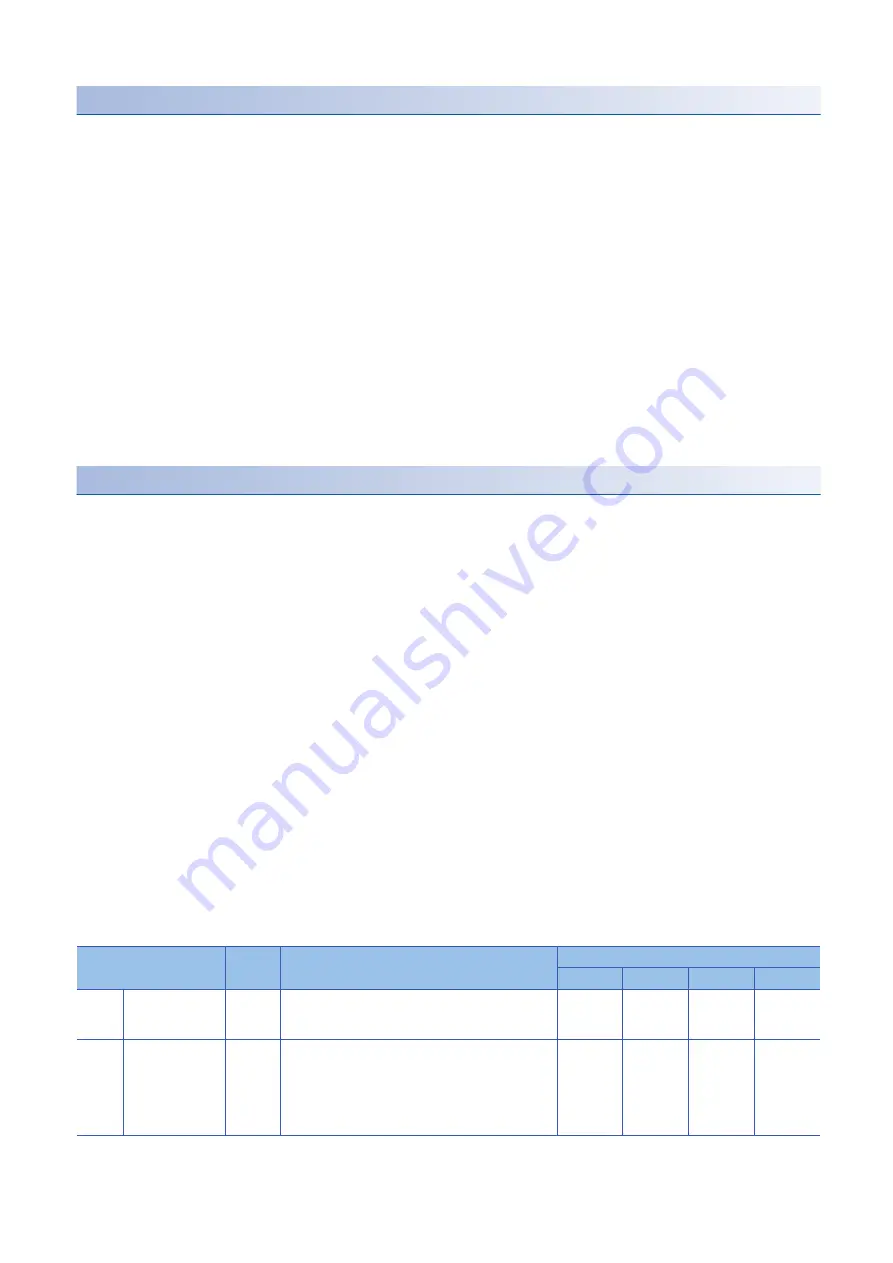
282
7 CONTROL SUB FUNCTIONS
7.9 Other Functions
Control precautions
• During the interpolation control, M code ON signal of the reference axis is turned on.
• M code ON signal will not turn on if 0 is set in [Da.10] M code. The M code will not be output, and the previously output
value will be held in [Md.25] Valid M code.)
• If M code ON signal is on at the positioning start, M code ON signal ON start (Error code: 19A0H) will occur, and the
positioning will not start.
• If PLC READY signal [Y0] is turned off, M code ON signal will turn off and 0 will be stored in [Md.25] Valid M code.
• If the positioning operation time is short in the continuous path control, there will not be enough time to turn off M code ON
signal, and M code ON signal ON (Warning code: 0992H) may occur. To avoid the warning, set 0 in [Da.10] M code of the
positioning data in that section to prevent the M code from being output.
• When the AFTER mode is set in the speed control, the M code is not output and the M code ON signal is not turned on.
• If 9003 is set in [Cd.3] Positioning start No. and the current value change is performed, the M code output function is
disabled.
• If two positioning data, one in the AFTER mode and the other in the WITH mode, are successively executed in the
continuous path control, M code ON signal ON (Warning code: 0992H) occurs when the target data switches from the one
in the AFTER mode to the one in the WITH mode. To avoid the warning, set 0 in [Da.10] M code of the positioning data in
that section to prevent the M code from being output.
Setting method
The following shows the settings required for the M code output function.
■
To specify the M code ON signal output timing separately for each positioning data
To specify the M code ON signal output timing separately for each positioning data, use "[Da.27] M code ON signal output
timing".
The following settings are required to use the parameter.
• Set an M code number in [Da.10] M code, one of the setting items of positioning data.
• Set the timing to output an M code ON signal [X4, X5, X6, X7] in "[Da.27] M code ON signal output timing" of the positioning
data.
■
To specify the same M code ON signal output timing for all positioning data
Set "[Pr.18] M code ON signal output timing". The same M code ON signal output timing can be set for each positioning data
in a batch. When "[Pr.18] M code ON signal output timing" is used, set 0 in "[Da.27] M code ON signal output timing". When a
value other than 0 is set, "[Da.27] M code ON signal output timing" is enabled. (The setting of "[Pr.18] M code ON signal
output timing" is validated at the rising edge (when turned off and on) of PLC READY signal [Y0].)
The following settings are required to use the parameter.
• Set an M code number in [Da.10] M code, one of the setting items of positioning data.
• Set "0: Use the setting value in "[Pr.18] M code ON signal output timing"" (initial value) in "[Da.27] M code ON signal output
timing" of the positioning data.
• Set the timing to output an M code ON signal [X4, X5, X6, X7] in the detailed parameter "[Pr.18] M code ON signal output
timing".
■
Buffer memory are to be used
*1 N indicates the offset address of each positioning data.
N = ((Positioning data No.) - 1)
10
Setting item
Setting
value
Setting detail
Buffer memory address
Axis 1
Axis 2
Axis 3
Axis 4
[Pr.18]
M code ON signal
output timing
Set the output timing of M code ON signal.
0: WITH mode
1: AFTER mode
27
177
327
477
[Da.27]
M code ON signal
output timing
Set the M code ON signal output timing for each
positioning data.
0: Use the set value of "[Pr.18] M code ON signal output
timing"
1: WITH mode
2: AFTER mode
2003+N
(b0 to b1)
8003+N
(b0 to b1)
14003+N
(b0 to b1)
20003+N
(b0 to b1)
Содержание MELSEC iQ-R RD75P4
Страница 1: ...MELSEC iQ R Positioning Module User s Manual Application RD75P2 RD75P4 RD75D2 RD75D4 ...
Страница 2: ......
Страница 13: ...11 MEMO ...
Страница 19: ...17 CONTENTS INDEX 588 REVISIONS 592 WARRANTY 593 TRADEMARKS 594 ...
Страница 498: ...496 13 PROGRAMMING 13 2 List of Labels Used ...
Страница 503: ...13 PROGRAMMING 13 4 Program Example 501 13 ...
Страница 511: ...13 PROGRAMMING 13 4 Program Example 509 13 Torque change program Step operation program Skip program ...
Страница 512: ...510 13 PROGRAMMING 13 4 Program Example Teaching program Continuous operation interrupt program ...
Страница 513: ...13 PROGRAMMING 13 4 Program Example 511 13 Target position change program Absolute position restoration program ...
Страница 514: ...512 13 PROGRAMMING 13 4 Program Example Restart program Parameter data initialization program ...
Страница 515: ...13 PROGRAMMING 13 4 Program Example 513 13 Flash ROM write program Error reset program ...
Страница 516: ...514 13 PROGRAMMING 13 4 Program Example Stop program ...
Страница 565: ...APPENDICES Appendix 4 Operation Examples of When the Remote Head Module Is Mounted 563 A ...
Страница 568: ...566 APPENDICES Appendix 4 Operation Examples of When the Remote Head Module Is Mounted Common program ...
Страница 584: ...582 APPENDICES Appendix 4 Operation Examples of When the Remote Head Module Is Mounted Restart program ...
Страница 587: ...APPENDICES Appendix 4 Operation Examples of When the Remote Head Module Is Mounted 585 A Stop program ...
Страница 597: ......