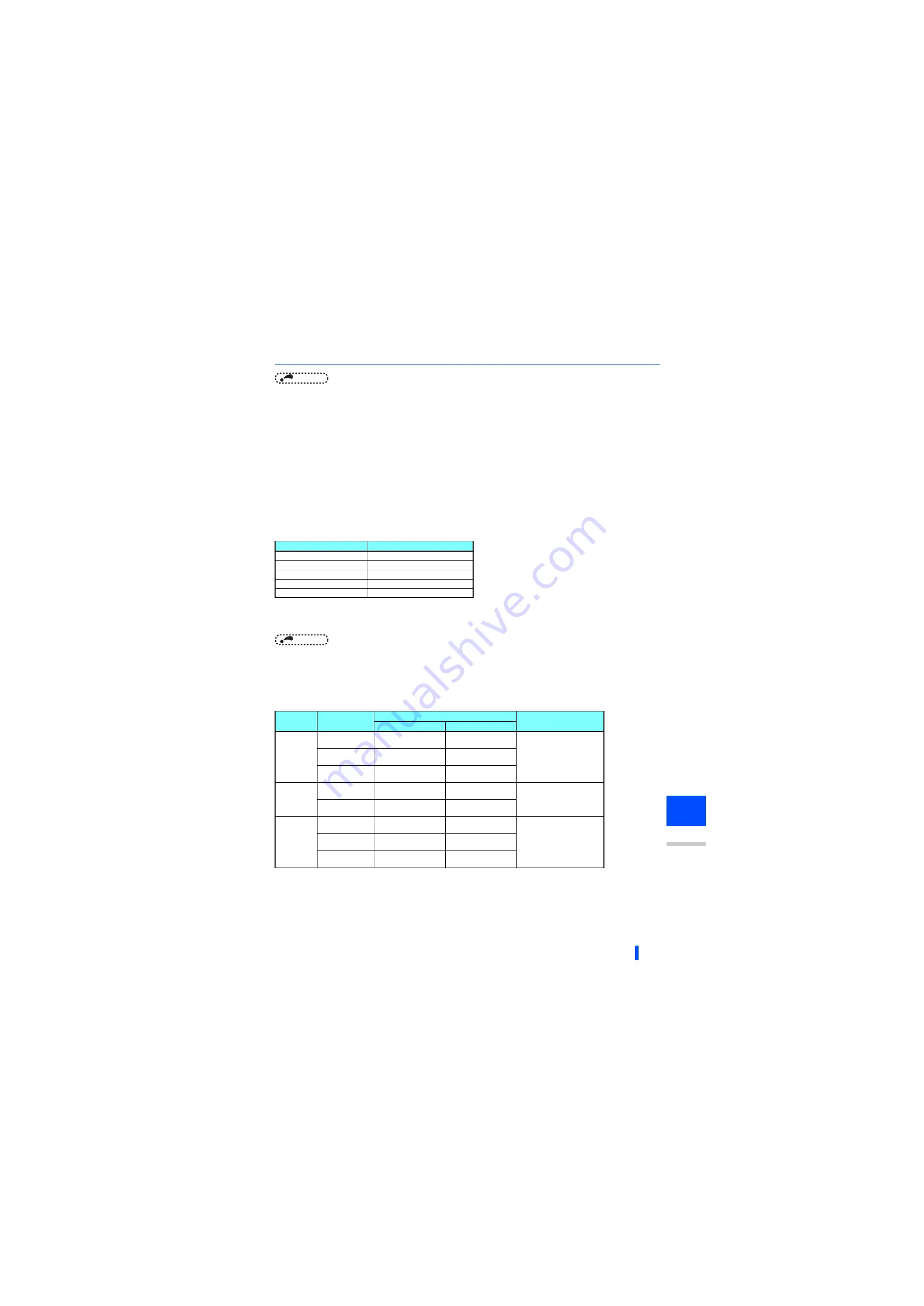
511
5
GROUP
A
NOTE
• When
Pr.128
is set to "0" or the X14 signal is OFF, regular inverter running not dancer control is performed.
• Dancer control is enabled by turning ON/OFF the bits of terminals assigned the X14 signal by RS-485 communication or over
the network.
• When dancer control is selected, set the PID output suspension function (
Pr.575 Output interruption detection time
=
"9999")
• When
Pr.561 PTC thermistor protection level
"9999", terminal 2 cannot be used for the main speed command. Terminal
2 becomes the PTC thermistor input terminal.
Selection of set point/measured value input method (Pr.609, Pr.610)
• Select the set point input method by
Pr.609 PID set point/deviation input selection
and the measured value input method
by
Pr.610 PID measured value input selection
. Switch the power voltage/current specifications of terminals 2 and 4 by
Pr.73 Analog input selection
or
Pr.267 Terminal 4 input selection
to match the specification of the input device.
• When
Pr.133 PID action set point
"9999",
Pr.133
is the set point.
When the set point is set at
Pr.133
, the setting frequency of
Pr.902
is equivalent to 0% and the setting frequency of
Pr.903
is equivalent to 100%.
When the same input method has been selected for the set point and measured value at
Pr.609
and
Pr.610
, set point input is invalid. (Inverter
runs at set point 0%)
CC-Link, CC-Link IE Field Network, or LONWORKS communication is available. For details on communication, refer to the Instruction Manual of
each option.
NOTE
• After changing the
Pr.73
and
Pr.267
settings, check the voltage/current input switch. Incorrect setting may cause a fault,
failure or malfunction. (For the details of the setting, refer to
.)
• When terminals 2 and 4 are selected for deviation input, perform bias calibration using
Pr.902
and
Pr.904
to prevent a minus
voltage from being entered as the deviation input signal. Input of a minus voltage might damage devices and the inverter.
• The following shows the relationship between the input values of the analog input terminals, and the set point and
measured value.
Can be changed by
Pr.73 and Pr.267
and the voltage/current input switch. (Refer to
.)
Pr.609, Pr.610 settings
Input method
1
Terminal 1
2
Terminal 2
3
Terminal 4
4
5
PLC function
Input
terminal
Inspect
specification
Relationship with analog input
Calibration parameter
Set point
Result
Terminal 2
0 to 5 V
0 V=0%
5 V=100%
0 V=0%
5 V=100%
Pr.125, Pr.902, Pr.903
0 to 10 V
0 V=0%
10 V=100%
0 V=0%
10 V=100%
0 to 20 mA
0 mA=0%
20 mA=100%
0 mA=0%
20 mA=100%
Terminal 1
0 to
5 V
-5 V to 0 V=0%
5 V=+100%
-5 V to 0 V=0%
5 V=+100%
When
Pr.128
= "10"
Pr.125, Pr.902, Pr.903
When
Pr.128
"1000"
Pr.917, Pr.918
0 to
10V
-10 V to 0 V=0%
10 V=+100%
-10 V to 0 V=0%
10 V=+100%
Terminal 4
0 to 5 V
0 V to 1 V=0%
5 V=100%
0 V to 1 V=0%
5 V=100%
Pr.126, Pr.904, Pr.905
0 to 10 V
0 V to 2 V=0%
10 V=100%
0 V to 2 V=0%
10 V=100%
0 to 20 mA
0 to 4 mA=0%
20 mA=100%
0 to 4 mA=0%
20 mA=100%
Содержание 800 Series
Страница 11: ...MEMO 10 ...
Страница 17: ...MEMO 16 ...
Страница 95: ...MEMO 94 ...
Страница 671: ...MEMO 670 ...
Страница 681: ...MEMO 680 ...