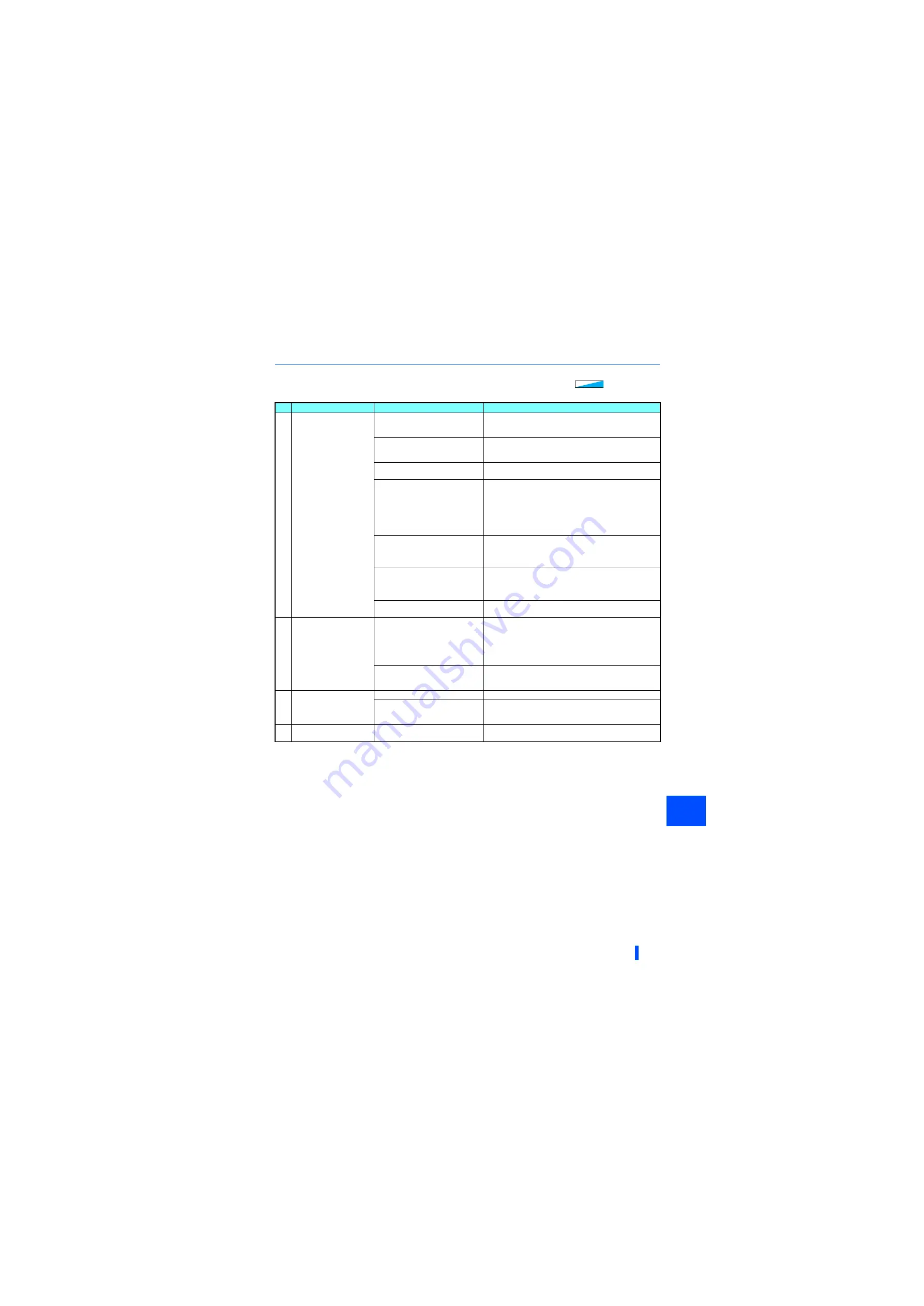
Position control under vector control
237
5
5.5.11
Troubleshooting in position control
Condition
Cause
Countermeasure
1
The motor does not rotate.
There is incorrect phase sequence
between the motor wiring and
encoder wiring.
Check the wiring. (Refer to
Control mode selection setting
Pr.800
Control method selection
is not
appropriate.
Check the
Pr.800
setting. (Refer to
.)
No servo ON or stroke end signals
(STF/STR) are input.
Check if a signal is properly input.
A command pulse or position pulse
sign (NP) is not correctly input.
Check if the command pulse is properly input (check the
accumulated value for command pulses in
Pr.430 Pulse
monitor selection
).
Check the command pulse type in
Pr.428 Command pulse
selection
.
Check that the position pulse sign (NP) is assigned to an input
terminal. (inverter pulse input)
The setting in
Pr.419 Position
command source selection
(position command source selection)
is not correct.
Check the position command source selection in
Pr.419
.
When simple position control by a
point table (
Pr.419
= "0") is used
, the
position feed length set by
Pr.465 to
Pr.494
is not correct.
Check the position feed length in
Pr.465 to Pr.494
.
The option to be used and parameter
settings do not match.
Correctly set
Pr.862 Encoder option selection
according to
the option to be used. (Refer to
2
The position is unfavorably
shifted.
A command pulse is not correctly
input.
Check the command pulse type in
Pr.428 Command pulse
selection
.
Check if the command pulse is properly input (check the
accumulated value of command pulses in
Pr.430
).
Check that the position pulse sign (NP) is assigned to an input
terminal. (inverter pulse input)
The command is affected by noise.
Noise is superpositioned on the
encoder feedback signals.
Set
Pr.72 PWM frequency selection
lower.
Change the earthing (grounding) position of the shielded
cable. Alternatively, do not connect it.
3
Hunting occurs in the motor
or the machine.
Position loop gain is too high.
Set
Pr.422 Position control gain
lower.
Speed loop gain is too high.
Perform easy gain tuning.
Set
Pr.820 Speed control P gain 1
lower and
Pr.821 Speed
control integral time 1
higher.
4
Machine movement is
unstable.
Acceleration/deceleration time
settings are affecting adversely.
Set
Pr.7 Acceleration time and Pr.8 Deceleration time
lower.
Vector
Vector
Vector
Содержание 800 Series
Страница 11: ...MEMO 10 ...
Страница 17: ...MEMO 16 ...
Страница 95: ...MEMO 94 ...
Страница 671: ...MEMO 670 ...
Страница 681: ...MEMO 680 ...